Introduction
Induction smelters have emerged as crucial tools in various industrial applications, particularly in the fields of metalworking and metallurgy. Their efficiency, precision, and ability to work with various materials make them an intriguing topic for both professionals and hobbyists alike. This article will delve into the intricacies of induction smelters, covering their functioning, benefits, applications, and maintenance. We will also touch upon tips and real-life examples to enhance your understanding. Whether you’re considering investing in an induction smelter or simply want to broaden your knowledge, this comprehensive guide has got you covered.
What is an Induction Smelter?
An induction smelter is a type of furnace that uses electromagnetic induction to heat materials. It employs principles of electromagnetic induction to generate heat, which is then used for melting metals, alloys, and other materials. Unlike traditional furnaces that rely on combustion processes, induction smelters utilize inductive heating, making them more efficient and environmentally friendly.
How Does an Induction Smelter Work?
The core principle behind an induction smelter involves an electromagnetic coil that produces an alternating magnetic field when electricity flows through it. This magnetic field induces electrical currents, known as eddy currents, in the conductive material placed within the coil. As these currents flow through the material, they generate heat due to electrical resistance, leading to the melting of the material.
Components of an Induction Smelter
- Induction Coil: Made from copper, this coil is responsible for generating the magnetic field.
- Power Supply: Provides the electricity needed to produce the alternating current.
- Crucible: A container that holds the material being melted.
- Cooling System: Often necessary to prevent overheating of parts of the smelter.
Advantages of Induction Smelters
Induction smelters offer numerous advantages over traditional methods of melting. The most notable of these advantages include:
1. Efficiency
Induction smelters operate at higher temperatures with quicker melting times. The energy consumed is largely used for heating the metal rather than being lost to the environment.
2. Precision and Control
These systems provide better temperature control, allowing for precise melting processes, which is essential in applications such as alloy production.
3. Environmentally Friendly
Induction smelters generate fewer emissions compared to traditional combustion-based processes, making them a cleaner alternative.
4. Versatility
They can be used to melt various materials, including ferrous and non-ferrous metals, making them suitable for a wide range of applications.
5. Simplified Operation
The operation of induction smelters is relatively straightforward, allowing for automated processes and reducing the need for extensive manual labor.
Types of Induction Smelters
Various types of induction smelters cater to different industrial needs. Here are some of the most common types:
1. Coreless Induction Furnace

This type utilizes a flexible induction coil that creates a hollow area in the center, where the material is placed. It’s suitable for a wide range of materials and melting processes.
2. Channel Induction Furnace
In channel furnaces, the coil is arranged in a channel shape, allowing material to be melted continuously. This design is often utilized in foundries for large-scale operations.
3. Induction Melting Furnace
These furnaces are optimized specifically for melting operations, often featuring additional mechanisms for alloying or refining metals.
4. Induction Heating Systems
While not strictly a smelting process, these systems focus on heating materials without necessarily melting them, useful in metal treatment and preparation.
Applications of Induction Smelters
Induction smelters find applications across a wide array of industries. Here are some notable examples:
1. Metal Recycling
Induction smelters can effectively melt scrap metals with minimal contaminants, making them ideal for the recycling industry.
2. Jewelry Making
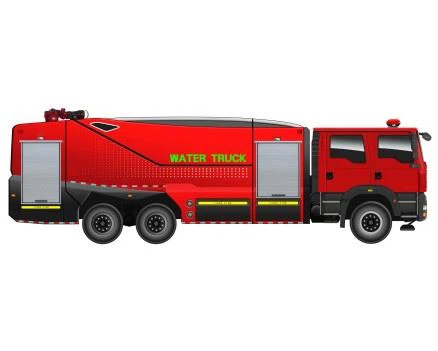
In the jewelry industry, small induction smelters allow artisans to melt precious metals for crafting intricate designs.
3. Aerospace
Induction smelting is often used to produce high-performance alloys required in aerospace components.
4. Automotive Manufacturing
Automotive parts, especially those requiring high precision, benefit from the controlled melting and alloying processes facilitated by induction smelting.
Practical Tips for Using Induction Smelters
To ensure optimal performance and longevity of your induction smelter, consider the following practical tips:
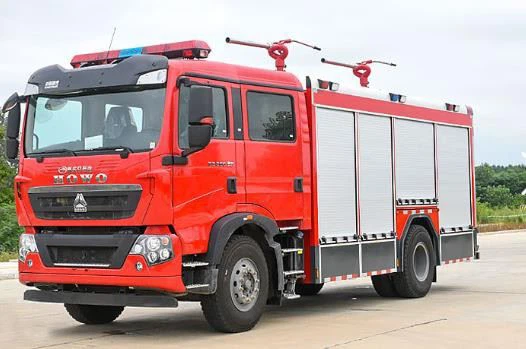
1. Proper Calibration
Regularly calibrate the machine to ensure accurate temperature readings and enhanced performance.
2. Material Preparation
Ensure that the materials are clean and free from contaminants to prevent unwanted reactions during the melting process.
3. Monitor Power Supply
A stable power supply is crucial. Consider using surge protectors to safeguard the equipment.
4. Regular Maintenance
Perform routine maintenance checks to keep components in good condition, particularly the induction coil and cooling system.
5. Safety Measures
Always adhere to safety guidelines and wear appropriate protective gear, including gloves and face shields, during operation.
Cost Considerations
The cost of an induction smelter can vary significantly based on its size, type, and application. Here’s a breakdown of cost factors:
Type of Smelter | Price Range | Main Use |
---|---|---|
Small Induction Furnace | $2,000 – $10,000 | Jewelry and small metal tasks |
Medium Induction Furnace | $10,000 – $40,000 | Metalworking and forging |
Large Industrial Furnace | $40,000 – $150,000+ | Steel and alloy production |
Common Challenges and Troubleshooting
Even with their numerous advantages, induction smelters may present certain challenges. Here are some common issues and their solutions:
1. Overheating
If components begin to overheat, check the cooling system for blockages or inefficiencies and ensure proper airflow around the unit.
2. Insufficient Melting
This may happen due to inadequate power supply or improperly sized coils. Verify that the appropriate settings are applied and upgrade as necessary.
3. Material Contamination
Contaminants can lead to poor-quality melts. Always prepare materials adequately by cleaning and sorting them before introduction into the furnace.
Future of Induction Smelting Technology
The technology behind induction smelters is continually evolving, with innovations aimed at improving efficiency and sustainability. Future trends may include:
1. Integration of AI and Automation
Artificial intelligence could play a role in optimizing operational parameters and predictive maintenance, enhancing the melting processes.
2. Hybrid Systems
Combining induction smelting with other technologies may provide additional benefits in terms of efficiency and energy savings.
3. Enhanced Recycling Capabilities
As the world moves towards more sustainable practices, advancements in induction smelting could make recycling processes even more effective, reducing waste and energy consumption.
FAQs About Induction Smelters
1. What materials can be melted in an induction smelter?
Induction smelters can melt a wide range of materials including various metals such as steel, aluminum, copper, and precious metals.
2. Is an induction smelter safe to operate?
Yes, when proper safety precautions are followed, induction smelters can be safe to operate. Always use protective equipment and adhere to manufacturer guidelines.
3. How much energy does an induction smelter consume?
The energy consumption of an induction smelter varies based on its size and operational parameters, but they are generally more energy-efficient compared to traditional furnaces.
4. Can I use an induction smelter for small-scale operations?
Absolutely! Small induction furnaces are specifically designed for hobbyists and small businesses, making them suitable for smaller production runs or projects.
5. What is the lifespan of an induction smelter?
With proper maintenance and care, induction smelters can last many years; commonly, a lifespan of 10-20 years can be expected depending on usage.
6. How do I choose the right induction smelter for my needs?
Consider factors such as the types of materials you wish to work with, the scale of operation, and the budget available. Research different models and consult with manufacturers.