Chemical mixing tanks are essential in numerous industries, such as pharmaceuticals, food processing, and chemical production. These tanks facilitate the mixing of different chemicals and solutions, ensuring uniformity and quality in the final products. In this article, we will explore various aspects of chemical mixing tanks, including types, designs, operational processes, safety considerations, and practical examples. Whether you’re new to the subject or looking to deepen your knowledge, this guide will provide you with everything you need to know.
What Are Chemical Mixing Tanks?
Chemical mixing tanks are specialized containers designed for the mixing, blending, cooling, heating, and storage of liquids and slurries in various industrial applications. Their primary purpose is to create a uniform product by thoroughly combining different chemical components. Understanding the types, designs, and operational features of these tanks is crucial for anyone involved in chemical manufacturing or related industries.
Key Features of Chemical Mixing Tanks
- Material: Typically made from stainless steel or other corrosion-resistant materials.
- Agitation Systems: Equipped with mixers or agitators to ensure thorough mixing.
- Temperature Control: Some tanks include heating or cooling jackets to maintain specific temperatures.
- Capacity: Available in various sizes to meet different production needs.
Types of Chemical Mixing Tanks
There are several types of chemical mixing tanks, each designed to meet specific mixing requirements:
1. Batch Mixing Tanks
Batch mixing tanks are used for mixing a specific quantity of chemicals at a time. Once the batch is complete, the contents are usually transferred to another container or processed further.
2. Continuous Mixing Tanks
These tanks facilitate the continuous inflow and outflow of materials, allowing for ongoing mixing processes. Continuous mixing is ideal for high-volume production where consistency is vital.
3. Jacketed Mixing Tanks
Jacketed tanks have an outer layer (or jacket) filled with a heating or cooling medium. This design enables the control of the internal temperature of the mixture, essential for reactions sensitive to temperature variations.
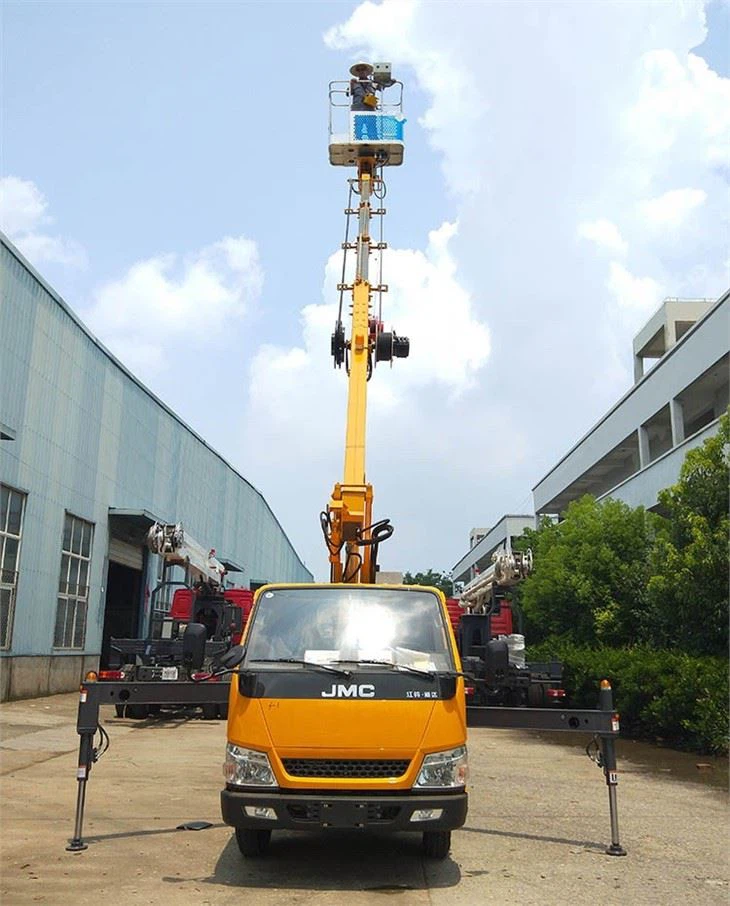
4. Mobile Mixing Tanks
Designed with wheels or skid bases, mobile mixing tanks can be easily relocated within a facility. These tanks are particularly useful for on-site mixing or situations requiring flexibility.
5. Vertical vs. Horizontal Tanks
Vertical tanks design allows for a smaller footprint, while horizontal tanks can facilitate easier loading and unloading of materials. The choice between them generally depends on space availability and operational preferences.
Design Considerations for Chemical Mixing Tanks
When designing or selecting a chemical mixing tank, several factors should be considered to ensure optimal performance:
1. Material Selection
The choice of materials is critical in preventing contamination and ensuring durability. Common materials include:
Material | Advantages | Disadvantages |
---|---|---|
Stainless Steel | Corrosion-resistant, durable | Higher cost |
Carbon Steel | Cost-effective for non-corrosive applications | Prone to rust and corrosion |
Polyethylene | Lightweight, resistant to corrosion | Less durable than metals |
2. Size and Capacity
Selecting the right size is crucial to meeting your production needs without wasting resources. Consider the volume of materials to be mixed and plan for future growth.
3. Agitation and Mixing Technology
The choice of agitator design will significantly impact the mixing efficiency. Consider the following types:
- Propeller Mixers: Suitable for low-viscosity liquids.
- Helical Ribbon Mixers: Ideal for medium to high-viscosity substances.
- Dynamic Mixers: Used for rapid mixing requirements.
Safety Considerations When Using Chemical Mixing Tanks
Ensuring safety during the operation of chemical mixing tanks is essential for both personnel and the environment. Implement the following safety measures:
1. Regular Maintenance
Routine inspections and maintenance of the mixing tanks and associated equipment can prevent mechanical failures that could lead to hazardous situations.
2. Proper Ventilation
Ensure that the mixing area is well-ventilated. Chemical reactions can release harmful gases, and proper ventilation reduces the risk of exposure.
3. Personal Protective Equipment (PPE)
Operators should wear appropriate PPE including gloves, goggles, and respirators to protect against chemical exposure.
4. Emergency Protocols
Establish and regularly train personnel on emergency protocols in case of spills or accidental exposure.
Operational Processes in Chemical Mixing Tanks
Understanding the operational processes involved in using chemical mixing tanks can enhance efficiency and product quality.
1. The Mixing Process
The mixing process typically follows these steps:
- Preparation of Raw Materials
- Loading Materials into the Tank
- Activation of Agitation Systems
- Monitoring of Mixing Parameters (temperature, pressure, consistency)
- Discharging the Mixture
2. Automation in Mixing
Many modern facilities employ automated systems for mixing to improve accuracy and reduce labor costs. These systems can include sensors and software for monitoring.
3. Quality Control Processes
Ensuring the quality of the mixed product can involve:
- Sampling during the mixing process
- Post-mixing analysis
- Compliance with industry regulations
Practical Examples of Chemical Mixing Tanks in Use
Chemical mixing tanks are prevalent across various industries. Here are a few examples:
1. Pharmaceutical Manufacturing
Pharmaceutical companies utilize mixing tanks for creating formulations of syrups, creams, and solutions. Precise measurements and consistent mixes are critical for efficacy and safety.
2. Food and Beverage Industry
In food processing, mixing tanks are used for combining ingredients. For example, juice production requires the mixing of various fruit concentrates, sugars, and preservatives.
3. Chemical Production
Chemical manufacturing facilities rely on mixing tanks to create products like detergents, fertilizers, and adhesives. The choice of tank type and mixing technology can affect product quality significantly.
Tips for Operating Chemical Mixing Tanks Effectively
- Regular training for operators on safety and operational procedures.
- Implementing a comprehensive maintenance program for equipment.
- Utilizing technology to monitor and control mixing parameters in real-time.
- Keeping thorough records of all mixing operations for compliance and quality control.
Frequently Asked Questions (FAQs)
1. What types of materials can be mixed in chemical mixing tanks?
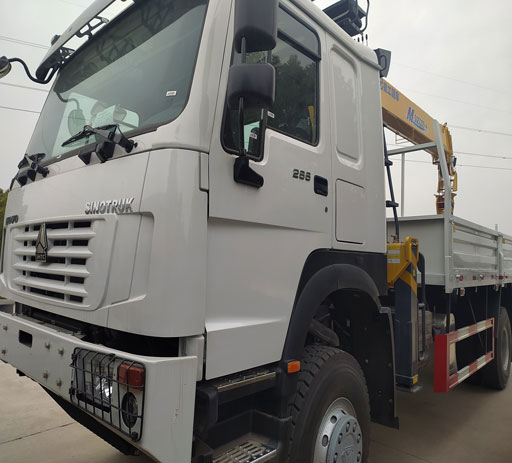
Chemical mixing tanks can handle a wide range of materials, including liquids, powders, and slurries. The choice of tank material and design will depend on the specific chemicals involved.
2. How do I choose the right size for a mixing tank?
The right size depends on the volume of materials you plan to mix and your production requirements. It’s essential to consider both current and future needs.
3. What are the safety regulations for operating chemical mixing tanks?
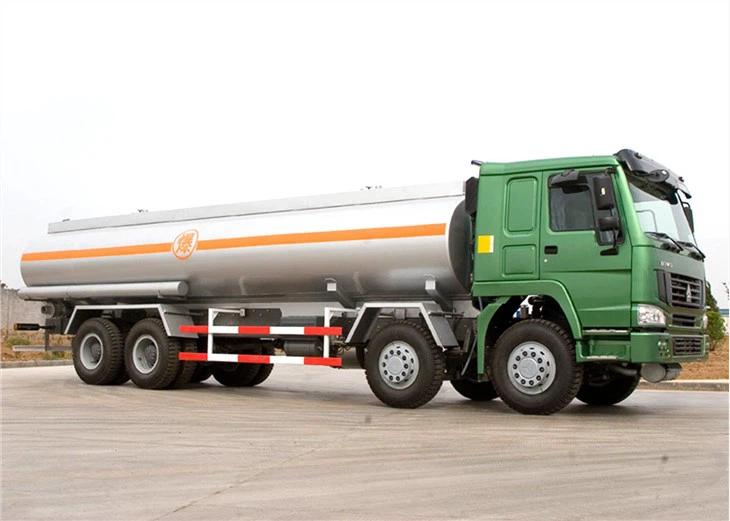
Safety regulations vary by industry and location. It’s crucial to comply with local, state, and federal regulations concerning chemical handling, safety equipment, and emergency protocols.
4. How often should maintenance be performed on mixing tanks?
Maintenance schedules can vary, but regular inspections should be conducted at least once a month, with more detailed evaluations annually or biannually.
5. Can chemical mixing tanks be automated?
Yes, many mixing tanks can be equipped with automation technologies to monitor and control mixing processes, improving accuracy and efficiency.
6. What should I do in case of a spill?
Immediately follow your facility’s emergency protocols, which typically include containing the spill, evacuating the area if necessary, and notifying the appropriate personnel.