Introduction to SKD Motors
SKD Motors, or Semi-Knocked Down Motors, is a term often associated with the automotive industry, particularly in the context of manufacturing and assembling vehicles. This process allows manufacturers to significantly reduce costs and time when establishing operations in a new market or enhancing existing production capabilities. In this article, we will explore the various facets of SKD Motors, including its definition, benefits, applications, challenges, and more. By the end of this comprehensive guide, you will have a well-rounded understanding of SKD Motors and how they fit into the global automotive landscape.
What Are SKD Motors?
SKD Motors refer to vehicle components that are shipped in parts and assembled in a different location from where they were manufactured. This method contrasts with Completely Knocked Down (CKD) kits, where vehicles are assembled from more extensive and complete parts. SKD typically includes sub-assemblies such as the frame, engine, and wheels. This approach simplifies logistics and lowers import duties, making it financially advantageous for manufacturers.
The Evolution of SKD Manufacturing
The concept of SKD manufacturing originated to help automobile manufacturers expand their reach into international markets. Early adopters found that by importing SKD kits, they could bypass high tariffs associated with fully assembled vehicles. The model saw significant changes over the decades, adapting to technological advancements and changing market needs.
Benefits of SKD Motors
1. Cost Reduction
The primary advantage of SKD production is its pronounced cost benefits. Importing parts as SKD kits can lower overall expenses due to reduced tariffs, shipping costs, and warehouse requirements. Companies can save significantly compared to the cost of fully assembled vehicles.
2. Market Flexibility
SKD manufacturing allows companies to adapt more quickly to changing market demands. Manufacturers can assemble vehicles based on local preferences without the need for extensive production facilities in every market.
3. Local Job Creation
Assembling SKD kits locally can create jobs in the region, contributing positively to the local economy. This benefit can enhance the company’s reputation and strengthen its social responsibility commitments.
4. Easier Compliance with Regulations
Many countries have stringent regulations regarding the import of vehicles. By assembling SKD kits locally, companies can often comply with local laws and standards, making it easier to operate in foreign markets.
Applications of SKD Motors in the Automotive Industry
Numerous automotive manufacturers utilize the SKD model to enhance their production capabilities. The following are some key applications:
1. Emerging Markets
Many automotive companies employ SKD manufacturing in emerging markets where setting up a full manufacturing plant may not be feasible initially, thus allowing for gradual investment.
2. Electric Vehicles (EVs)
With the growing EV market, manufacturers are using SKD kits to assemble electric vehicles locally, adapting to regional demands and preferences effectively.
3. Specialty Vehicles
Some manufacturers specialize in producing vehicles for specific applications, such as agricultural or commercial use. SKD manufacturing enables them to meet these niche market demands efficiently.
Challenges in SKD Manufacturing
1. Quality Control
Ensuring consistent quality across a range of assembly operations can be challenging. Manufacturers must implement strict quality control measures to maintain standards.
2. Supplier Coordination
Managing relationships with various suppliers is crucial for successful SKD operations. Timely delivery of components is essential to avoid production delays.
3. Training and Workforce Development
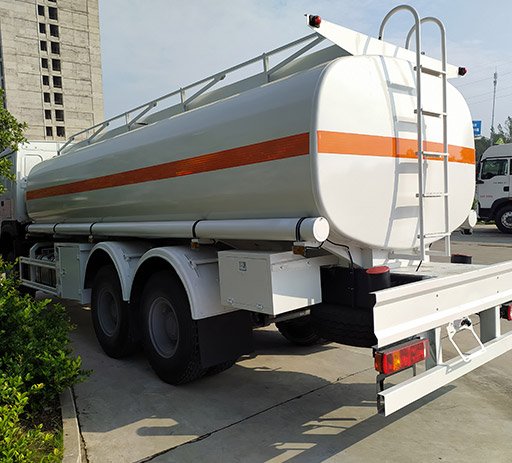
The workforce needs to be trained to assemble different vehicle types accurately. Continuous training programs help upskill employees and maintain quality standards.
Steps Involved in the SKD Process
1. Design and Development
The first step involves the design and development of the vehicle. Engineers draft plans and create prototypes to refine the vehicle’s specifications.
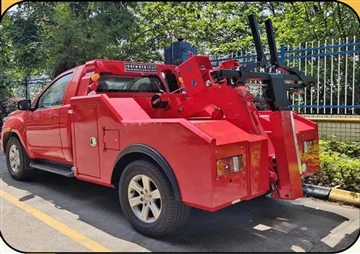
2. Manufacturing Parts
Components are manufactured, either in-house or outsourced, depending on the company’s production capabilities. Parts are then prepared for shipping as SKD kits.
3. Shipping to Assembly Plant
Once the parts are ready, they are shipped to the local assembly plant, where skilled workers will put everything together.
4. Assembly
At the assembly facility, skilled technicians assemble the vehicle based on the imported SKD kits, ensuring compliance with local standards and regulations.
5. Quality Assurance
Post-assembly, each vehicle undergoes a quality assurance process to ensure it meets corporate and industry standards.
Real-World Examples of SKD Motors
1. Toyota
Toyota has successfully implemented SKD operations in various countries, allowing them to adapt their popular models to local markets while maintaining competitive pricing. Their assembly plants in Thailand extensively use the SKD model.
2. Hyundai
Hyundai also utilizes SKD methods in different regions, particularly in emerging markets. Their assembly plants have catered to local preferences while ensuring the models comply with regional standards.
3. Honda
Honda’s operations in India demonstrate effective use of the SKD methodology to introduce models optimized for local consumers, establishing a robust market presence in the region.
Tips for Successful SKD Operations
1. Ensure Proper Planning
Meticulous planning is essential for successful SKD operations. Research market needs, establish a clear timeline, and set expectations for all stakeholders.
2. Invest in Workforce Training
Providing adequate training for staff involved in the assembly process will help maintain quality and efficiency. Regular workshops and refresher courses can keep employees updated.
3. Establish Strong Supplier Relationships
Maintaining good relationships with suppliers ensures timely delivery of components, thus avoiding delays during assembly. Open communication channels and regular reviews can help strengthen these connections.
Future of SKD Motors
As the automotive industry evolves, the SKD model continues to adapt to new trends, including electric and autonomous vehicles. Advances in technology, such as automation and robotics, could further enhance SKD operations, increasing efficiency and lowering production costs. Additionally, growing global interest in sustainable practices may lead to the development of more eco-friendly SKD methods, enhancing the overall industry’s focus on sustainability.
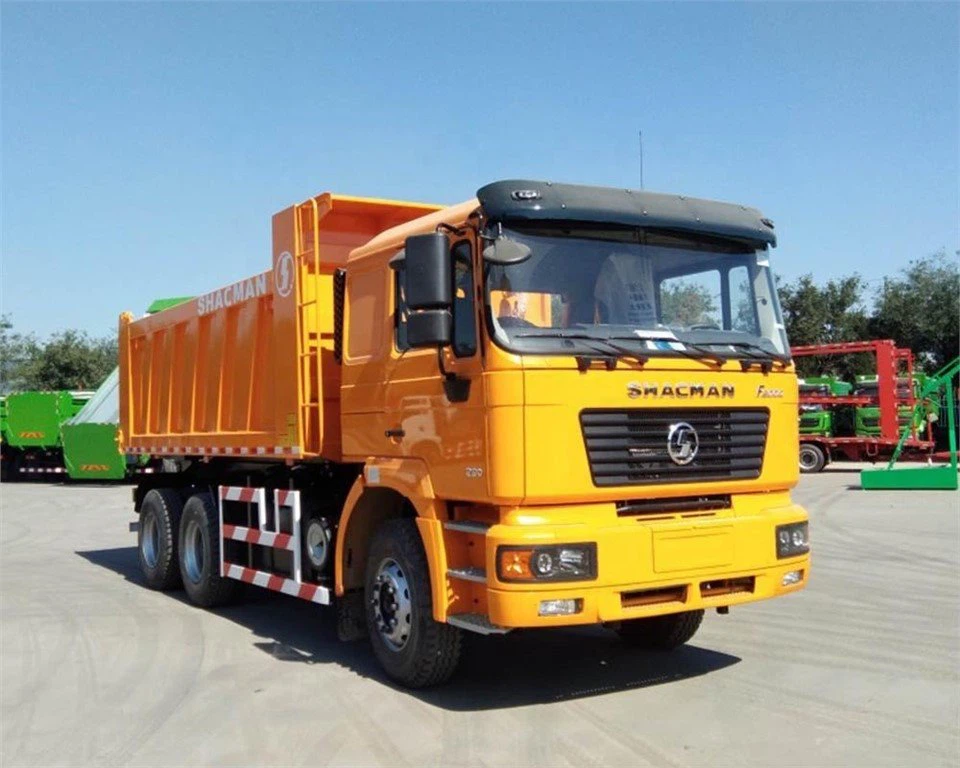
Frequently Asked Questions (FAQs)
1. What is the difference between SKD and CKD?
SKD refers to Semi-Knocked Down kits, which are partially assembled components shipped for local assembly, while CKD (Completely Knocked Down) kits include more extensive parts for a complete assembly process.
2. Are SKD Motors environmentally friendly?
SKD operations can be more environmentally friendly than full imports due to reduced shipping emissions, local assembly, and potential for utilizing local materials and labor.
3. Can any automobile manufacturer use SKD methods?
While most manufacturers can utilize SKD, its effectiveness depends on factors such as market size, local regulations, and the manufacturer’s ability to manage assembly logistics efficiently.
4. What types of vehicles are typically produced using SKD methods?
SKD methods are often used for passenger cars, electric vehicles, commercial vehicles, and specialty vehicles designed for specific applications, such as agriculture or construction.
5. How does SKD manufacturing impact local economies?
SKD manufacturing positively impacts local economies by creating jobs, boosting local suppliers, and enhancing overall economic activity through localized production and assembly.
6. What are some best practices for SKD operations?
Best practices for SKD operations include thorough planning, regular training for the assembly workforce, establishing strong supplier relationships, and maintaining quality control across all phases of production.