Introduction
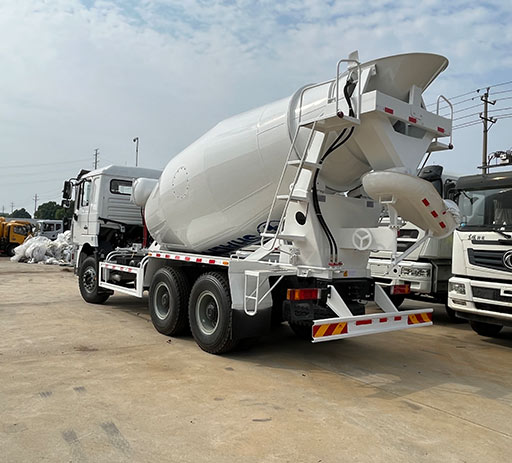
Weaver’s sanitation refers to the practices and protocols that ensure cleanliness and hygiene in weaving environments, where textiles are produced. The significance of sanitation extends beyond mere cleanliness; it encompasses the health and safety of workers, the quality of the products, and sustainability within the textile industry. With a rising emphasis on hygiene practices, especially in industrial settings, this article aims to provide a detailed understanding of weaver’s sanitation, exploring its importance, best practices, challenges, and solutions.
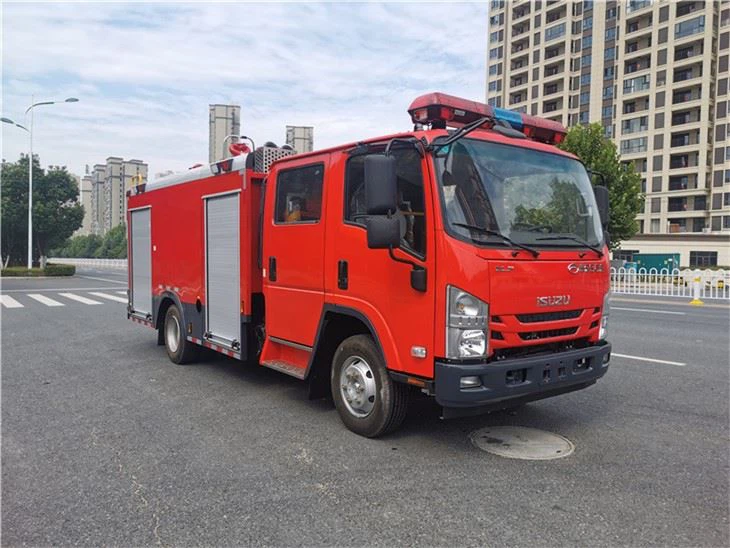
The Importance of Weaver’s Sanitation
Sanitation in weaving is crucial for several reasons:
- Health and Safety: Maintaining a clean environment reduces the risk of accidents and exposure to harmful substances.
- Product Quality: Clean surroundings contribute to the quality of the final textile products, preventing dust and contaminants.
- Employee Satisfaction: A hygienic workplace fosters better morale and productivity among employees.
- Regulatory Compliance: Compliance with health and safety regulations is mandatory for any weaving facility.
- Brand Image: Sanitation contributes to a positive public image, enhancing consumer trust.
Key Areas of Focus in Weaver’s Sanitation
1. Workspace Cleanliness
Workspace cleanliness involves systematic cleaning protocols that are implemented daily. Here are essential tips to ensure welding areas remain clean:
- Daily sweeping and mopping of floors to remove fibers and dust.
- Regular cleaning of machinery to prevent buildup of textiles and other residues.
- Strategic placement of waste disposal bins to encourage proper waste management.
2. Personal Hygiene of Workers
The personal hygiene of workers is paramount. Here are some practices to implement:
- Encourage regular hand washing, especially after handling raw materials.
- Provide adequate sanitation facilities such as handwashing stations and restrooms.
- Train employees on the importance of personal hygiene and how it affects product quality.
3. Handling Raw Materials
Proper handling of raw materials helps minimize contamination. Consider the following:
- Store raw materials in clean, sealed containers to avoid exposure to dust and pests.
- Implement a first-in, first-out (FIFO) system to ensure materials are utilized in a timely manner.
4. Waste Management
Effective waste management is essential in a weaving facility. Implement these practices:
- Establish a recycling program for textile waste.
- Dispose of hazardous materials in accordance with local regulations.
- Conduct regular audits of waste disposal methods to identify areas for improvement.
5. Equipment Sanitation
Sanitizing equipment is critical for maintaining a clean weaving environment. Best practices include:
- Regular servicing and cleaning of looms and other machinery.
- Using specific cleaning agents that are safe for industrial equipment.
- Training staff on proper equipment handling and maintenance to prevent contamination.
6. Air Quality Management
Good air quality is essential for the health of workers and the quality of products. Consider these strategies:
- Install air filtration systems to capture fibers and dust particles.
- Ensure proper ventilation in weaving areas to eliminate stagnant air.
- Monitor air quality regularly to check for contaminants.
7. Training and Awareness Programs
Comprehensive training is fundamental for effective sanitation. Consider these steps:
- Organize regular workshops emphasizing hygiene protocols.
- Develop an easy-to-understand manual on sanitation practices for all employees.
- Encourage feedback from employees about sanitation practices and areas of improvement.
8. Using Technology in Sanitation
Technology plays a vital role in ensuring sanitation in weaving. Explore these options:
- Invest in robotic cleaning systems for regular floor cleaning.
- Utilize monitoring systems for air quality and sanitation compliance.
- Implement digital solutions for tracking cleaning schedules and maintenance needs.
9. Compliance and Regulatory Standards
Understanding compliance with regulations is pivotal. Key points include:
- Stay informed about local and national sanitation laws relevant to textiles.
- Adopt sanitary standards set by organizations such as the Occupational Safety and Health Administration (OSHA).
- Audit your practices regularly to ensure compliance with all applicable standards.
10. Case Studies and Practical Examples
Examining real-life practices can provide valuable insights into effective sanitation strategies. Below are two case studies:
Company Name | Sanitation Practice Implemented | Benefits Observed |
---|---|---|
Textile Innovations | Regular training sessions for personal hygiene | Reduction in product complaints by 30% |
Eco-Friendly Fabrics | Installation of advanced air filtration systems | Improved overall air quality and employee health |
Challenges in Weaver’s Sanitation
While the need for effective sanitation practices is clear, several challenges can hinder implementation:
- Cost: Investing in sanitation equipment and training can be expensive for smaller operations.
- Compliance: Staying updated with changing regulations can be daunting.
- Employee Resistance: Some workers may resist change and new practices.
- Lack of Awareness: Not all workers may understand the importance of sanitation.
Best Practices for Overcoming Challenges
Overcoming the challenges in sanitation requires a proactive approach:
- Allocate budget specifically for sanitation improvements.
- Communicate the benefits of sanitation practices to all employees.
- Engage workers in discussions and decisions about sanitation policies.
- Provide ongoing training to keep everyone informed about best practices.
FAQs About Weaver’s Sanitation
1. What are the key components of effective weaver’s sanitation?
The key components include workspace cleanliness, personal hygiene, proper handling of raw materials, waste management, equipment sanitation, and air quality management.
2. How often should sanitation practices be implemented?
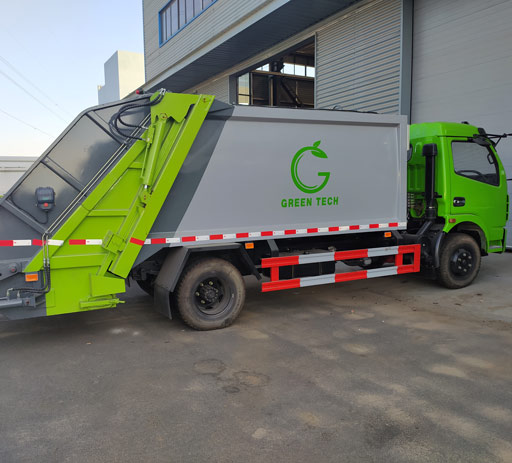
Sanitation practices should be continual, with daily cleaning routines and regular training sessions to reinforce the importance of hygiene.
3. What are some common mistakes in weaver’s sanitation?
Common mistakes include neglecting to clean machinery, improper waste disposal, and insufficient employee training on hygiene practices.
4. How can technology improve weaver’s sanitation?
Technology can enhance sanitation through automated cleaning systems, real-time air quality monitoring, and digital record-keeping for compliance checks.
5. Are there specific sanitation regulations for textile companies?
Yes, textile companies must comply with local, state, and federal hygiene regulations, including those set by OSHA and other regulatory bodies.
6. What can small textile businesses do to ensure sanitation?
Small businesses can implement simple sanitation practices like regular cleaning schedules, staff training, and efficient waste management systems.