Introduction
The Vactor 2100 is a highly regarded combination sewer cleaner that has proven itself invaluable in the field of urban maintenance and infrastructure management. Renowned for its efficiency and reliability, the Vactor 2100 is utilized by municipalities and private contractors alike for various tasks, from septic system cleaning to stormwater maintenance. This article will explore everything about the Vactor 2100, including its features, applications, benefits, and maintenance tips, aiming to provide a comprehensive resource for anyone interested in this versatile machine.
What is the Vactor 2100?
Overview of the Vactor 2100
The Vactor 2100 is a powerful vacuum and jetting truck designed primarily for cleaning sewer lines, catch basins, and other drainage systems. It integrates high-pressure water jetting capabilities with vacuum excavation, making it an indispensable tool for waste management professionals.
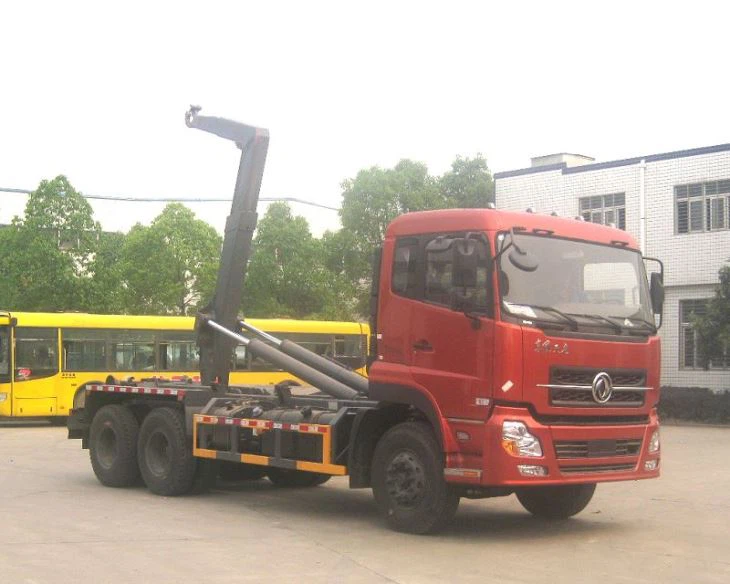
Key Features
- High-Volume Vacuum System: The Vactor 2100 features a robust vacuum system that effectively removes debris from sewer lines and catch basins.
- Water Jetting Capability: Equipped with high-pressure water jets, this truck can clear blockages, roots, and grease from pipes.
- Large Debris Tank: Designed to hold significant amounts of waste material, reducing the frequency of disposal trips.
- Enhanced Maneuverability: The compact design allows for easy movement in urban environments.
Applications of the Vactor 2100
Municipal Maintenance
Municipalities widely use the Vactor 2100 for maintaining sewer systems and storm drains. Regular maintenance prevents blockages that can lead to flooding and other issues.
Construction and Infrastructure
In construction sites, the Vactor 2100 can be used for trenching and excavation, making it easier to manage underground utilities.
Emergency Spill Response
This truck is also essential in responding to environmental spills, allowing for swift clean-up and waste removal.
Parking Lots and Paved Areas
The Vactor 2100 can efficiently remove debris and liquids from parking lots, contributing to overall safety and cleanliness.
Industrial Cleaning
Industries that require cleaning of large tanks or additional waste cannot afford downtime. The Vactor 2100 efficiently handles such tasks, ensuring minimal disruption.
Advantages of Using the Vactor 2100
Efficiency and Productivity
The combination of vacuuming and jetting capabilities allows for efficient cleaning operations, saving time and labor costs.
Environmental Benefits
By managing waste effectively, the Vactor 2100 helps protect the environment from contamination, supporting sustainable practices.
Cost-Effective Solution
Investing in a Vactor 2100 can yield significant savings in the long term, minimizing the need for multiple machines and reducing maintenance costs.
Technical Specifications
Specification | Details |
---|---|
Vacuum System Type | Positive displacement |
Water Capacity | Up to 1,200 gallons |
Debris Tank Capacity | Up to 12 cubic yards |
Vacuum Performance | Up to 4,000 CFM |
Jetting Pressure | Up to 2,000 PSI |
How to Operate a Vactor 2100
Pre-Operation Checks
- Inspect all hoses and connections for wear and tear.
- Check fluid levels, including water and hydraulic oil.
- Ensure all safety features are functional.
Starting the Vactor 2100
Starting the vehicle involves engaging all systems in a specific sequence to ensure safety and operational efficiency. Refer to the user manual for precise steps.
Operating the Vacuum System
Utilize the control panel to activate the vacuum pump and adjust air flow as needed. Ensure the debris tank is monitored during operation to avoid overflow.
Using the Water Jetting Feature
Set the desired pressure on the control panel. The jetting can be utilized to break down clogs, and the water should be directed into the lines to flush out debris.
Post-Operation Maintenance
- Clean out the debris tank thoroughly.
- Flush the jetting system with clean water to prevent buildup.
- Perform a general inspection of all components to check for wear.
Maintenance Tips for the Vactor 2100
Regular Inspections
Schedule regular inspections to identify and address issues before they become significant problems.
Fluid Changes
Change hydraulic and engine oils as recommended by the manufacturer to ensure optimal performance.
Filter Maintenance
Keep filters clean and replace them as necessary to prevent clogs and maintain efficiency.
Hose Care
Inspect hoses for any signs of damage, and replace them promptly to avoid leaks and air loss.
Cost Considerations
Initial Investment
The purchase price of a Vactor 2100 can vary based on customizations, but they generally represent a significant investment for municipalities and contractors.
Operating Costs
Cost Factor | Estimated Range |
---|---|
Fuel | $100 – $300 per week |
Maintenance | $500 – $1,500 annually |
Insurance | $1,000 – $2,500 annually |
Labor | Dependent on local wage rates |
FAQs About the Vactor 2100
1. How often should the Vactor 2100 be serviced?
Regular servicing is recommended every 500 operating hours or as stated in the manufacturer’s manual to ensure optimal performance.
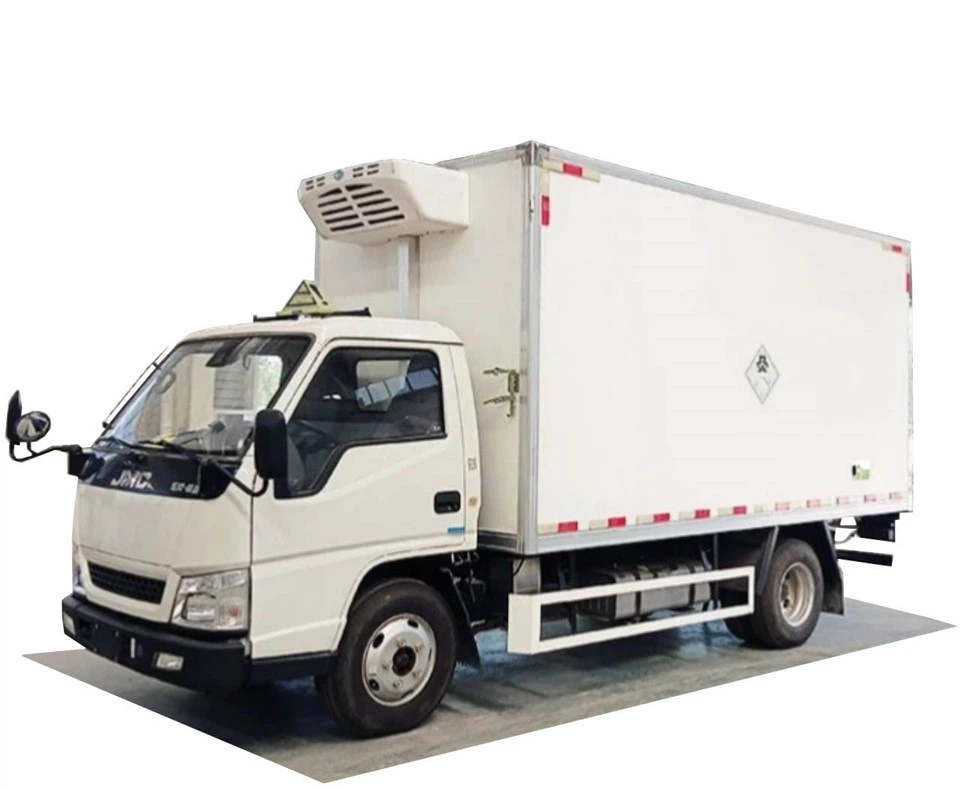
2. What type of training is required to operate the Vactor 2100?
Operators should undergo training that covers safety protocols, basic maintenance tasks, and operating procedures to ensure safe and efficient use of the machine.
3. Can the Vactor 2100 be used in residential areas?
Yes, the Vactor 2100 is designed for both urban and rural applications and can efficiently handle residential jobs, including septic and drain cleaning.
4. What should I do if I experience a malfunction while operating?
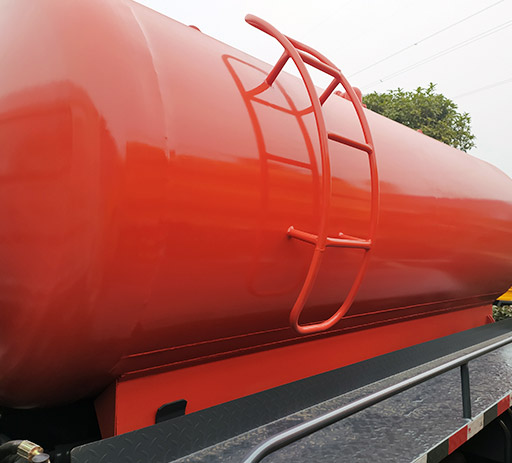
Immediately stop the operation and refer to the troubleshooting section of the user manual. If the problem persists, contact a qualified technician for assistance.
5. Is financing available for the purchase of a Vactor 2100?
Many manufacturers offer financing options; consider researching different payment plans and leasing arrangements to determine what works best for your situation.
6. What is the lifespan of a Vactor 2100?
With proper maintenance and care, the Vactor 2100 can last for several years, typically between 10 to 15 years, depending on usage and operating conditions.