Understanding how a cement mixer truck works is crucial for construction professionals and enthusiasts alike. This article will delve deeply into the operation, components, and practical applications of cement mixer trucks, equipping you with valuable insights.
Table of Contents
- 1. Introduction to Cement Mixer Trucks
- 2. Components of a Cement Mixer Truck
- 3. Operating Principle of Cement Mixer Trucks
- 4. The Mixing Process Explained
- 5. How Cement Mixer Trucks Transport Concrete
- 6. Loading and Unloading Techniques
- 7. Maintenance Tips for Cement Mixer Trucks
- 8. Common Issues and Troubleshooting
- 9. Environmental Concerns and Solutions
- 10. Frequently Asked Questions
1. Introduction to Cement Mixer Trucks
Cement mixer trucks, or concrete trucks, play a vital role in the construction industry. They are designed to transport and mix concrete efficiently, ensuring that it arrives at the job site ready for use. These trucks save time and labor costs, making them an essential piece of equipment in modern construction projects.
2. Components of a Cement Mixer Truck
Cement mixer trucks consist of various components that work together to achieve the desired result. Here are the key parts:
2.1 Chassis
The chassis is the truck’s main frame, supporting all other components. It includes the engine, transmission, and axles.
2.2 Mixer Drum
The mixer drum is a cylindrical container mounted on the truck’s chassis. It rotates to mix the concrete ingredients and keep the mixture in a fluid state during transportation.
2.3 Auger
An auger is a spiral-shaped mechanism located at the back of the truck. It helps to discharge the concrete from the mixer drum and is often powered hydraulic.
2.4 Control System
The control system includes all electronic controls that manage the mixer’s operations, including speed and mixing duration.
2.5 Water Tank
A water tank is typically integrated into the design to add water during mixing or to clean the mixer drum post-job.
2.6 Other Components
- Calibration and Load Cells
- Hydraulic System
- Discharge Chute
- Wheels and Tires
3. Operating Principle of Cement Mixer Trucks
The operational mechanics behind cement mixer trucks involve mixing cement, water, and aggregates (sand or gravel) while in transit. Here’s a breakdown of how it works:
3.1 Loading Cement and Aggregates
Cement and aggregates are loaded into the mixer drum at a batching plant. The ingredients are measured precisely to achieve the desired concrete strength and consistency.
3.2 Mixing Ingredients
Once loaded, the mixer drum rotates clockwise, blending the ingredients together. This process ensures a uniform mixture, crucial for the quality of the concrete.
3.3 Transportation
The truck then travels to the construction site, where the drum continues to rotate to prevent the mixture from setting.
3.4 Discharging Concrete
Upon arrival, the operator uses the auger system or turns the drum in the reverse direction to discharge the concrete. The hydraulic mechanism helps control this process, allowing for precise delivery.
4. The Mixing Process Explained
The mixing process is essential for creating high-quality concrete. Here’s a step-by-step explanation:
4.1 Batching
Ingredients are batched in exact proportions. This phase utilizes scales to ensure accuracy.
4.2 Dry Mixing
The drum may rotate to facilitate dry mixing before adding water, ensuring an even distribution of all dry components.
4.3 Adding Water
Water is added gradually during mixing, allowing for better control of the concrete’s final consistency.
4.4 Final Mixing
The rotation continues until the mixture reaches a homogeneous consistency. Variations in time can affect the mix’s quality and characteristics.
4.5 Verification
Once mixing is complete, concrete samples may be taken for testing to ensure they meet required standards.
5. How Cement Mixer Trucks Transport Concrete
Transportation is a crucial phase that ensures concrete is delivered correctly and efficiently. Here are the main factors involved:
5.1 Route Planning
Effective route planning is essential, considering road conditions, traffic patterns, and distance from the batching plant to the job site.
5.2 Timing
The optimal time for transportation is tightly controlled, as concrete should typically be poured within 90 minutes after mixing to maintain integrity.
5.3 Continuous Rotation
The mixer drum continuously rotates to keep the concrete from setting during transit, using a speed appropriate to maintain fluidity without over-mixing.
6. Loading and Unloading Techniques
Loading and unloading concrete efficiently can significantly impact productivity on-site. Here’s how it’s typically done:
6.1 Loading Techniques
Concrete trucks are loaded at batch plants using chutes or hoppers. The mixer drum is positioned to receive the ingredients as they are poured in.
6.2 Unloading Techniques
Unloading can be accomplished using:
- Direct Discharge: The truck turns the drum in the reverse direction.
- Chute or Auger: Helps in guiding the concrete precisely where needed.
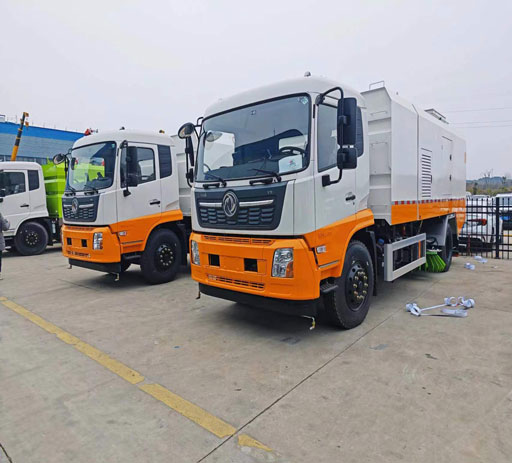
7. Maintenance Tips for Cement Mixer Trucks
Regular maintenance is key to ensuring the longevity and performance of cement mixer trucks. Crucial maintenance tips include:
7.1 Daily Checks
Operators should perform daily inspections of the mixer drum, auger, and hydraulic systems.
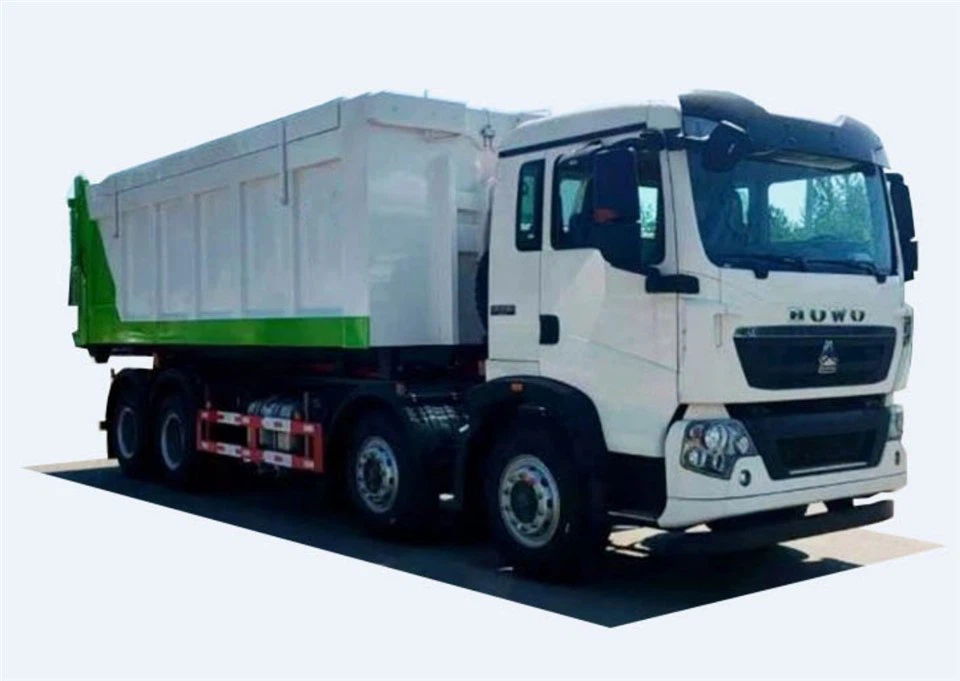
7.2 Lubrication
Regularly lubricate moving components to prevent wear and improve efficiency.
7.3 Cleaning
Immediately after unloading, cleaning the drum helps prevent concrete buildup and facilitates easier future loadings.
7.4 Scheduled Maintenance
Adhere to industry standards for scheduled maintenance services, including inspecting all electrical and hydraulic systems.
8. Common Issues and Troubleshooting
Cement mixer trucks can encounter various issues that may affect their operation. Here are some common problems and solutions:
8.1 Concrete Setting in the Drum
If the truck is delayed, the concrete can begin to set inside the drum. If this occurs, a mixture of water and frequent rotation can help. However, if it hardens, professional cleaning will be necessary.
8.2 Hydraulic Failures
Check for leaks or pressure drops in the hydraulic system and consult the manual for troubleshooting steps.
8.3 Engine Malfunctions
Regular inspections of the engine and adhering to service intervals can prevent unexpected breakdowns.
8.4 Unusual Noises
Any abnormal sounds should be investigated immediately as they can indicate mechanical issues that require attention.
9. Environmental Concerns and Solutions
The construction industry is fraught with environmental concerns, and cement mixer trucks are no exception. Here are some common issues and sustainable solutions:
9.1 Dust Emissions
Dust generated during loading can affect air quality. Using dust extraction systems can mitigate this issue.
9.2 Water Usage
Excessive water used during cleaning can lead to water wastage. Implementing a recycling water system can conserve water resources.
9.3 Noise Pollution
Operational noise can be disruptive. Using sound-dampening materials and engine silencing technologies helps reduce noise levels.
10. Frequently Asked Questions
10.1 What is the capacity of a cement mixer truck?
Most cement mixer trucks have a capacity ranging from 6 to 16 cubic yards, depending on the truck’s size and design.
10.2 How far can a cement mixer truck deliver concrete?
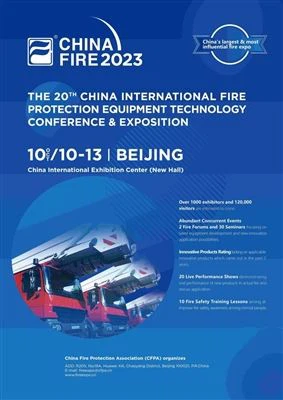
The distance concrete can be delivered largely depends on travel time and traffic conditions, but typically ranges from 10 to 70 miles from the batching plant.
10.3 Can cement mixer trucks mix different types of concrete?
Yes, cement mixer trucks can typically mix different types of concrete by adjusting the ratio of ingredients during batching.
10.4 How long does concrete last in a cement mixer?
Concrete should ideally be poured within 90 minutes of mixing to maintain its integrity, but some circumstances may vary based on additives used.
10.5 What training is required to operate a cement mixer truck?
Operators typically need a commercial driver’s license (CDL) and specialized training for handling the equipment safely and efficiently.
10.6 What are the safety precautions for operating a cement mixer truck?
Operators should always wear appropriate personal protective equipment (PPE), perform pre-operation checks, and be trained on safe loading and unloading practices.