Compactors are essential machines that help businesses efficiently manage waste, improve transportation costs, and optimize space by compressing materials. Understanding the components of these machines is vital for maintenance, repairs, and improving operational efficiency. This article explores various aspects of compactor parts, their functions, types, and maintenance tips.
What is a Compactor?
A compactor is a heavy machine used to reduce the size of waste material, making it easier and more cost-effective to manage. They are commonly used in industries such as construction, waste management, and recycling. Compactors make it possible to reduce the volume of waste by up to 75%. This process not only saves space but also minimizes transportation costs.
The Importance of Compactor Parts
The efficiency, reliability, and longevity of a compactor depend significantly on the quality and condition of its parts. Regular maintenance and timely replacement of worn-out components can prevent costly breakdowns and improve operational efficiency. Understanding the main parts of a compactor and their functions is crucial for anyone operating or maintaining these machines.
Main Components of Compactors
1. Hydraulic System
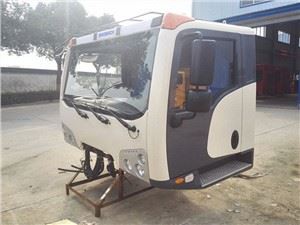
The hydraulic system is essential for the operation of most compactors. It powers the compaction mechanism and controls the machine’s movements. Key parts include:
- Hydraulic Pump: Converts mechanical energy into hydraulic energy, providing the necessary pressure to operate the compactor.
- Hydraulic Cylinders: Responsible for the compaction action, pushing the compaction plate down onto the waste.
- Hydraulic Hoses: Transport hydraulic fluid between components, ensuring efficient operation.
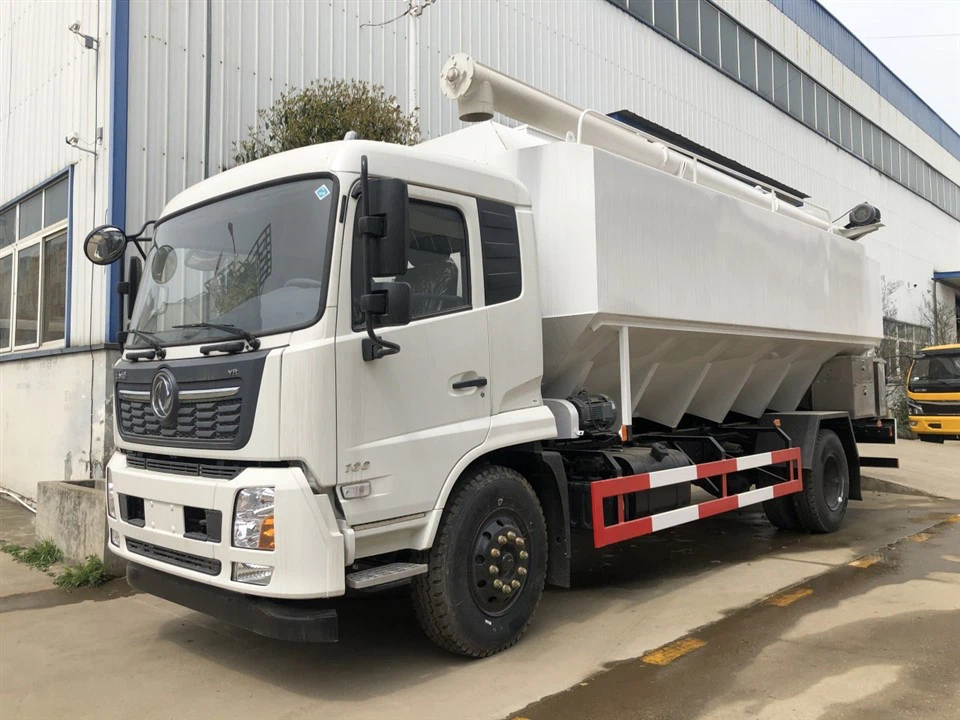
2. Compaction Plate
The compaction plate is the key component that performs the actual work of compacting the materials. Its size, shape, and weight determine how effectively it can compress various types of waste. Factors influencing its effectiveness include:
- The material of the plate (steel, plastic, etc.)
- The design of the plate, which can vary for different applications (solid waste, recyclables, etc.).
3. Drive System
The drive system powers the compactor, enabling it to move and operate effectively. Components include:
- Engine: Provides the power required to operate the compactor.
- Transmission: Transfers power from the engine to the wheels or tracks, allowing for smooth operations.
4. Controls and Instrumentation
The controls and instrumentation of a compactor are crucial for managing its operations. They include:
- Control Panel: Contains buttons, switches, and gauges used to operate the compactor.
- Sensors: Monitor the performance of the machine and alert operators to any issues.
5. Frame and Chassis
The frame serves as the backbone of the compactor, supporting all other components and ensuring stability. Key considerations include:
- Material: Typically made of steel for durability.
- Weight: Heavier frames provide greater stability during operation.
6. Tire and Wheel Systems
The tires and wheels of a compactor are crucial for mobility and performance. Attributes to consider include:
- Tread Design: Influences traction and stability on various surfaces.
- Size: Affects the compactor’s ability to maneuver in tight spaces.
Common Issues with Compactor Parts
1. Hydraulic Leaks
Hydraulic leaks can lead to decreased efficiency and increased operating costs. Common causes include:
- Worn seals and hoses.
- Improper hydraulic fluid levels.
2. Wear and Tear on Compaction Plates
Over time, compaction plates can wear down, leading to diminished performance. Regular inspections can identify issues early.
3. Engine Problems
Engine failures can halt operations. Routine maintenance, such as oil changes, can help prevent these problems.
4. Electrical Failures
Problems with the control panel or wiring can lead to operational issues. Regular inspections can help identify faulty components before they cause significant downtime.
Maintenance Tips for Compactor Parts
1. Regular Inspections
Conduct thorough inspections of all parts, focusing on hydraulic systems, compaction plates, and the engine to catch issues early.
2. Correct Lubrication
Ensure all moving parts are adequately lubricated to reduce friction and wear. Use the recommended lubricants specified in the manufacturer’s manual.
3. Hydraulic Fluid Checks
Regularly check hydraulic fluid levels and replace fluids as needed to maintain optimal performance.
4. Parts Replacement
Schedule replacements for worn or damaged parts based on the manufacturer’s recommendations to avoid unexpected breakdowns.
Choosing the Right Compactor Parts
1. Compatibility
Ensure that any parts you purchase are compatible with your specific compactor model. Refer to the service manual for exact specifications.
2. Quality vs. Price
While it may be tempting to choose cheaper parts, investing in high-quality components can save money in the long run by reducing maintenance and repair costs.
3. Supplier Reputation
Choose suppliers with a good reputation for quality and service. Reading reviews and asking for recommendations can help in this regard.
Practical Examples of Compactor Use
1. Construction Sites
At construction sites, compactors are used to manage debris and soil. They help reduce waste volume and increase efficiency in site cleanup.
2. Recycling Facilities
In recycling facilities, compactors are essential for compressing metal, paper, and plastic for efficient processing and shipping.
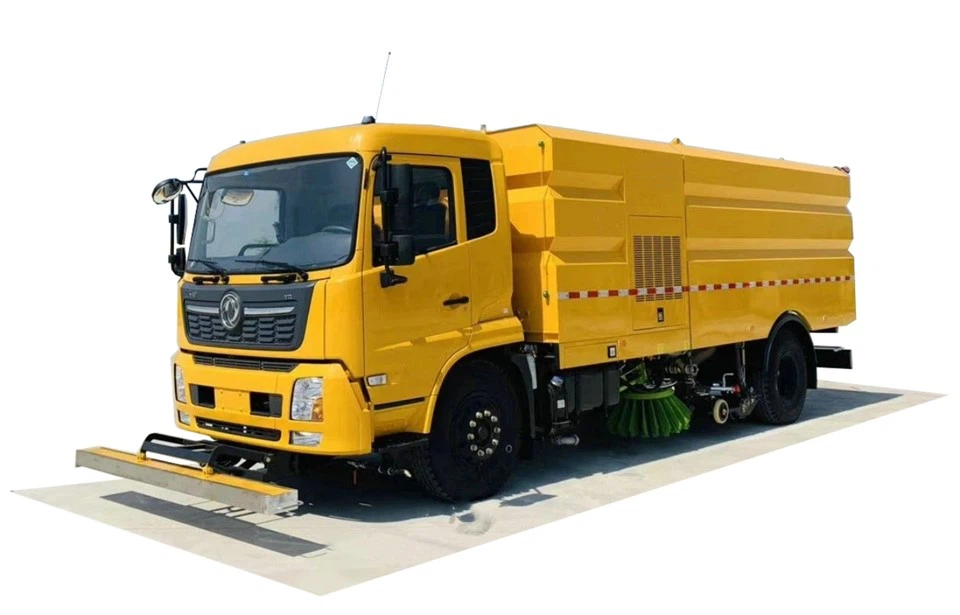
3. Waste Management Companies
Waste management companies utilize compactors to streamline the collection process and maximize container capacity.
Frequently Asked Questions (FAQs)
1. What are the common types of compactors?
Common types of compactors include stationary compactors, portable compactors, and self-contained compactors. Each design serves different waste management needs.
2. How often should I replace compactor parts?
This depends on the usage and condition of the parts. Generally, regular inspections every 6 to 12 months can help determine the need for replacement.
3. Can I repair compactor parts myself?
While some minor repairs can be done independently, it’s recommended to consult a professional for more complex issues to ensure proper functioning.
4. What is the average lifespan of compactor parts?
The lifespan of compactor parts varies greatly. For example, hydraulic hoses might last 5-7 years, while engines can last up to 10 years or more with proper maintenance.
5. How can I improve the efficiency of my compactor?
Regular maintenance, proper operation according to the manufacturer’s guidelines, and timely replacement of parts can significantly enhance the efficiency of your compactor.
6. What should I do if my compactor breaks down?
If a compactor breaks down, stop its operation immediately, identify any visible issues, and consult a qualified technician for a thorough inspection and repair.