Introduction to Ring Omatic
The term “ring omatic” refers to a specialized piece of equipment commonly used in various industries, including manufacturing, quality control, and automation. Its design and functionality can simplify multiple processes, streamlining efficiency and productivity. In this article, we will dive deep into what a ring omatic is, how it works, its applications, and valuable tips for maximizing its use. By the end of this guide, you will have a comprehensive understanding of ring omatic, allowing you to make informed decisions about its implementation.
What is Ring Omatic?
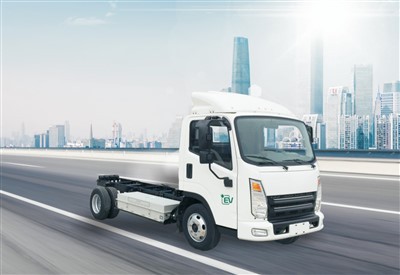
At its core, the ring omatic is a system designed for the rapid and consistent placement of rings, often used in assembly lines and manufacturing processes. The machine can automate the process of placing rings on products, ensuring accurate alignment and reducing human error. Ring omatics can handle various ring sizes, materials, and shapes, making it an essential tool in production lines where ring placement is crucial.
History and Development of Ring Omatic
The evolution of the ring omatic dates back several decades, with technology continuously advancing and improving its efficiency. Initially developed for specific applications, the modern ring omatic is adaptable and can cater to various industries’ needs, including automotive, aerospace, and consumer goods. The rise of automation in industries has allowed the ring omatic to become a standard piece of equipment on many production floors.
How Does Ring Omatic Work?
The operation of a ring omatic involves several steps, starting with ring feed, followed by placement, and finally, quality control. Understanding each step gives insight into how this machine integrates into various processes.
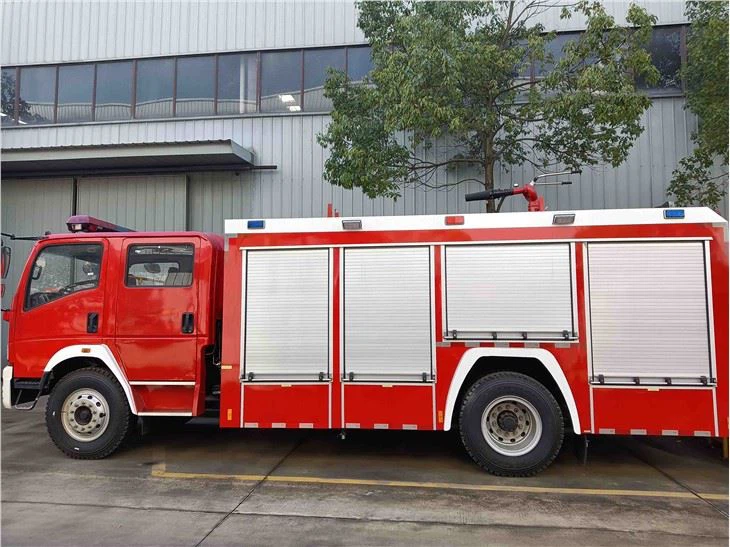
Components of Ring Omatic
- Feeder System: Automatically feeds rings into the machine.
- Placement Mechanism: Positions the ring accurately on the product.
- Control Panel: Allows operators to set parameters and monitor performance.
- Quality Check Sensors: Ensure that the rings are placed correctly and securely.
Step-by-Step Operation
- The feeder system supplies rings from a bulk source.
- The placement mechanism identifies the correct position for the ring.
- The control panel allows the operator to commence the process.
- Sensors confirm that the ring is placed accurately.
- The system outputs the finished product for further processing.
Applications of Ring Omatic
Ring omatic machines can be found in diverse industries, showcasing their versatility. Here are some of the most common applications:
1. Automotive Industry
In the automotive sector, ring omatics are essential for placing seals, bearing rings, and gaskets. By automating this process, manufacturers can increase speed while minimizing defects.
2. Aerospace Manufacturing
Aerospace components often require high precision. Ring omatics are used to ensure that critical rings fit correctly in various assemblies, enhancing overall safety and reliability.
3. Consumer Goods Production
Many consumer products require ring assemblies in packaging and closure. Ring omatics improve efficiency by expediting this assembly process, reducing labor costs.
4. Electronics Assembly
Electronics often utilize rings for insulation and protection. The ring omatic ensures that these components are placed accurately and securely during production.
Benefits of Using Ring Omatic
Implementing ring omatic systems in your production line can yield significant advantages, including:
Increased Efficiency
Automation reduces the time needed for ring placement, allowing for faster production cycles.
Reduced Labor Costs
By automating this task, companies can cut labor costs and reallocate workers to more critical areas of production.
Minimized Errors
Human error is a prevalent issue in manual ring placement. Ring omatics provide consistent accuracy, resulting in fewer defects.
Scalability
As production demands change, ring omatic systems can often be adjusted to accommodate different sizes and types of rings, providing flexibility.
Choosing the Right Ring Omatic for Your Needs
When considering a ring omatic for your production line, several factors come into play. Here’s what to keep in mind:
1. Production Volume
Identify how many units you need to produce regularly. Higher volumes may require more advanced machines with faster capabilities.
2. Ring Specifications
Different projects require different ring types. Ensure that your chosen machine can handle the sizes and materials you need.
3. Integration with Existing Systems
Your ring omatic should easily integrate into your current production line without causing significant downtime or requiring extensive modifications.
4. Cost Considerations
Budget constraints are essential to consider. Invest in a ring omatic that offers a balance between performance and cost.
Practical Examples of Ring Omatic Usage
To clarify the versatile applications of ring omatic, let’s explore some practical examples:
Example 1: Automotive Assembly Line
In an automotive plant, a ring omatic is employed to insert oil seals in engine assemblies. The machine retrieves a seal from the feeder, aligns it during placement, and confirms through sensors that it is correctly seated. This process dramatically reduces overall assembly time, contributing to faster vehicle production rates.
Example 2: Appliance Manufacturing

An appliance manufacturer uses a ring omatic to place rubber gaskets around the doors of refrigerators. By automating this task, they not only speed up assembly but also ensure a consistent seal quality, which is vital for energy efficiency.
Maintenance Tips for Ring Omatic
Maintaining your ring omatic is crucial for optimal performance. Here are some practical maintenance tips:
1. Regular Cleaning
Keep the machine clean to prevent debris from affecting operation. Schedule regular cleaning sessions based on production volume.
2. Periodic Inspections
Conduct periodic inspections of mechanical parts and sensors to identify wear and tear. Replace any worn components immediately to prevent costly downtime.
3. Software Updates
If your ring omatic model features software control, keep the system updated to benefit from the latest features and security improvements.
4. Operator Training
Ensure that all operators receive proper training on the machine’s operation and maintenance requirements to maximize efficiency and safety.
Frequently Asked Questions About Ring Omatic
1. What types of rings can a ring omatic handle?
A ring omatic can handle various types of rings, including rubber, metal, and plastic, depending on the machine’s specifications.
2. Is a ring omatic suitable for low-volume production?
While ring omatics excel in high-volume production, some models can be adjusted for low-volume applications as well.
3. How much does a ring omatic cost?
The price of a ring omatic can vary significantly based on features, capabilities, and manufacturer. Entry-level models may start at a few thousand dollars, while advanced machines can cost tens of thousands.
4. Can a ring omatic be customized for specific production needs?
Many manufacturers offer customization options, allowing businesses to tailor their ring omatic to meet specific production requirements.
5. How do I know when to replace my ring omatic?
Consider replacement if maintenance costs become prohibitive, the machine fails to meet production demands, or newer technology offers significantly improved performance.
6. What are the common issues faced with ring omatic machines?
Common issues include misalignment during ring placement, sensor failures, and mechanical jams. Regular maintenance can help prevent these problems.