Core casting is an essential method in manufacturing, playing a pivotal role in the production of complex metal parts. In this article, we delve deep into the core casting group, exploring its significance, processes, types, and practical applications, while providing useful tips and insights into the industry.
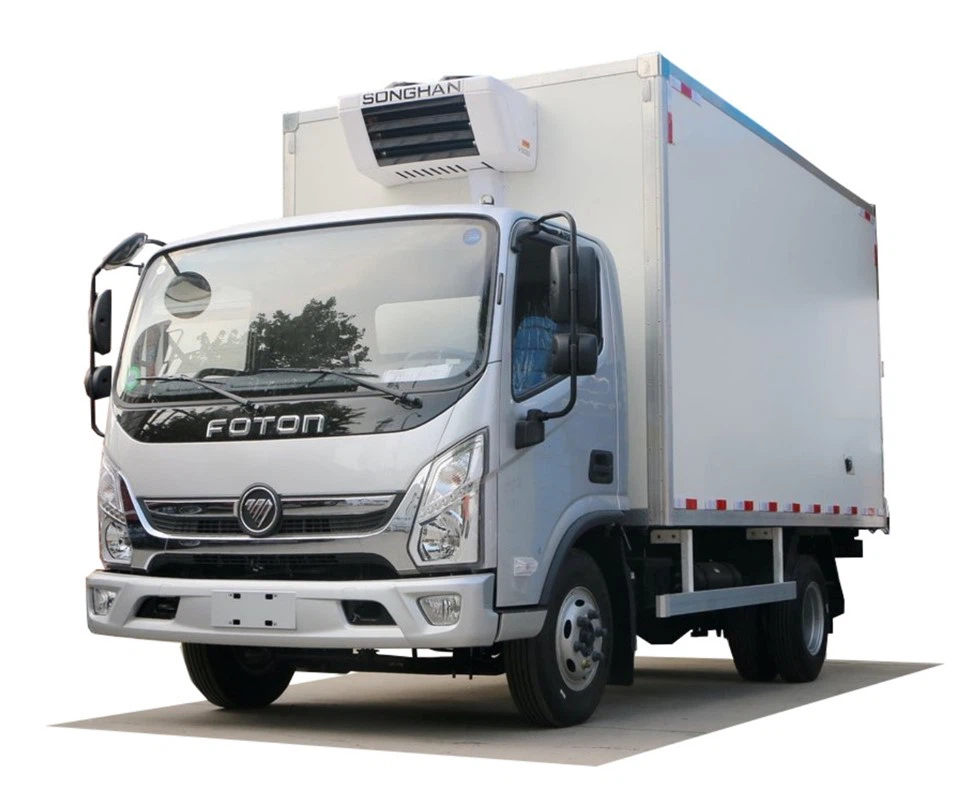
What is Core Casting?
Core casting is a specialized method used in the manufacturing of metal parts through the process of casting. It involves creating a core that shapes the internal cavities of a part, allowing for intricate designs and features that would be difficult to achieve through traditional casting methods. This technique is prolific in industries such as automotive, aerospace, and machinery manufacturing.
The Importance of Core Casting
Core casting is crucial because it enables manufacturers to produce highly sophisticated components with reduced production time. The use of cores can significantly improve product quality by ensuring uniformity and precision in the manufacturing process.
Key Benefits of Core Casting
- Enhanced design flexibility
- Cost-effectiveness for large production runs
- Improved dimensional accuracy
- Ability to produce lightweight components
- Reduced post-processing requirements
Core Casting Processes
1. Sand Casting
Sand casting is the most common core casting method, where sand is used to create molds and cores. The process involves:
- Creating a sand mold from a pattern.
- Inserting a sand core to shape the internal features.
- Pouring molten metal into the mold.
- Allowing the metal to cool and solidify before removing the mold.
2. Investment Casting
Investment casting, or lost wax casting, involves creating a wax pattern coated in ceramic. The steps include:
- Creating a wax model and encasing it in ceramic material.
- Removing the wax through heating, leaving a ceramic mold.
- Pouring in molten metal to create complex parts.
3. Die Casting
Die casting is a faster production method that uses high pressure to force molten metal into a mold. Important details include:
- Molds are typically made of steel or iron.
- It is suitable for mass production of small to medium-sized parts.
Comparative Table of Core Casting Processes
Process | Material | Cost | Production Volume |
---|---|---|---|
Sand Casting | Metal Alloys | Low | Medium to High |
Investment Casting | Metal Alloys | Medium | Low to Medium |
Die Casting | Aluminum, Zinc | High | High |
Types of Cores Used in Core Casting
1. Sand Cores
Sand cores are made using a mixture of sand and binding agents. They are preferred for their cost-effectiveness and versatility in various casting applications.
2. Metal Cores
Metal cores are made from iron or steel, providing higher strength and stability compared to sand cores. They are ideal for high-precision applications.
3. Ceramic Cores
Ceramic cores are used for casting high-temperature alloys. They can withstand extreme conditions and maintain precision in intricate designs.
Core Material Comparison Table
Core Type | Advantages | Disadvantages |
---|---|---|
Sand Core | Low cost, easy to produce | Less durable, less precise |
Metal Core | High strength, precision | Higher cost |
Ceramic Core | High heat resistance, precision | Fragile, expensive |
Applications of Core Casting
1. Automotive Industry
Core casting plays a vital role in producing engine blocks, cylinder heads, and other complex components that require internal cavities for performance and efficiency.
2. Aerospace Industry
In aerospace, core casting is used to manufacture components like turbine blades and housing structures that demand precision and lightweight materials.
3. Machinery Manufacturing
Heavy machinery components, such as gear housings and pump casings, frequently utilize core casting for their durability and structural integrity.
Best Practices in Core Casting
1. Selecting the Right Core Material
Choosing the appropriate core material based on the casting process and end-use application is critical for achieving desired results.
2. Mold Design Considerations
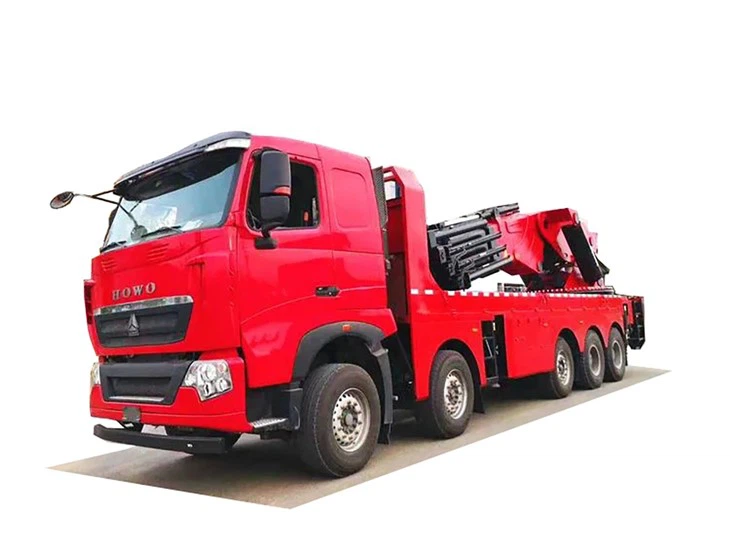
Designing molds with appropriate draft angles and surface finishes ensures easier part removal and enhances overall quality.
3. Quality Control and Testing
Implementing stringent quality control measures, including non-destructive testing methods, allows manufacturers to detect defects early in the process.
Practical Tips for Effective Core Casting
- Invest in automation for increased efficiency.
- Use advanced simulation software to improve mold designs.
- Train staff on best practices to minimize defects.
FAQs About Core Casting
1. What is the primary purpose of core casting?
The primary purpose of core casting is to create internal cavities in metal parts, enabling the production of complex shapes and designs.
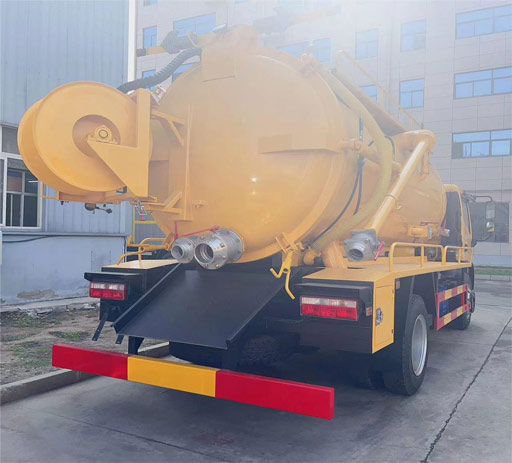
2. How does sand casting differ from die casting?
Sand casting uses a sand mold and is more suited for larger, simpler shapes, while die casting uses high pressure and is ideal for mass production of intricate parts.
3. What are the main advantages of using ceramic cores?
Ceramic cores offer high heat resistance and precise dimensional control, making them suitable for high-temperature alloys in demanding applications.
4. Can core casting be used for small-scale production?
Yes, core casting can be adapted for small-scale production, although its primary advantages shine in large-volume manufacturing.
5. What industries utilize core casting technologies?
Core casting technologies are primarily used in the automotive, aerospace, and machinery manufacturing industries.
6. How can manufacturers improve their core casting processes?
Manufacturers can improve processes by selecting the right materials, investing in automation, and implementing robust quality control measures.