Introduction
Concrete mixer trucks are vital in construction projects, ensuring that concrete is mixed and delivered efficiently. Understanding the various parts of a concrete mixer truck helps operators maintain and repair their vehicles effectively. This article explores the essential components of concrete mixer trucks, offering insights into their functions and tips for proper maintenance. We will cover everything from the mixing drum to the chassis, providing a thorough understanding of each part’s role in the operation of the truck.
The Importance of Concrete Mixer Trucks
Concrete mixer trucks play a crucial role in the construction industry by transporting pre-mixed concrete from batch plants to construction sites. Their specialized design allows for maintaining the integrity of the concrete mixture during transit, ensuring that it arrives ready for pouring. By understanding the parts of these trucks, operators can ensure optimal performance and longevity, preventing costly breakdowns and delays in construction schedules.
Key Components of a Concrete Mixer Truck
Concrete mixer trucks consist of several critical components, each contributing to the overall function and efficiency of the vehicle. Below, we break down the main parts of a concrete mixer truck and explain their roles.
1. Chassis
The chassis is the truck’s frame, providing structural support for all other components. It houses the engine, transmission, and axles. A robust chassis is crucial to ensure that the truck can handle the heavy load of wet concrete.
Common Chassis Types
- Standard Chassis: Suitable for most construction sites.
- Heavy-Duty Chassis: Designed for larger loads and rough terrain.
2. Mixing Drum
The mixing drum is the most recognizable part of a concrete mixer truck. It is responsible for mixing the raw materials—cement, water, sand, and aggregates—into concrete. The drum rotates to ensure thorough mixing and to prevent the concrete from setting before delivery.
Drum Specifications
Drum Capacity | Common Sizes (Cubic Yards) |
---|---|
Small | 3 to 6 |
Medium | 7 to 10 |
Large | 11 to 14 |
3. Auger
The auger is a spiral tool located inside the mixing drum. It helps move the concrete towards the discharge chute, enabling a smooth and consistent flow of concrete to be poured at the job site. Proper maintenance of the auger is essential to prevent blockages and ensure efficient mixing.
4. Discharge Chute
This component allows the concrete to exit the mixing drum and flow onto the construction site. The discharge chute can be adjusted to direct the concrete precisely where it’s needed. Operators must ensure the chute is free of obstructions for seamless operations.
5. Water Tank
A water tank is usually mounted on the mixer truck to add water to the mix as needed. It provides flexibility in adjusting the consistency of the concrete. Operators should regularly check for leaks and clean the tank to avoid contamination.
6. Transmission System
The transmission system transfers power from the engine to the truck’s wheels. An efficient transmission is vital for maintaining the truck’s speed and handling, especially on uneven terrain. Regular maintenance checks can avoid costly repairs.
7. Engine
The engine powers the entire mixer truck. Depending on the model, it may run on diesel or gasoline. Regular oil changes and engine tune-ups are essential for ensuring maximum performance and longevity.
8. Tires
The tires provide traction and support for the truck. Given the weight of a fully loaded concrete mixer, it’s vital to use high-quality, durable tires designed for heavy loads. Inspecting and replacing tires worn down is critical for safety and performance.
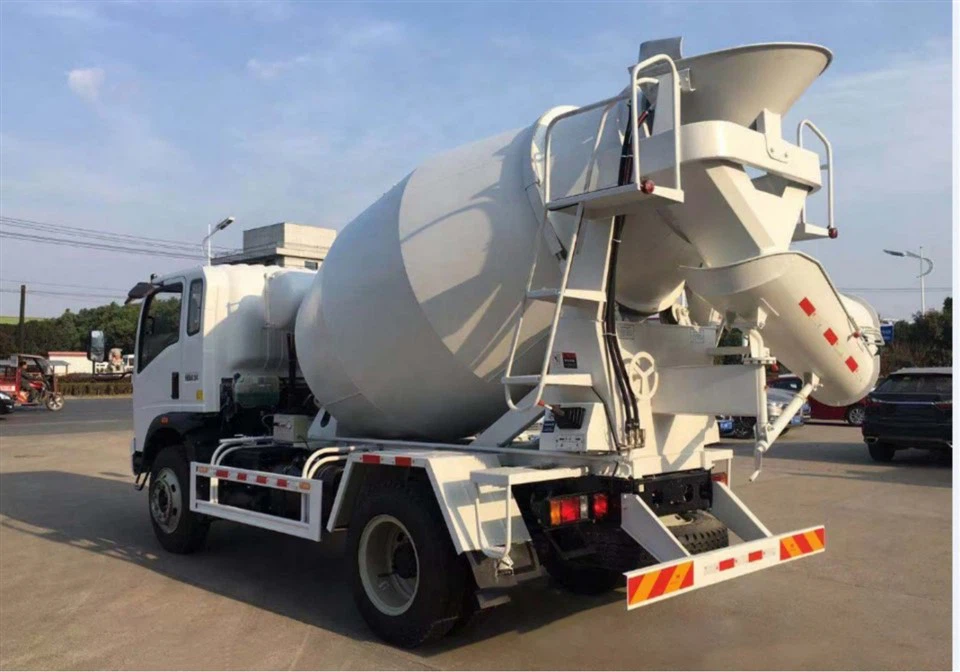
9. Hydraulic System
The hydraulic system is responsible for the movement of the mixing drum and other components. Regular checks can help identify leaks and maintain optimal function. A well-maintained hydraulic system is crucial for smooth operation and control over the drum’s positioning.
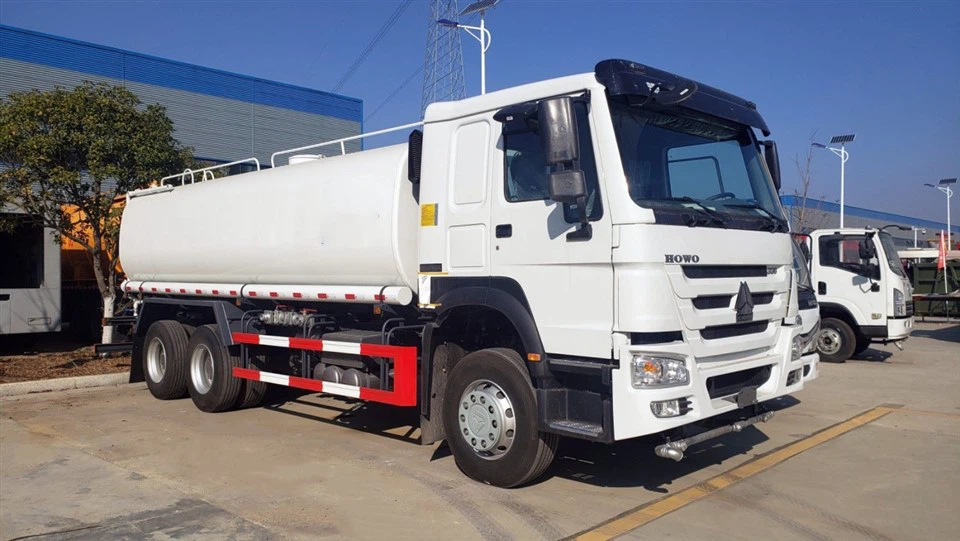
10. Control Panel
The control panel allows the operator to manage the mixing drum’s rotation speed, the flow of concrete, and other essential functions. Understanding how to read the control panel effectively can significantly improve the efficiency of the mixing process.
Maintenance Tips for Concrete Mixer Truck Parts
Proper maintenance of concrete mixer truck parts ensures their longevity and minimizes downtime during operation. Here are some practical tips:
1. Regular Inspections
Conduct thorough inspections of all parts regularly. Focus on the mixing drum, hydraulic system, and tires to catch any issues early.
2. Lubricate Moving Parts
Apply lubricant to moving parts, including the auger and hydraulic components, to reduce wear and tear and improve performance.
3. Monitor Fluid Levels
Ensure that engine oil, hydraulic fluid, and coolant levels are at recommended levels to prevent overheating and engine failure.
4. Clean the Mixing Drum
After each use, ensure that the mixing drum is cleaned to prevent concrete buildup. Leftover concrete can harden and become difficult to remove.
5. Tire Maintenance
Regularly check tire pressure and tread wear. Replace any tires that show signs of excessive wear or damage.
Cost of Concrete Mixer Truck Parts
Understanding the costs associated with various parts of a concrete mixer truck can help owners budget for repairs and maintenance. Below is a table with general estimates for common parts:
Part | Estimated Cost (USD) |
---|---|
Mixing Drum | $15,000 – $30,000 |
Hydraulic System | $2,000 – $8,000 |
Engine | $10,000 – $20,000 |
Tires | $1,000 – $3,000 (set) |
Control Panel | $1,500 – $3,000 |
Leading Manufacturers of Concrete Mixer Truck Parts
Several manufacturers specialize in producing high-quality parts for concrete mixer trucks. Some of the leading brands include:
1. Oshkosh
Oshkosh is known for producing durable and reliable mixer trucks that can withstand heavy-duty use.
2. Mack Trucks
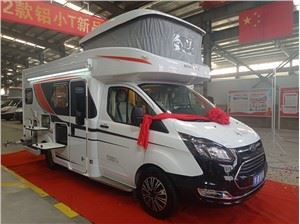
Mack offers a range of concrete mixer trucks with excellent build quality and innovative features.
3. Kenworth
Kenworth trucks are known for their engine performance and user-friendly design, making them suitable for concrete mixing.
4. Peterbilt
Peterbilt provides a diverse lineup of mixer trucks, focusing on fuel efficiency and driver comfort.
Future Trends in Concrete Mixer Truck Technology
As technology advances, several trends are emerging in the concrete mixing industry:
1. Eco-Friendly Solutions
Many manufacturers are working towards developing eco-friendly concrete mixer trucks that reduce emissions and fuel consumption.
2. Automation and Smart Technology
Integrating sensors and automation into concrete mixer trucks helps in monitoring performance, enabling predictive maintenance, and improving safety features.
3. Lightweight Materials
Using lightweight materials in truck manufacturing can help improve fuel efficiency and enhance performance without sacrificing strength.
FAQ Section
What is the typical lifespan of a concrete mixer truck?
A well-maintained concrete mixer truck can last anywhere from 10 to 15 years, depending on usage and care.
How often should I perform maintenance on my mixer truck?
Regular inspections should be conducted weekly, with more thorough maintenance checks every 1,000 miles or every six months, whichever comes first.
What should I do if my mixer truck breaks down?
If your mixer truck breaks down, first ensure safety and then assess the problem. Contact a professional mechanic for repairs if you’re unable to troubleshoot the issue.
Can I replace parts of the mixer truck myself?
While some basic maintenance tasks can be performed by owners, replacing major components is often best left to professionals to ensure safety and proper installation.
Are there specific regulations for operating concrete mixer trucks?
Yes, regulations vary by region, but common requirements include licensing for operators, compliance with weight limits, and proper safety equipment.
What factors should I consider when purchasing parts for my mixer truck?
Consider the quality of the parts, compatibility with your specific truck model, and warranty options to ensure reliability and longevity.