Introduction
Marathon compactors are vital equipment used in various industries, especially for waste management and recycling. Understanding the different parts of these machines is crucial for ensuring optimal performance and longevity. In this comprehensive guide, we will explore the essential components of marathon compactors, their functions, and how to maintain them effectively. Whether you are a business owner, maintenance personnel, or just looking to expand your knowledge, this article will provide you with everything you need to know about marathon compactor parts.
Understanding Marathon Compactors
What is a Marathon Compactor?
A marathon compactor is a machine designed to compress waste materials into manageable, compact bales. This compression not only saves space but also facilitates easier transport and recycling. They are commonly used in various settings, including commercial waste disposal sites, recycling centers, and large municipal operations.
Types of Marathon Compactors
Marathon offers a variety of compaction solutions, including stationary compactors, self-contained compactors, and vertical balers. Each type has specific parts tailored to its operational needs:
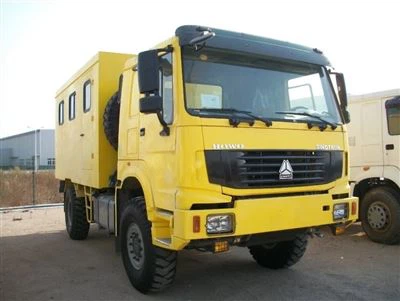
- Stationary Compactors: Typically found in fixed locations, ideal for high-volume waste.
- Self-Contained Compactors: Designed for on-site waste handling, often used by supermarkets and restaurants.
- Vertical Balers: Excellent for packaging recyclable materials like cardboard and plastics.
Key Parts of Marathon Compactors
1. Compaction Chamber
The compaction chamber is where the waste is collected and compressed. Depending on the model, this area may vary in size and shape. Proper maintenance of the compaction chamber is crucial for effective operation.
2. Platen
The platen is the flat surface that applies pressure during the compaction process. This part can become worn over time, so regular inspection is essential to ensure uniform compaction.
3. Hydraulic System
A hydraulic system powers the compaction process. Key components include hydraulic pumps, hoses, and cylinders. To maintain a fully functional system, check for leaks or signs of wear regularly.
4. Electrical Components
Electrical components, including motors and control panels, are essential for the operation of marathon compactors. Regularly inspecting these components can prevent operational failures.
5. Hopper
The hopper is the entry point for waste materials. It should be regularly cleaned and maintained to prevent blockages.
6. Safety Features
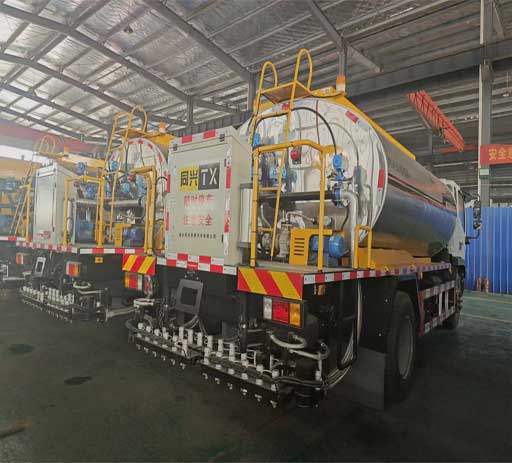
Safety features such as emergency stop buttons and safety interlocks are crucial. Regular checks ensure they function correctly to protect operators and maintenance personnel.
Importance of Using Genuine Marathon Compactor Parts
Why Choose Genuine Parts?
Using genuine marathon compactor parts guarantees compatibility, quality, and reliability. Aftermarket parts may be cheaper but often come with risks such as decreased performance and increased wear.
Where to Find Genuine Parts
Genuine marathon compactor parts are available through authorized dealers and the manufacturer’s website. It’s essential to verify the source to avoid counterfeit products.
Maintenance Best Practices
Regular Inspections
Conduct routine inspections of all parts to identify signs of wear or damage early. Focus on hydraulic lines, electrical connections, and mechanical components.
Lubrication
Proper lubrication is vital to minimize friction and wear. Follow the manufacturer’s guidelines for lubrication intervals and types of lubricants to use.
Cleaning
Regular cleaning of the compaction chamber and hopper prevents buildup that can impact the performance of your equipment.
Common Issues and Solutions
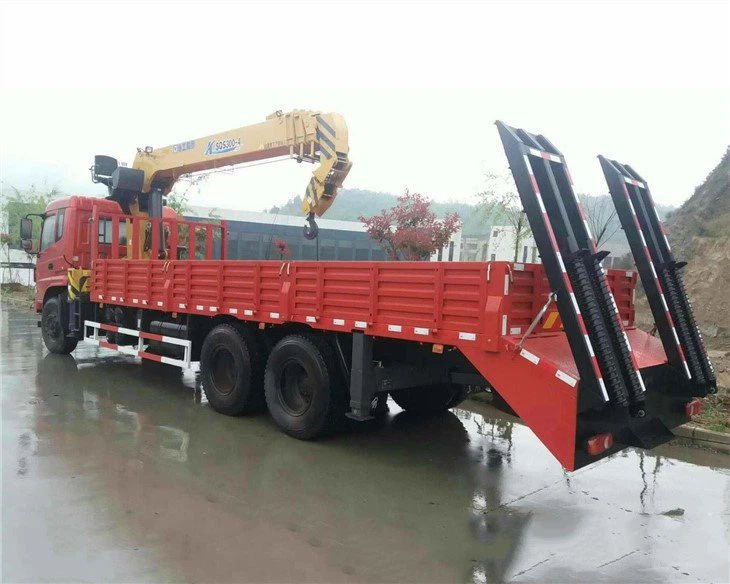
1. Leakage in the Hydraulic System
Hydraulic leaks can lead to reduced efficiency. To address this, identify the source of the leak and replace damaged hoses or seals immediately.
2. Electrical Failures
Electrical issues may manifest as the machine not starting or intermittent operation. Check the control panel and connections for loose or damaged wires.
3. Inconsistent Compaction
If the compaction is inconsistent, inspect the platen for wear and ensure the hydraulic system is functioning correctly. In some cases, recalibration may be necessary.
Practical Examples and Tips
Example 1: Efficient Waste Management
Businesses such as grocery stores can dramatically reduce their waste footprint by using marathon compactors. Implementing a regular maintenance schedule and using genuine parts ensures the longevity of the equipment, leading to better waste management practices.
Example 2: Recycling Operations
In a recycling facility, marathon compactors can streamline operations by efficiently processing materials. Knowledge about parts and their maintenance can significantly enhance operational efficiency.
Tips for Operating Marathon Compactors
- Ensure operators are trained on safety procedures.
- Establish a routine maintenance calendar to minimize downtime.
- Use the machine within its specified capacity to avoid damage.
FAQ Section
1. What are marathon compactor parts made of?
Marathon compactor parts are made from durable materials such as high-strength steel, which withstands the harsh conditions of waste compaction.
2. How often should I perform maintenance on my compactor?
Routine maintenance should be performed at least once a month. However, more frequent checks may be necessary depending on usage intensity.
3. Can I install parts myself?
While minor repairs can be done by knowledgeable personnel, it is recommended to have a certified technician install complex components to ensure proper functioning.
4. What should I do if my compactor stops working?
First, check for obvious issues such as power or hydraulic failures. If the problem persists, consult the user manual or contact a professional for assistance.
5. How can I tell if my hydraulic system needs maintenance?
Common indicators include unusual noises, leaks, or reduced compaction force. If you notice any of these signs, it’s time to perform maintenance.
6. Are aftermarket parts a good option?
While aftermarket parts are often less expensive, they may not provide the same quality and reliability as genuine marathon parts, potentially leading to more frequent repairs and lower performance.