Introduction
The term “SKD” appears in various contexts and industries, often leading to confusion about its meaning and implications. This article aims to clarify the meaning of SKD, explore its diverse usage across different fields, and provide practical examples and tips for better understanding. You will gain insight into why understanding SKD is essential in today’s world, whether you are involved in manufacturing, technology, or international trade.
What Does SKD Stand For?
The Basic Definition of SKD
SKD stands for “Semi Knocked Down.” It refers to a shipping and manufacturing practice where products are shipped in a partially assembled state. This method allows companies to save on shipping costs and tariffs while facilitating easier assembly once the products reach their destination.
Historical Context of SKD
The concept of SKD emerged in the manufacturing sector as globalization increased. Companies realized that by disassembling products into SKD units, they could adapt to local markets more effectively. This practice gained popularity in industries such as automotive, electronics, and machinery production.
Applications of SKD in Different Industries
1. Automotive Industry
In the automotive sector, SKD assembly is a common practice. Car manufacturers often ship parts from various countries to assembly plants in target markets. This method allows for localized production and reduces costs related to tariffs and transportation.
Example:
A company might manufacture car parts in Germany, ship them as SKD kits containing minimal assembly requirements, and then assemble them in India. This process adheres to local laws while making the products more affordable for the Indian market.
2. Electronics Industry
Electronics manufacturers also utilize SKD shipping. By sending products in a semi-assembled format, companies can reduce shipping volume and optimize logistics.
Example:
A company producing televisions might send screens and circuit boards separately to a local assembly plant, where they can be combined to create finished products. This practice minimizes shipping costs and ensures compliance with regional regulations.
3. Machinery and Equipment
In industrial machinery, the SKD method allows manufacturers to supply complex equipment efficiently. The machinery is disassembled into components, reducing shipping weight.
Example:
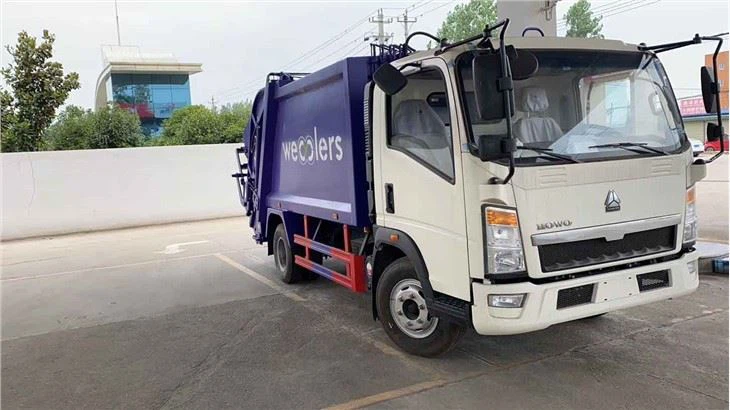
A manufacturer of construction equipment may ship parts of bulldozers as SKD kits to regional dealers. The assembly done locally leads to lower operating costs in distribution.
Advantages of SKD Manufacturing
1. Cost Savings
By shipping SKD kits, companies significantly reduce shipping costs. The reduction in volumetric space also cuts down on freight charges.
2. Flexibility in Assembly
SKD allows manufacturers to adapt to local market demands and regulations. Different configurations can be assembled based on regional preferences.
3. Compliance with Local Regulations
SKD shipping can facilitate compliance with local laws and tariffs, which can vary from one region to another. This leads to avoidance of hefty tariffs on fully assembled products.
4. Increased Speed to Market
By utilizing SKD, companies can accelerate the time it takes for products to reach the market. The assembly phase can be managed much faster than a lengthy supply chain process of fully assembled items.
Disadvantages of SKD Manufacturing
1. Requires Specialized Knowledge
Although SKD assembly offers many advantages, it does require specialized knowledge and skills. Workers must be trained to assemble complex kits effectively.
2. Risk of Damaged Parts
Shipping parts in a semi-assembled state may lead to higher risks of transport damage. Companies need to invest in adequate packaging to minimize losses.
3. Dependence on Logistics
Successful implementation of SKD heavily relies on efficient logistics and distribution networks. Companies must ensure that their logistics strategies are robust to avoid delays.
SKD vs. CKD: Understanding the Difference
What is CKD?
CKD stands for “Completely Knocked Down,” where products are shipped in a fully disassembled state, requiring comprehensive assembly at the destination. This differs from SKD, where products are only partially assembled.
Comparison Table: SKD vs. CKD
Criteria | SKD | CKD |
---|---|---|
Assembly Level | Semi-assembled | Fully disassembled |
Shipping Costs | Lower due to reduced size | Lower but potentially more assembly time |
Complexity in Assembly | Moderate | High |
Market Compliance | Quick adaptation | Longer process |
Challenges of Implementing SKD
1. Quality Control
Ensuring the quality of parts in SKD kits can be challenging. Companies need to implement robust quality checks throughout the shipping process.
2. Standardization Issues
Different assembly plants may have varying standards, leading to inconsistencies in the final product. Standardizing processes can be crucial to maintaining quality.
3. Inventory Management
Companies must effectively manage inventory to ensure they have the right parts available for assembly. Poor inventory management can lead to delays and increased costs.
Future Trends in SKD Manufacturing
1. Smart Manufacturing
With advancements in smart manufacturing technologies, SKD processes are likely to become more efficient and faster. IoT (Internet of Things) will play a critical role in streamlining assembly lines.
2. Sustainability Practices
As sustainability becomes more critical, SKD could help reduce carbon footprints by optimizing logistics and minimizing waste. Companies are increasingly focusing on eco-friendly packaging and shipping methods.
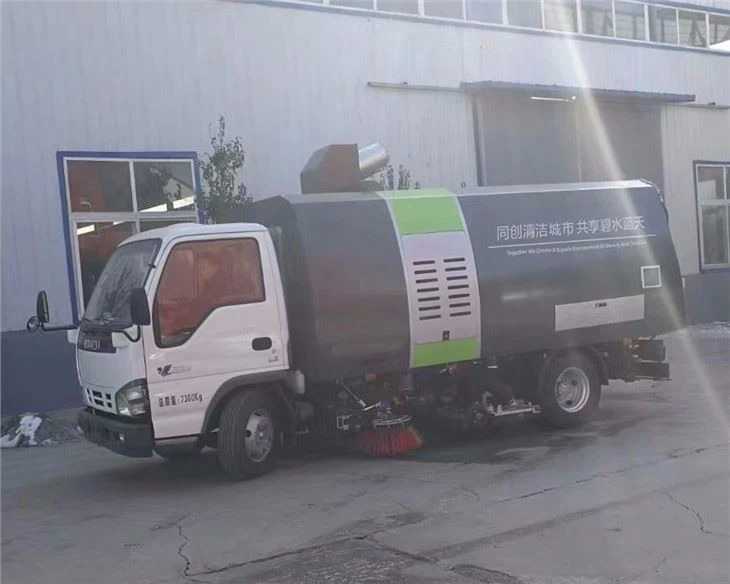
3. Local Sourcing of Components
There’s a growing trend toward local sourcing of components for SKD kits, enhancing local economies and reducing transportation emissions further.
Practical Tips for Successfully Implementing SKD
1. Invest in Training
Ensure your workforce is well-trained in SKD assembly processes. Regular training sessions can foster skills and improve assembly efficiency.
2. Enhance Quality Control
Implement a robust quality control process for incoming SKD kits. Regular checks can prevent minor issues from becoming significant problems.
3. Supply Chain Partnership
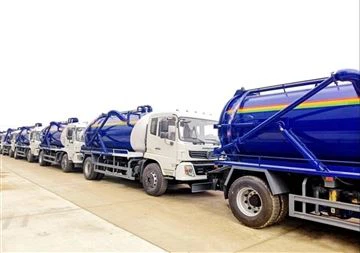
Cultivate strong relationships with suppliers and logistics partners. Effective communication will handle potential disruptions swiftly.
4. Use Technology for Inventory Management
Utilize software tools to keep track of inventory levels and manage SKD parts effectively. This can minimize delays due to stockouts.
FAQs about SKD Meaning and Usage
1. What is the difference between SKD and SKT?
SKT stands for “Semi Knocked Town,” which is similar to SKD but typically involves more extensive disassembly and assembly requirements. The terms are often used interchangeably, but SKT can denote a slightly different focus.
2. Can SKD be used in the pharmaceutical industry?
While SKD is not commonly associated with pharmaceuticals, certain areas may utilize similar concepts for distributing complex machinery related to manufacturing.
3. How does SKD affect tariffs and taxes?
Shipping products in SKD format can significantly reduce tariffs and taxes since partially assembled products may be classified differently than fully assembled goods.
4. What are the most common sectors using SKD?
The automotive, electronics, and machinery sectors widely adopt SKD due to the cost and logistical benefits it offers.
5. Is SKD suitable for small businesses?
Yes, SKD can be beneficial for small businesses, particularly those looking to optimize shipping costs and respond quickly to market needs. However, resources for assembly and training must be available.
6. How can I learn more about implementing SKD in my business?
You can learn more through workshops, online courses, and industry conferences focused on supply chain management and manufacturing processes.