Wheeler concrete is a form of ready-mix concrete that has gained attention in recent years for its unique characteristics and applications in both residential and commercial projects. This article seeks to provide a detailed analysis of wheeler concrete, its properties, advantages, applications, and more, aimed at individuals and professionals interested in modern construction techniques.
What is Wheeler Concrete?
Wheeler concrete refers to a specialized type of concrete designed for versatility and efficiency in construction projects. It is mixed on-site and transported in a wheeled container, enabling quick delivery and adaptability to various construction needs. This type of concrete is particularly beneficial for projects requiring immediate use and customized mixes.
History of Wheeler Concrete
The development of wheeler concrete can be traced back to the evolving needs in the construction industry for faster and more efficient materials. With advancements in transportation technology, the idea of delivering mixed concrete directly to the job site became feasible, leading to the modern concept of wheeler concrete.
Key Characteristics of Wheeler Concrete
Characteristic | Description |
---|---|
Versatility | Can be tailored to various structural requirements and environmental conditions. |
Portability | Transported easily to remote job sites; ready for immediate use. |
Quick Set Times | Allows for rapid completion of projects, minimizing downtime. |
Cost-Effectiveness | Reducing labor costs and transportation expenses. |
Quality Control | Can be mixed on-site with specific quality requirements in mind. |
Advantages of Using Wheeler Concrete
1. Time Efficiency
Wheeler concrete offers significant time savings during the construction process due to its ready-mix availability. It eliminates the need for lengthy hauling processes from batch plants, enabling construction teams to start work immediately.
2. Customization
Contractors can customize the concrete mix based on specific project requirements. This includes alterations in strength, insulation properties, and aesthetic qualities, providing flexibility that traditional concrete may not offer.
3. Reduced Waste
By mixing the precise amount of concrete needed for a project, contractors can significantly reduce waste, making better use of both materials and finances.
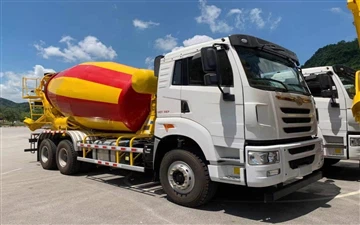
4. Consistent Quality
Wheeler concrete is produced under controlled conditions, ensuring uniformity in every batch. This level of quality control results in reliable performance and durability.
Main Applications of Wheeler Concrete
1. Residential Construction
Wheeler concrete is often used in constructing foundations, walls, and floors in residential buildings. Homeowners benefit from its efficiency and the ability to customize mixtures for specific requirements, such as insulation or aesthetic finishes.
2. Commercial Construction
In commercial projects, wheeler concrete serves essential roles in creating durable pavements, parking structures, and building frameworks. Its rapid set times help meet commercial construction deadlines.
3. Infrastructure Development
Wheeler concrete is utilized in infrastructure projects like roads and bridges, where quick application and strength are crucial. Its versatility allows it to adapt to various environmental challenges.
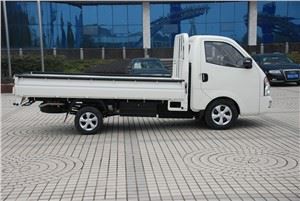
4. Decorative Applications
For aesthetic projects, wheel concrete can be mixed with pigments and additives, allowing for artistic designs in sidewalks, driveways, and landscaping features.
5. Specialty Construction Projects
Wheeler concrete is also suitable for specialty projects including arts installations, retaining walls, and ephemeral structures that require unique formulations and swift execution.
How to Use Wheeler Concrete Effectively
1. Assess Your Project Needs
The first step in utilizing wheeler concrete is to assess the project’s requirements—strength, finish, volume, and setting time. This will guide you in customizing your concrete mix.
2. Choose the Right Mix Design
Select an appropriate mix design tailored to your specific needs. Coordinates with suppliers to determine the best mix for your project’s requirements.
3. Plan for Delivery
Schedule concrete delivery times strategically to ensure that your team is ready to use the material upon arrival, minimizing potential delays.
4. Use Proper Tools and Equipment
Ensure that the necessary tools and equipment are available on site. This includes mixing tools, pumps, and finishing tools for a smooth pour and finishing process.
5. Monitor Weather Conditions
Weather plays a significant role in concrete curing. Planning pours based on weather forecasts can help avoid complications such as excessive heat or rain.
Practical Tips for Working with Wheeler Concrete
1. Trial Mixes
Before the entire project, conduct trial mixes to verify the desired properties, including workability and finish. This allows for adjustments before large batches are mixed.
2. Regular Checks
Perform regular checks on the curing process. This ensures that hydration is adequate, and the concrete achieves the desired strength effectively.
3. Post-Pour Care
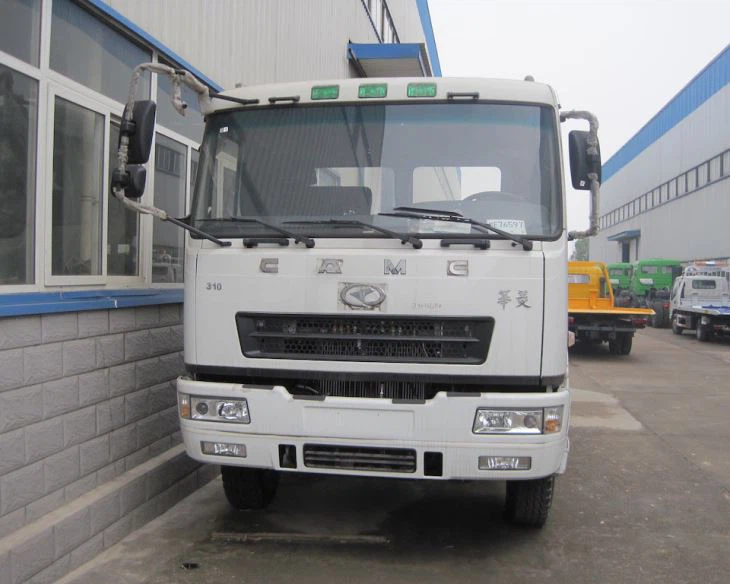
Implement proper curing methods after pouring, including the use of curing compounds or wet burlap to retain moisture, enhancing the concrete’s final performance.
Cost Considerations for Wheeler Concrete
Factors Influencing Cost | Description |
---|---|
Mix Complexity | Custom mix designs with additives and specific aggregates will increase costs. |
Project Size | Larger projects may benefit from bulk purchasing discounts. |
Transport Distance | The further the delivery, the higher the transportation costs. |
Labor Costs | Consider labor for mixing, pouring, and finishing the concrete. |
Additional Materials | Costs for reinforcement materials, finishing tools, and curing products. |
Environmental Impact of Wheeler Concrete
1. Sustainable Practices
When using wheeler concrete, consider sustainable practices such as using recycled materials in your mix and ensuring proper waste reduction to minimize the environmental footprint.
2. Energy Efficiency in Production
Utilizing locally sourced materials and efficient transport methods can reduce energy consumption associated with production and delivery.
Frequently Asked Questions (FAQ)
1. What is the difference between wheeler concrete and standard concrete?
Wheeler concrete is mixed on-site for immediate use, while standard concrete is typically batch-mixed and transported. Wheeler concrete offers quicker delivery and customization for specific projects.
2. Can I use wheeler concrete for decorative purposes?
Yes, wheeler concrete can be mixed with pigments and additives to achieve various aesthetic finishes for decorative applications like sidewalks and landscapes.
3. How long does it take for wheeler concrete to set?
The setting time can vary based on the mix, but most wheeler concrete typically sets within a few hours, allowing for relatively rapid construction processes.
4. Is wheeler concrete environmentally friendly?
Wheeler concrete can be made environmentally friendly by using recycled materials and following sustainable practices in its production and use.
5. How do I maintain wheeler concrete after it has cured?
Maintain wheeler concrete by sealing it for waterproofing, cleaning it to remove debris, and repairing any cracks promptly to ensure longevity.
6. Is wheeler concrete suitable for cold weather applications?
Wheeler concrete can be adapted for cold weather applications, but it requires additional measures, such as using insulating blankets and adjusting the mix to ensure proper curing.