Cement is one of the most essential building materials in modern construction, and transporting it efficiently plays a crucial role in the industry. This article explores cement tankers—what they are, their types, advantages, challenges, and practical tips for optimal use.
What is a Cement Tanker?
A cement tanker is a specialized vehicle designed for transporting bulk cement from production facilities to construction sites or distribution centers. Unlike regular trucks, cement tankers have unique structures that allow them to carry dry and powdered cement without leakage or contamination.
Cement Tanker Overview
- Structure: Cement tankers usually have a cylindrical shape to facilitate the easy flow of powder. They are equipped with pneumatic systems for loading and unloading the cement.
- Materials of Construction: Most cement tankers are made from high-quality steel or aluminum to prevent corrosion and ensure durability.
- Loading Mechanism: Cement tankers often use pneumatic air blowers for loading, allowing for faster and cleaner operations.
- Capacity: These tankers vary in size, typically holding between 25 to 45 tons of cement.
Types of Cement Tankers
Different types of cement tankers serve various purposes in the cement transportation industry:
1. Pneumatic Cement Tankers
Pneumatic tankers utilize compressed air to transport bulk cement. This type is effective in ensuring that the cement remains dust-free and is loaded and unloaded easily.
2. Sliding Floor Cement Tankers
These tankers use a sliding floor to transport cement. The floor moves, pushing the cement towards the discharge point. This type is beneficial for maintaining a constant flow during unloading.
3. Vertical Cement Tankers
Vertical cement tankers are more compact and often used for urban deliveries. They usually have a smaller capacity but offer greater maneuverability in tight spaces.
Comparison Table of Cement Tanker Types
Type | Loading Mechanism | Capacity | Best Use |
---|---|---|---|
Pneumatic | Compressed Air | 25-45 tons | Long-distance transport |
Sliding Floor | Mechanically Driven | 20-30 tons | Continuous unloading |
Vertical | Gravity | 15-25 tons | Urban deliveries |
Advantages of Using Cement Tankers
Utilizing cement tankers presents several benefits to the construction and logistics industry:
1. Efficient Transportation
Cement tankers facilitate the transportation of large quantities of cement in a single trip, reducing the need for multiple shipments and lowering logistical costs.
2. Reduced Material Wastage
Designed for bulk transport, cement tankers minimize spillage and loss of material compared to traditional bagged cement transportation.
3. Versatility in Delivery
The various types of cement tankers allow for versatile applications, whether for long hauls, short urban deliveries, or specialized unloading processes.
Practical Example
A construction company may need to deliver 100 tons of cement. Using pneumatic cement tankers, the company can make two trips with two 50-ton tankers rather than ten trips with smaller trucks, significantly saving time and fuel costs.
Challenges in Cement Transportation
While cement tankers offer numerous advantages, they are also subject to various challenges:
1. Maintenance Costs
Regular maintenance is essential to ensure the efficiency and safety of cement tankers. This can increase operational costs if not managed correctly.
2. Regulatory Compliance
Cement transport is subject to various regulations, including weight limits and safety standards. Non-compliance can result in fines and operational delays.
3. Weather Conditions
Inclement weather can affect transport schedules and safety. Proper planning is necessary to mitigate these risks.
Best Practices for Using Cement Tankers
To maximize the efficiency of cement tankers, consider these best practices:
1. Route Planning
Utilizing route optimization software can help in determining the most efficient paths for deliveries, considering traffic and road conditions.
2. Regular Maintenance Checks
Establish a strict maintenance schedule to ensure tankers are always in good condition. Regular inspections can prevent costly breakdowns.
3. Training for Operators
Ensure that drivers and operators are well-trained in handling cement tankers, including safe loading, unloading, and driving practices.
Tip
Implement safety training programs that highlight the unique challenges associated with transporting bulk materials like cement to improve overall safety and efficiency.
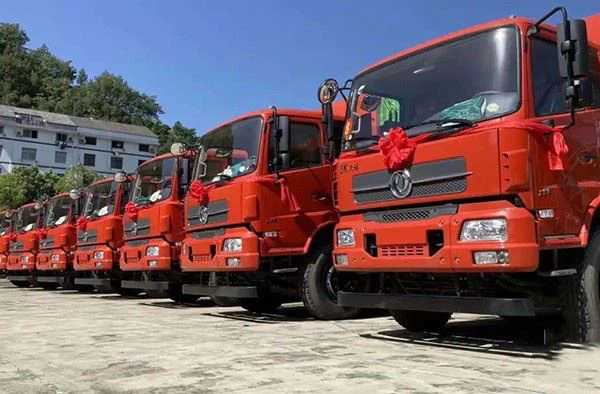
The Future of Cement Tankers
As the construction industry evolves, so will the technology surrounding cement tankers. Innovations are likely to focus on improving efficiency, reducing environmental impact, and enhancing safety:
1. Eco-Friendly Solutions
With the construction industry’s growing focus on sustainability, more manufacturers are exploring eco-friendly materials and designs for cement tankers.
2. Automation and Technology
Advancements in technology may lead to automated loading and unloading systems, further increasing efficiency in cement transportation.
Frequently Asked Questions (FAQs)
1. How much cement can a cement tanker hold?
Cement tankers usually have a capacity ranging from 25 to 45 tons.
2. What materials are cement tankers made from?
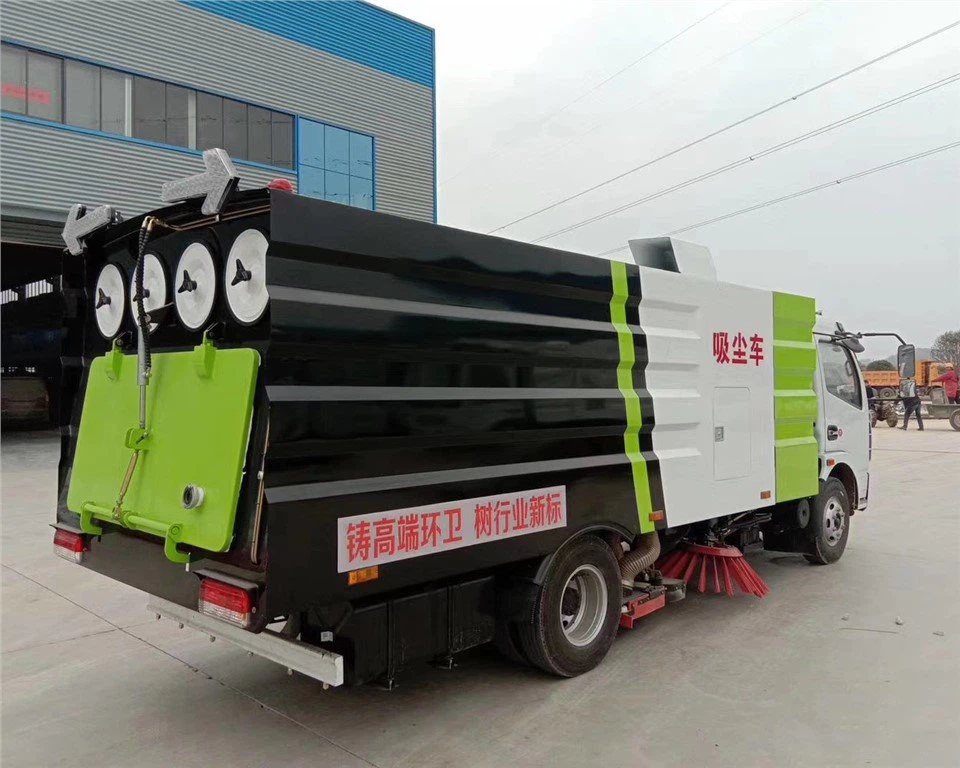
Most cement tankers are constructed from high-quality steel or aluminum to prevent corrosion and ensure long-lasting use.
3. How is cement loaded and unloaded from a tanker?
Cement is typically loaded using a pneumatic system that uses compressed air and is unloaded via gravity or a sliding floor mechanism.
4. What are the safety regulations for transporting cement?
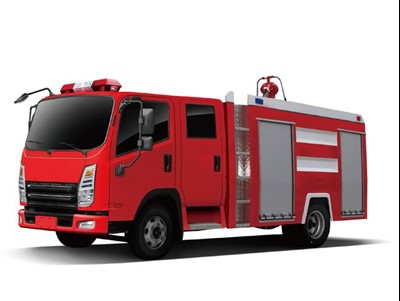
Transporting cement involves compliance with local and national regulations, including weight limits, safety standards, and proper labeling of the cargo.
5. What are the benefits of using bulk cement over bagged cement?
Using bulk cement minimizes transportation costs, reduces waste, and allows for efficient delivery to construction sites.
6. What maintenance practices should be followed for cement tankers?
Regular inspections, routine maintenance like checking for leaks, and ensuring all components are functioning are essential for the optimal performance of cement tankers.