Introduction to CBM Concrete
CBM concrete, standing for Cellular Lightweight Concrete (CLC) or Concrete Block Making, is an innovative material that has garnered attention for its lightweight and insulating properties. This type of concrete is made by incorporating air bubbles into the mix, which significantly reduces its density while maintaining strength. This article aims to provide an in-depth exploration of CBM concrete, focusing on its properties, production methods, applications, and advantages. We will also discuss practical examples and tips for working with CBM concrete, along with a FAQ section addressing common queries.
The Fundamental Properties of CBM Concrete
1. Lightweight Composition
One of the most defining characteristics of CBM concrete is its lightweight nature. The inclusion of air bubbles reduces the overall density of the material, making it easier to handle and transport. Typically, CBM concrete has a density ranging from 300 to 1800 kg/m³, compared to traditional concrete, which is usually over 2400 kg/m³.
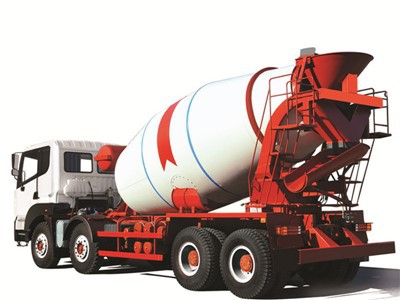
2. Insulating Properties
CBM concrete offers significant thermal insulation benefits. Its bubbly structure reduces heat conductivity, keeping buildings cooler in summer and warmer in winter. This property contributes to energy efficiency in buildings, making it an attractive option for construction.
3. Strength and Durability
Although lighter than traditional concrete, CBM concrete does not compromise on strength. Properly formulated mixes can achieve compressive strengths anywhere from 2.5 N/mm² to 30 N/mm², making it suitable for various structural applications.
4. Eco-Friendly Characteristics
CBM concrete is often considered more sustainable than traditional concrete. It can be made using recycled materials and requires less energy for production. Furthermore, its insulation properties contribute to lower energy consumption in buildings.
Methods of Producing CBM Concrete
1. Foaming Agent Method
The most common method for producing CBM concrete is through the use of foaming agents. A chemically stable foaming agent is mixed with water to create a foam, which is then combined with the cement mixture. The foam creates tiny air bubbles that reduce the density of the concrete.
2. Precast Method
In the precast method, CBM concrete is produced in molds at a factory setting. This allows for better quality control and uniformity. The finished blocks or panels can be transported to the construction site for assembly.
3. In-Situ Method
This method involves producing CBM concrete directly at the construction site. It is useful for large projects where specific dimensions and shapes are required. The mixing and pouring happen continuously, allowing for a seamless structure.
Applications of CBM Concrete
1. Building Construction
CBM concrete is widely used in building construction, especially in residential projects and low-rise buildings. Its lightweight nature reduces the load on foundations, making it ideal for various structures.
2. Infrastructure Projects
Due to its insulating properties, CBM concrete is suitable for infrastructure projects such as bridges, sound barriers, and insulation panels for tunnels. Its durability ensures longevity in these applications.
3. Modular Construction
CBM concrete is highly favorable for modular construction due to its ease of handling and quick assembly process. Prefabricated components can be constructed off-site and easily transported, significantly reducing construction times.
4. Road Construction
Application | Description |
---|---|
Sub-base Layers | Used in sub-base layers for pavements to provide insulation. |
Noise Barriers | Effectively reduces noise pollution by absorbing sound. |
Advantages of Using CBM Concrete
1. Cost-Effectiveness
The lightweight properties of CBM concrete reduce transportation costs and increase labor efficiency during construction. This translates to overall lower project costs.
2. Energy Efficiency
The thermal insulation properties of CBM concrete contribute significantly to energy savings over the life of a building. This can lead to reduced heating and cooling costs for occupied spaces.
3. Flexibility and Adaptability
CBM concrete can be easily molded into various shapes and sizes, allowing for creative architectural designs and flexibility in construction.
Challenges in Using CBM Concrete
1. Knowledge and Expertise
Working with CBM concrete requires specific knowledge regarding mixing, curing, and application methods. Insufficient expertise can lead to subpar results.
2. Variability in Properties
The properties of CBM concrete can vary significantly based on the mix and production method. Consistency must be maintained to meet structural requirements.
3. Limited Load-Bearing Capacity
While CBM concrete offers strength for various applications, its lightweight nature limits its use in heavy-load bearing structures. Adequate analysis is required to avoid structural failures.
Best Practices for Working with CBM Concrete
1. Proper Mix Design
Establishing an appropriate mix design according to the specific application is vital. Ensure the balance between air bubble content and aggregate size for desired strength and density.
2. Quality Control
Conduct regular quality checks during the mixing and casting processes to maintain consistency and avoid defects.
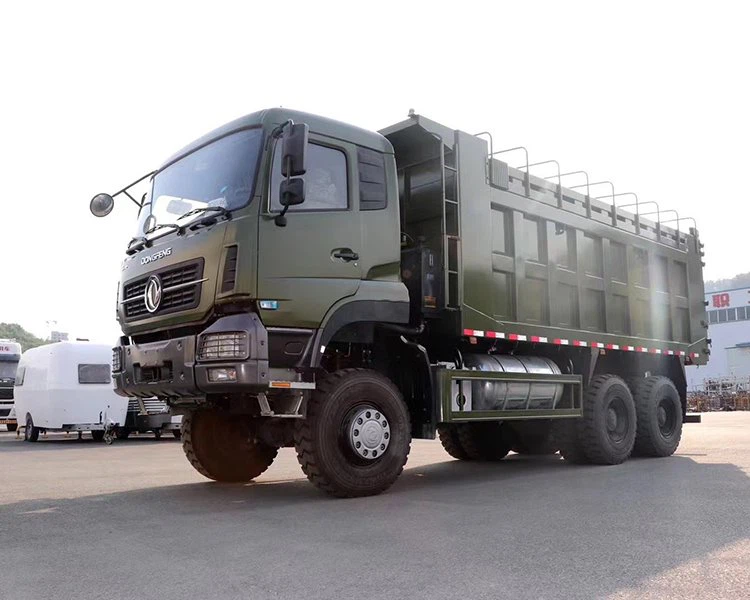
3. Curing Techniques
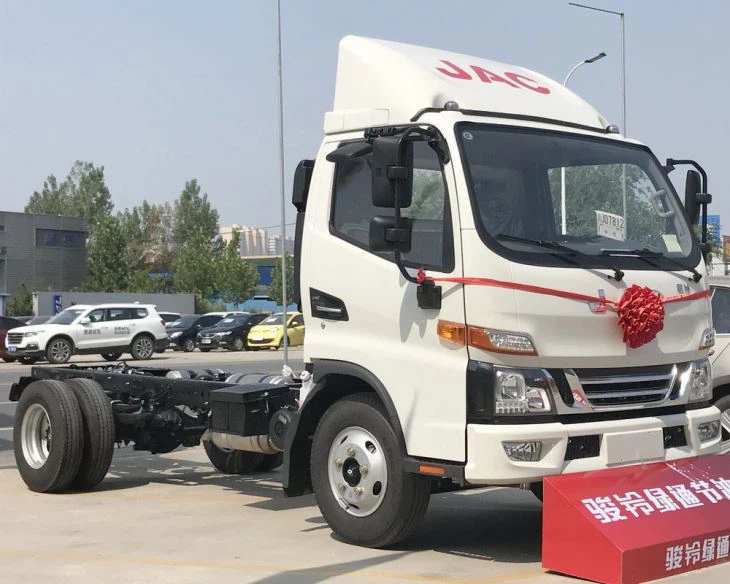
Implement effective curing techniques to prevent cracks and ensure complete hydration of the concrete. This could involve covering the surface to retain moisture or using curing compounds.
Cost Analysis of CBM Concrete
Item | Traditional Concrete | CBM Concrete |
---|---|---|
Material Costs | Higher due to dense aggregates | Lower due to lightweight materials |
Transportation | Higher weight increases lift costs | Lower costs due to reduced weight |
Labor Costs | Standard | Reduced labor needed for handling |
Frequently Asked Questions (FAQs)
1. What is the primary difference between CBM concrete and traditional concrete?
CBM concrete is lighter and has better insulation properties than traditional concrete. It is made with air bubbles that reduce its density, while traditional concrete usually has a higher density and weight.
2. Can CBM concrete be used for structural applications?
Yes, CBM concrete can be used for structural applications, but its suitability depends on the specific load requirements. Proper engineering analysis is essential.
3. How is CBM concrete produced on site?
On-site production of CBM concrete involves mixing foam with a cement aggregate mixture directly at the construction site. This method ensures that the concrete is fresh when used for pouring.
4. What are the environmental benefits of using CBM concrete?
CBM concrete is often considered more environmentally friendly due to its use of recycled materials, lower energy consumption for production, and energy-saving insulation properties that reduce heating and cooling needs.
5. Can CBM concrete be colored or finished like traditional concrete?
Yes, CBM concrete can be colored and finished using similar methods as traditional concrete, such as staining, painting, or adding decorative aggregates.
6. What maintenance does CBM concrete require?
CBM concrete generally requires minimal maintenance, but it should be monitored for water damage or cracking over time. Regular inspections can help maintain its integrity.