Introduction to Milk Truck Tanks
Milk truck tanks are critical components in the dairy industry. They are designed to safely transport liquid milk from farms to processing facilities. This article delves deep into the functionality, types, maintenance, and importance of milk truck tanks, making it a valuable resource for dairymen, fleet operators, and industry enthusiasts. With the growth of the dairy industry, understanding milk truck tanks and their operation can greatly enhance efficiency and safety in milk transportation.
What is a Milk Truck Tank?
A milk truck tank is an insulated tanker specifically designed to transport raw or processed milk. These tanks are manufactured from stainless steel to ensure durability, prevent contamination, and maintain the quality of the milk during transport. They come in various sizes, typically ranging from 1,000 to 8,000 gallons, depending on the needs of the dairy farm and processing facility.
Why Are Milk Truck Tanks Important?
These tanks play a vital role in the dairy supply chain. They not only help in transporting milk safely but also ensure that it is kept at the right temperature. Maintaining optimal conditions is crucial to prevent spoilage and preserve freshness.
Components of a Milk Truck Tank
Component | Function |
---|---|
Insulation | Helps keep the milk at a stable temperature |
Valve System | Allows for easy filling and emptying of the tank |
Pumping System | Facilitates the transfer of milk to other containers |
Manhole | Provides access for cleaning and inspection |
Types of Milk Truck Tanks
Milk truck tanks can be classified into several types based on various factors such as design, capacity, and usage.
1. Standard Milk Tankers
These are the most common type of milk trucks, equipped with a single compartment for raw milk collection. They are widely used in rural dairy farms for collection and transportation.
2. Insulated Milk Tankers
Insulated tankers are designed with thermal insulation to keep milk at optimal temperatures during transport. They protect milk from temperature fluctuations, preventing spoilage.
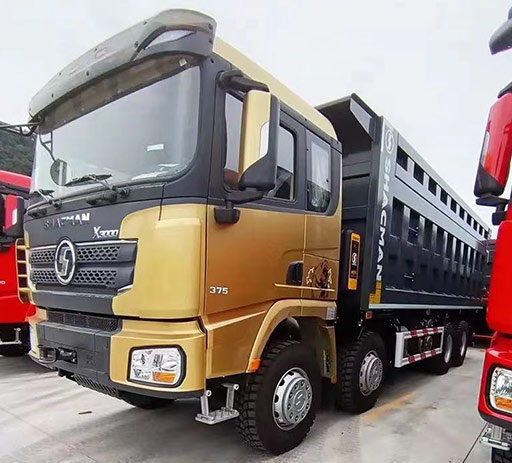
3. Multi-Compartment Milk Tankers
These tankers have multiple compartments, allowing them to transport different types of dairy products simultaneously. This design is excellent for operations serving multiple clients.
How Milk Truck Tanks Work
The operation of a milk truck tank involves several key processes, from loading at the dairy farm to delivery at the processing plant.
1. Loading Milk
The first step is the loading process. Milk is pumped from the farm’s bulk tank into the tanker. It’s crucial for this process to be done quickly to maintain the milk’s freshness.
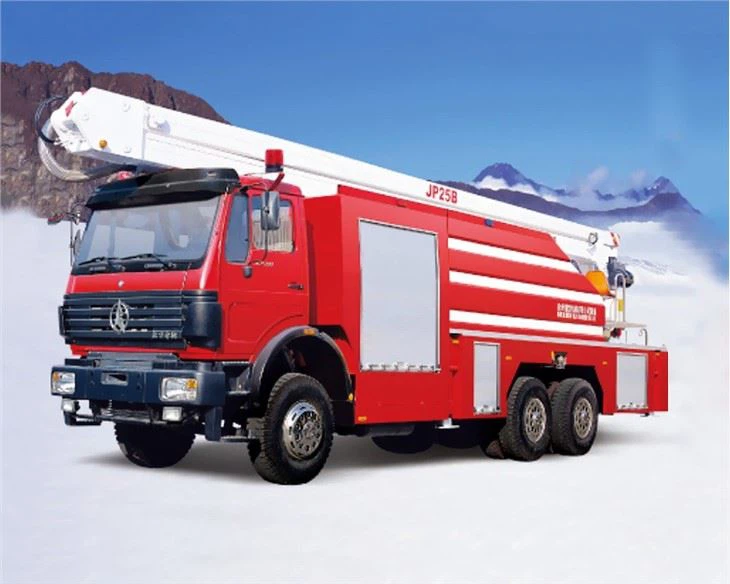
2. Insulation and Temperature Control
Once loaded, the tank’s insulation keeps the milk at a safe temperature. Milk should ideally be kept below 40°F (4°C) to avoid bacterial growth.
3. Transporting the Milk
During transport, the truck should minimize stops and ensure the fastest route to the processing facility. A reliable tracking system can help in monitoring this process.
4. Unloading Milk
At the processing facility, the tank is connected to the facility’s system for easy unloading. The unloading should also be done efficiently to maintain quality.
Maintenance of Milk Truck Tanks
Regular maintenance of milk truck tanks is crucial for ensuring hygiene and efficiency. Here are some practical tips:
1. Daily Cleaning
After each use, tanks must be cleaned to prevent milk residue buildup. Hot water and appropriate cleaning agents should be used.
2. Regular Inspections
Routine inspections for leaks, dents, or corrosion can help maintain the tank’s integrity. Any worn-out components should be replaced immediately.
3. Temperature Monitoring
Utilizing temperature monitoring systems can help ensure that milk is kept at optimal temperatures during transport.
Safety Considerations in Milk Tank Transportation
Operating milk truck tanks comes with several safety considerations:
1. Compliance with Regulations
All milk transportation must comply with local health regulations to ensure safety and quality.
2. Driver Training
Drivers should be trained in the proper handling of milk truck tanks, including emergency protocols and safe driving practices.
3. Equipment Safety Checks
Regular equipment checks can prevent accidents during transit. Ensuring brakes, tires, and other critical components are in good condition is vital.
The Future of Milk Truck Tanks
The dairy industry is constantly evolving, and so are milk truck tanks. Key trends shaping the future include:
1. Technological Innovations
Smart monitoring systems that integrate IoT technology for real-time tracking and temperature monitoring are becoming standard.
2. Environmental Considerations
With a growing focus on sustainability, manufacturers are exploring eco-friendly materials and practices in tanker production.
Conclusion
Understanding milk truck tanks is crucial for anyone involved in the dairy industry. From safe transportation to effective maintenance practices, the proper management of these tanks ensures the delivery of high-quality milk, benefiting producers and consumers alike.
FAQs
1. How often should milk truck tanks be cleaned?
Milk truck tanks should be cleaned after every use to prevent residue buildup and contamination.
2. What is the ideal temperature for transporting milk?
The ideal temperature for transporting milk is below 40°F (4°C) to prevent bacterial growth.
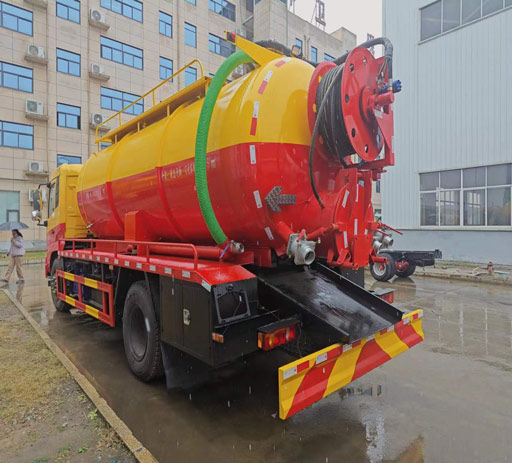
3. How long can milk remain in a tank during transport?
Ideally, milk should not remain in a tank for more than 24 hours during transport, depending on temperature control.
4. Are there specific laws regulating milk transportation?
Yes, there are specific local and federal regulations governing milk transportation to ensure safety and quality.
5. What types of materials are milk truck tanks typically made from?
Milk truck tanks are typically made from stainless steel due to its durability and resistance to corrosion.
6. Can milk truck tanks be used for transporting other liquids?
While milk truck tanks are designed specifically for dairy products, some may be suitable for carrying other non-corrosive liquid food products. Always check compatibility first.