Introduction
The realm of mechanical engineering has witnessed significant advancements over the years, particularly with the emergence of innovative systems such as M2 mechanical systems. These systems play a vital role in various fields, including manufacturing, automotive, aerospace, and robotics. Understanding M2 mechanical systems is essential for engineers, manufacturers, and hobbyists alike, as they pave the way for more efficient and reliable designs. This article aims to provide a detailed look at M2 mechanical systems, their applications, benefits, and how they differ from traditional mechanical systems. It is designed to be an invaluable resource for anyone interested in the fascinating world of mechanical engineering.
What is M2 Mechanical?
M2 mechanical systems refer to a specific classification of mechanical components that operate efficiently, often incorporating advanced technologies and designs. The term “M2” typically signifies the second iteration or phase of a mechanical design, emphasizing improvements in efficiency, reliability, and functionality. M2 mechanical systems can be found across various applications, from intricate machinery to simple mechanical devices.
Key Characteristics of M2 Mechanical Systems
- Enhanced Efficiency: M2 mechanical systems often rely on advanced materials and designs that enhance energy efficiency and reduce operational costs.
- Improved Reliability: Incorporating robustness in design minimizes maintenance requirements and extends the lifespan of mechanical components.
- Adaptability: M2 systems can be adapted for various applications, making them versatile solutions in engineering.
- Integration with Technology: Many M2 systems utilize digital technologies such as sensors and automation, improving their performance and adaptability.
Applications of M2 Mechanical Systems
M2 mechanical systems have diverse applications across several industries. Understanding these applications can help engineers and businesses find innovative ways to implement these systems.
1. Manufacturing
In manufacturing, M2 mechanical systems streamline production processes, enhancing the ability to produce high-quality products at a faster pace. For instance, in automated assembly lines, M2 systems can be integrated to optimize workflows and reduce waste.
2. Automotive Industry
The automotive sector employs M2 systems to improve vehicle performance and safety. Modern vehicles utilize M2 mechanical components in their braking systems, steering mechanisms, and adaptive cruise control.
3. Aerospace Engineering
Aerospace applications benefit significantly from M2 mechanical systems, where precision and reliability are paramount. M2 systems are used in aircraft engines and control systems, ensuring efficiency and safety during flight operations.
4. Robotics
In robotics, M2 mechanical systems allow for more precise movements and greater functionality. Robotic arms, for example, use advanced M2 mechanisms to perform tasks with high accuracy.
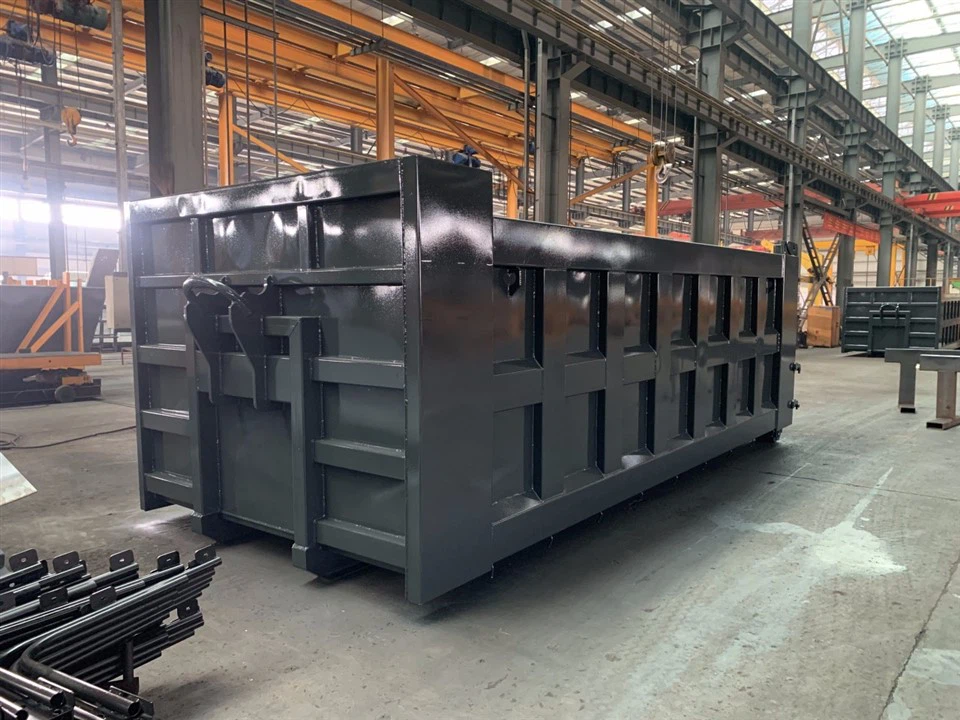
Table 1: Examples of M2 Mechanical Systems in Different Industries
Industry | Application | Benefits |
---|---|---|
Manufacturing | Automated assembly lines | Increased productivity, reduced waste |
Automotive | Braking systems | Enhanced safety, improved performance |
Aerospace | Aircraft engines | Greater reliability, efficiency |
Robotics | Robotic arms | High precision, multitasking capability |
Benefits of M2 Mechanical Systems
M2 mechanical systems provide numerous advantages that set them apart from traditional mechanical designs. Here are some of the key benefits:
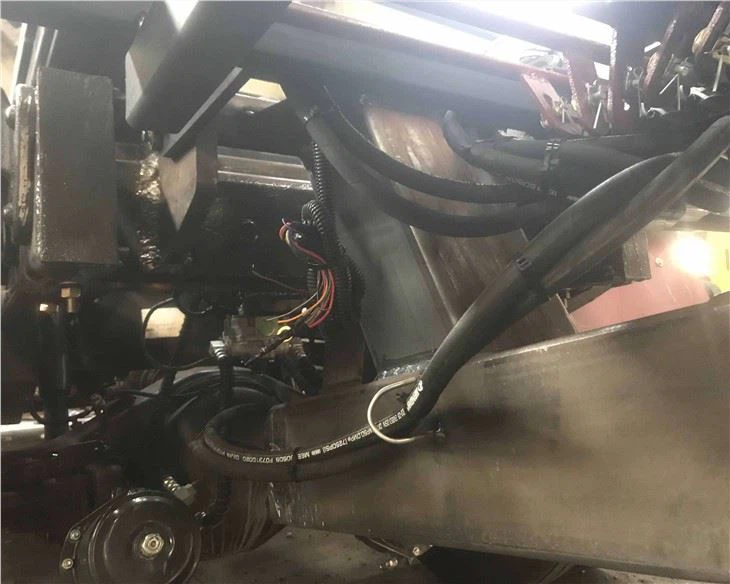
1. Cost Savings
By improving efficiency and reducing maintenance needs, M2 systems can lead to significant cost savings over time. Businesses can maximize productivity with lower operational costs.
2. Enhanced Performance
M2 systems often come with improved design features that enhance their overall performance, leading to superior output in various applications.
3. Sustainability
Sustainability is increasingly important in engineering and manufacturing. M2 mechanical systems are designed with energy efficiency in mind, which contributes to reducing carbon footprints.
4. Safety Features
Advancements in M2 systems often include safety mechanisms that minimize risks in their respective applications. This is particularly evident in the automotive and aerospace industries.
How M2 Mechanical Systems Differ from Traditional Mechanical Systems
Understanding the distinctions between M2 mechanical systems and traditional mechanical systems is crucial for professionals in the field. Here are some key differences:
1. Design Philosophy
M2 mechanical systems are designed with modern challenges in mind, incorporating advanced materials and technologies, while traditional systems may rely on older design philosophies that do not prioritize efficiency or adaptability.
2. Use of Technology
Modern mechanical systems leverage technology such as sensors, data analytics, and automation for improved performance. Traditional mechanical systems often lack these integrations.
3. Efficiency Standards
M2 systems are developed with a clear focus on energy efficiency and sustainability, intentionally designed to meet modern efficiency standards that older systems may not fulfill.
Understanding M2 Mechanical Components
To fully grasp M2 mechanical systems, it is essential to understand the components that make up these systems. Here are various components commonly found in M2 mechanical designs:
1. Gears and Pulleys
These components play a crucial role in transferring motion and force. M2 gears and pulleys are designed for optimal efficiency and durability.
2. Actuators
Actuators convert energy into motion, making them integral to M2 mechanical systems. These components often come in electric, hydraulic, or pneumatic forms, each with their specific applications.
3. Sensors
Sensors are essential for feedback control in M2 systems. They provide real-time data that systems can use to adjust operations dynamically, enhancing reliability.
Table 2: Common M2 Mechanical Components
Component | Function | Application |
---|---|---|
Gears | Transfer motion | Robotics, automotive |
Pulleys | Provide mechanical advantage | Manufacturing, lifting |
Actuators | Convert energy to motion | Aerospace, robotics |
Sensors | Provide real-time feedback | Industrial automation |
Developing M2 Mechanical Systems
Framework for Development
Developing M2 mechanical systems requires a structured approach to ensure optimal performance. Here are some practical tips for designing these systems:
1. Define Requirements
Identify the key requirements for the system, including desired performance metrics and environmental conditions. This should guide subsequent design decisions.
2. Select Appropriate Materials
Choose advanced materials that enhance durability and efficiency. Composites, lightweight metals, and advanced polymers are often favored in M2 designs.
3. Integrate Technology
Utilize digital technologies to enhance system functionality. Incorporating IoT devices, AI, and automation can significantly improve system performance and adaptability.
4. Test and Validate
Once the M2 mechanical system is developed, rigorous testing and validation must be conducted to ensure it meets the required performance and safety standards.
Best Practices for Maintaining M2 Mechanical Systems
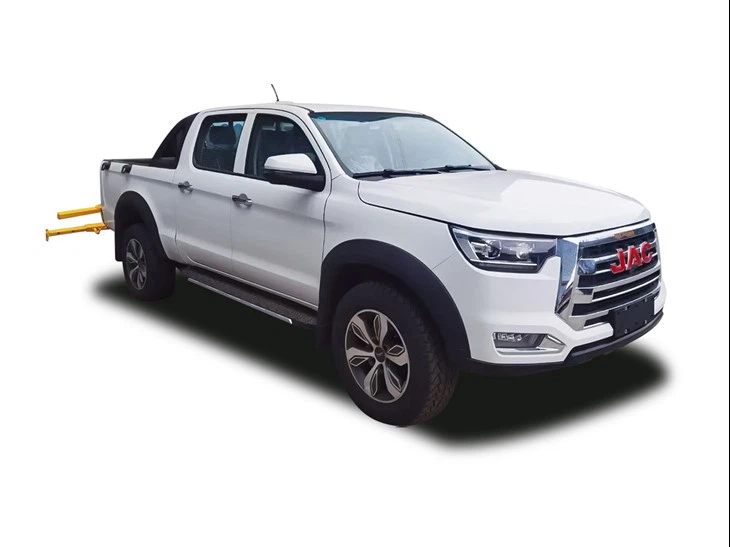
1. Regular Inspections
Conduct regular inspections to identify wear and tear early. This can prevent more extensive damage and ensure reliable operation.
2. Scheduled Maintenance
Implement a scheduled maintenance plan that includes lubrication, adjustments, and component replacements as necessary.
3. Training Personnel
Ensure that personnel are trained to operate and maintain M2 mechanical systems. Proper training can reduce the likelihood of errors that lead to system failures.
4. Document Performance Metrics
Keep thorough documentation of performance metrics to identify trends and make data-driven decisions for improvements.
FAQs about M2 Mechanical Systems
1. What industries use M2 mechanical systems?
M2 mechanical systems are utilized across various industries, including manufacturing, automotive, aerospace, and robotics, due to their efficiency and adaptability.
2. How do M2 systems differ from traditional mechanical systems?
M2 systems often incorporate advanced technologies and materials for better performance, efficiency, and safety compared to traditional mechanical systems.
3. What advantages do M2 mechanical systems provide?
Key advantages include cost savings, enhanced performance, sustainability, and improved safety features, making them attractive for modern applications.
4. What components are commonly used in M2 mechanical systems?
Common components include gears, pulleys, actuators, and sensors, all designed to improve overall system functionality.
5. How can I develop an M2 mechanical system?
To develop an M2 mechanical system, define requirements, select appropriate materials, integrate technology, and conduct thorough testing and validation.
6. What are the best practices for maintaining M2 mechanical systems?
Best practices include regular inspections, scheduled maintenance, training personnel, and documenting performance metrics to ensure reliability and performance.