Introduction
Oil tanker trailers are vital components in the transportation of liquid fuel, oil, and other hazardous materials. Understanding their design, functionality, and safety measures is critical for operators and businesses in the oil industry. This article dives deep into various aspects of oil tanker trailers, exploring their types, benefits, maintenance, safety protocols, and more. Whether you’re a fleet manager, driver, or an oil industry aficionado, this comprehensive guide will provide you with the information needed to navigate the world of oil tanker trailers effectively.
What is an Oil Tanker Trailer?
An oil tanker trailer is a specialized vehicle designed for transporting fluids such as crude oil, gasoline, or chemicals. These trailers are built to withstand the unique challenges posed by the transport of liquid products, ensuring safe delivery to different destinations.
Key Components of an Oil Tanker Trailer
- Tank: Typically made of strong, corrosion-resistant materials that are capable of holding large volumes of liquid.
- Chassis: The base frame designed to support the tank and withstand the weight of the loaded liquids.
- Suspension System: Helps absorb road bumps and ensures a smooth ride, which is crucial for maintaining the stability of the load.
- Valves and Hoses: Essential for loading and unloading the contents securely and efficiently.
Types of Oil Tanker Trailers
There are different types of oil tanker trailers based on their construction and usage. Here are some common types:
1. Semi-Trailer Tankers
These are trailers that are designed to be towed by a truck. They typically have a cylindrical tank and are among the most common types utilized in the oil industry.
2. Rollover Tank Trailers
This type of trailer is built with a lower center of gravity, enhancing stability during transport. They are designed to prevent loss of cargo in case of accidents.
3. Rear and Side Loading Tankers
Depending on the design, some tankers can be loaded from the rear or sides, providing flexibility in how they’re operated and minimizing downtime at loading stations.
4. Compartmentalized Tankers
These trailers have multiple compartments that allow for the transportation of different types of liquids simultaneously while minimizing the risk of contamination.
Benefits of Using Oil Tanker Trailers
Employing oil tanker trailers comes with several advantages:
1. Increased Efficiency
Oil tanker trailers enable large quantities of liquid fuel or chemicals to be transported in one trip, reducing the number of trips needed and improving overall efficiency.
2. Safety Features
Modern oil tanker trailers are equipped with various safety features, such as spill containment systems, emergency shut-off valves, and pressure relief valves, to enhance the security of transporting hazardous materials.
3. Environmental Control
With proper design and maintenance, these trailers help minimize the risk of spills or leaks, contributing to better environmental protection over traditional transport methods.
How to Choose the Right Oil Tanker Trailer
Selecting the right oil tanker trailer can significantly affect your operations. Consider the following factors:
1. Cargo Capacity
Evaluate the volume of liquid you plan to transport. Tankers come in various sizes, and understanding your needs is crucial for selecting one that offers optimal capacity.
2. Type of Liquid
Different liquids require specific features in a trailer, such as heating systems for viscous materials or insulation for temperature-sensitive products.
3. Road Regulations
Ensure that the chosen tanker complies with local, national, and international road regulations concerning the transportation of hazardous materials.
Maintenance Tips for Oil Tanker Trailers
1. Regular Inspections
Conduct regular inspections to identify potential issues such as leaks, structural integrity, and the condition of tires and brakes. Document these inspections for compliance and future reference.
2. Cleaning the Tank
Keep the interior of the tank clean to avoid contamination. Implement a defined cleaning schedule based on the type of liquid being transported.
3. Replacement of Worn Parts
Regularly check and replace worn-out components like hoses, gaskets, and valves to prevent leaks and ensure efficiency.
4. Seasonal Preparation
Prepare your tanker for seasonal weather changes, such as cold winters. Insulating materials or heating systems may be necessary for specific regions.
Safety Protocols for Operating Oil Tanker Trailers
Safety is of utmost importance in the oil industry. Here are protocols to ensure safe operations:
1. Proper Training
Ensure all drivers and operators receive training on handling hazardous materials and operating tanker trailers safely.
2. Use of Personal Protective Equipment (PPE)
Always wear the required PPE, including gloves, goggles, and flame-resistant clothing, while handling oil or chemicals.
3. Adherence to Environmental Regulations
Familiarize yourself with local environmental regulations concerning the transportation of oil. Follow guidelines to determine the best practices to prevent spills and accidents.
4. Emergency Preparedness
Have an emergency response plan in place, including spill kits, and ensure that all personnel know how to react in case of a leak or accident.
Real-World Examples of Oil Tanker Trailers in Use
Oil tanker trailers are widely used across various industries. Here are some practical examples:
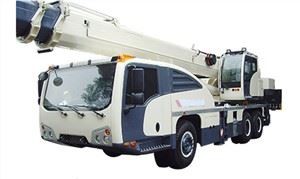
1. Transportation of Crude Oil
Oil companies use tanker trailers to transport crude oil from extraction sites to refineries. For instance, in the North Dakota oil fields, large semi-tanker trailers help move thousands of barrels daily to processing facilities.
2. Delivery to Gas Stations
Gasoline distributors rely on compartmentalized tankers to efficiently deliver fuel to gas stations. These tankers can load different grades of fuel and minimize downtime at the loading terminal.
3. Chemical Transport
Chemicals require specialized trailers designed for various properties, such as corrosiveness and volatility. Companies transport hazardous chemicals using unique tankers with specific containment measures.
Cost Factors When Investing in Oil Tanker Trailers
Investing in oil tanker trailers involves understanding the associated costs:
1. Initial Purchase Cost
The cost of purchasing a new oil tanker trailer can vary significantly based on size, type, and features, ranging anywhere from $30,000 to $150,000 or more.
2. Maintenance and Operational Costs
Routine maintenance costs, insurance, fuel consumption, and repairs contribute to ongoing operational expenses. Establish a budget for these elements to ensure profitability.
3. Regulatory Compliance Costs
Meeting safety and environmental regulations may require investing in additional equipment or training, which should be factored into total costs.
Frequently Asked Questions (FAQ)
1. What is the average lifespan of an oil tanker trailer?
The average lifespan of an oil tanker trailer can range from 10 to 25 years, depending on maintenance, usage, and environmental conditions.
2. How do I clean an oil tanker trailer?
Cleaning involves emptying the tank, rinsing with appropriate cleaning solutions, and ensuring all residues are removed. It is recommended to follow specific cleaning protocols for the type of liquid transported.
3. Are oil tanker trailers regulated?
Yes, oil tanker trailers are subject to stringent regulations related to design, construction, and operation by governmental authorities to ensure safety and environmental protection.
4. Can oil tanker trailers transport other liquids?
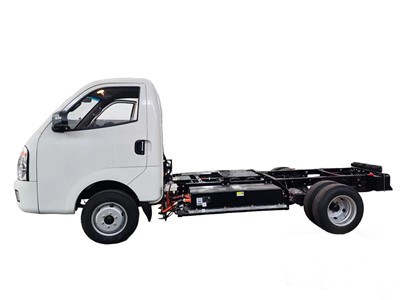
Yes, compartmentalized oil tanker trailers can transport various liquids, including chemicals. However, care must be taken to prevent contamination and comply with regulations.
5. What safety features should I look for in an oil tanker trailer?
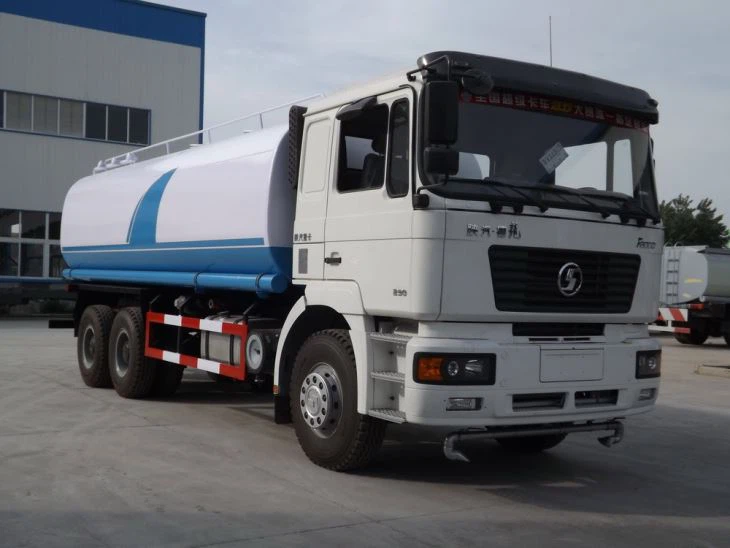
Some essential safety features to look for include spill containment systems, leak detection technologies, and emergency shut-off valves.
6. How often should I inspect my oil tanker trailer?
Regular inspections should be conducted before each trip and scheduled comprehensive inspections every few months. Compliance with manufacturer recommendations is essential for safe operations.