Vacuum tanks are integral components in various industrial and automotive applications. They provide a means of collecting, storing, and utilizing vacuum energy for efficiency in processes such as waste management, fuel injection, and more. Understanding vacuum tank parts can enhance maintenance, troubleshooting, and overall performance.
What is a Vacuum Tank?
A vacuum tank is a sealed container designed to hold a gas or liquid at a pressure less than that of the atmosphere. This negative pressure is essential for a variety of applications, including vacuum-assisted material handling and environmental waste management.
How Vacuum Tanks Work
Vacuum tanks function by creating a controlled vacuum environment, which allows for the movement of liquids or gases through suction. This is accomplished by removing air or vapor from the tank, leading to a drop in pressure inside the tank.
Key Components of Vacuum Tanks
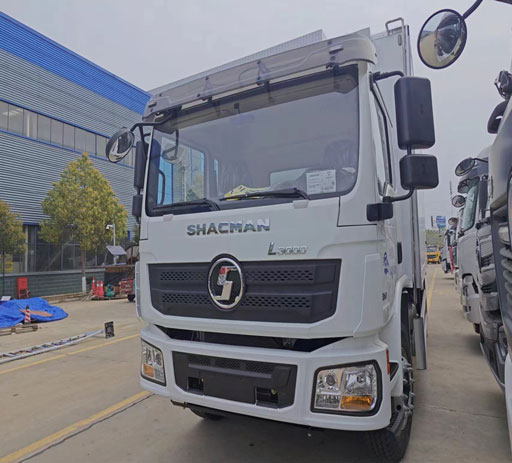
Understanding the various parts of vacuum tanks is crucial for their proper operation. Here are some of the essential components:
1. Tank Body
The tank body is the primary structure of the vacuum tank, usually constructed from materials like metal or reinforced plastic to withstand external pressure and the contents within.
2. Vacuum Pump
The vacuum pump is responsible for creating the vacuum within the tank by removing air or vapor. There are various types of vacuum pumps, including:
- Rotary vane pumps
- Diaphragm pumps
- Scroll pumps
3. Pressure Relief Valve
This valve is a safety feature that prevents the tank from over-pressurizing. If the internal pressure exceeds a certain limit, the valve opens to release gases, ensuring the tank’s integrity.
4. Inlet and Outlet Ports
Inlet and outlet ports allow substances to flow into and out of the tank. These ports must be designed to prevent leakage and maintain the vacuum integrity of the tank.
5. Level Indicators
Level indicators help monitor the amount of liquid or material inside the vacuum tank. They can be mechanical or electronic, providing real-time data on tank contents.
6. Fittings and Hoses
Fittings and hoses connect the vacuum tank to various systems and components. They must be durable and able to handle the vacuum conditions without collapsing.
Materials Used in Vacuum Tanks
The materials utilized in the construction of vacuum tanks play a pivotal role in their effectiveness and longevity. Key materials include:
1. Steel
Steel is a robust choice for vacuum tanks due to its strength and ability to withstand high pressures. It is commonly used in industrial vacuum tanks.
2. Aluminum
Aluminum is lightweight and resistant to corrosion, making it a suitable option for smaller vacuum tanks in automotive applications.
3. Plastics
Plastics may be used in vacuum tanks for specific applications where chemical resistance and lightweight properties are required, such as in laboratory settings.
Common Applications of Vacuum Tanks
Understanding the applications of vacuum tanks can help industrial professionals and end-users to appreciate their importance. Here are some common uses:
1. Waste Management
Vacuum tanks are employed to collect and transport waste materials in areas such as septic systems and sewage treatment facilities.
2. Water Treatment
In water treatment plants, vacuum tanks play a role in sedimentation and filtration processes, aiding in the purification of water supplies.
3. Fuel Systems
Vacuum tanks are essential in the fuel systems of vehicles, where they assist in fuel delivery to the engine by creating the necessary suction.
Maintenance Tips for Vacuum Tanks
Proper maintenance of vacuum tank parts is crucial for optimal performance. Here are some tips:
1. Regular Inspections
Conduct regular inspections of all parts, including valves and hoses, to identify signs of wear or damage early.
2. Clean Components
Periodically clean the tank and all connected components to remove any residue that could affect performance.
3. Monitor Pressure Levels
Maintain and monitor the appropriate pressure levels within the tank using pressure gauges or electronic monitoring systems.
Challenges and Solutions in Vacuum Tank Operations
While vacuum tanks are crucial, they can present several challenges. Addressing these issues effectively requires understanding their causes and solutions.
1. Leakage Issues
Leakage can compromise vacuum integrity. Regularly check fittings, valves, and seals for wear and replace them as needed.
2. Mechanical Failures
Mechanical failures of components such as pumps can lead to downtime. Implementing a routine maintenance schedule can help mitigate this risk.
3. Pressure Imbalance
Pressure imbalances can lead to inefficient operation. Ensure that pressure relief valves are functioning correctly to prevent over-pressurization.
Innovations in Vacuum Technology
The field of vacuum technology is constantly evolving, with innovations aimed at improving performance and efficiency:
1. Advanced Monitoring Systems
Smart technology allows for real-time monitoring of vacuum systems, enabling immediate detection of issues and enhancing maintenance strategies.
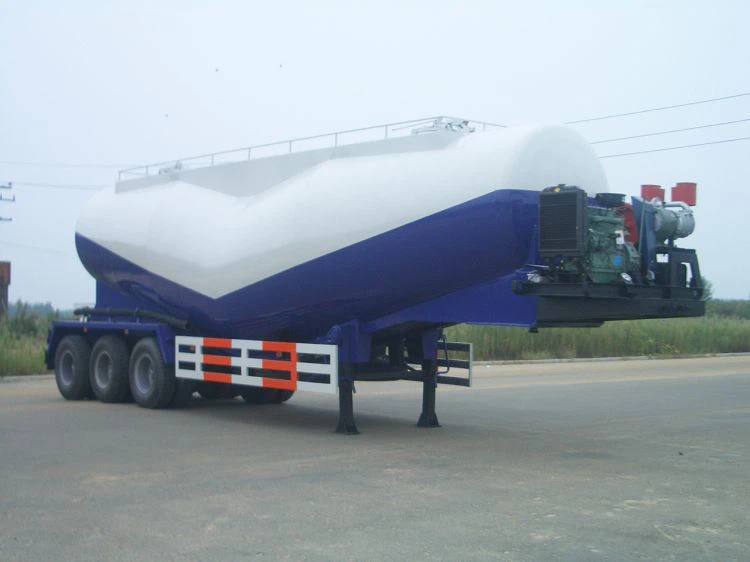
2. Eco-Friendly Materials
Innovative materials that are both lightweight and environmentally friendly are being developed for use in vacuum tanks, promoting sustainability in industrial processes.
3. Enhanced Pump Designs
New designs in vacuum pump technology aim to provide more efficient energy use, reducing operating costs and environmental impact.
Understanding Regulations and Standards
It is crucial for industries using vacuum tanks to adhere to various regulations and standards:
1. Environmental Regulations
Many regions have stringent environmental regulations governing waste management and emissions, which can affect vacuum tank design and operation.
2. Safety Standards
Compliance with safety standards ensures that the vacuum tank operates safely, protecting workers and the environment.
FAQs
1. What materials are vacuum tanks commonly made from?
Vacuum tanks are typically made from steel, aluminum, or various plastics, depending on the application and requirements.
2. How do I know if my vacuum tank has a leak?
Signs of leakage include irregular pressure readings, inconsistent performance, and visible signs of wear or damage at fittings and seals.
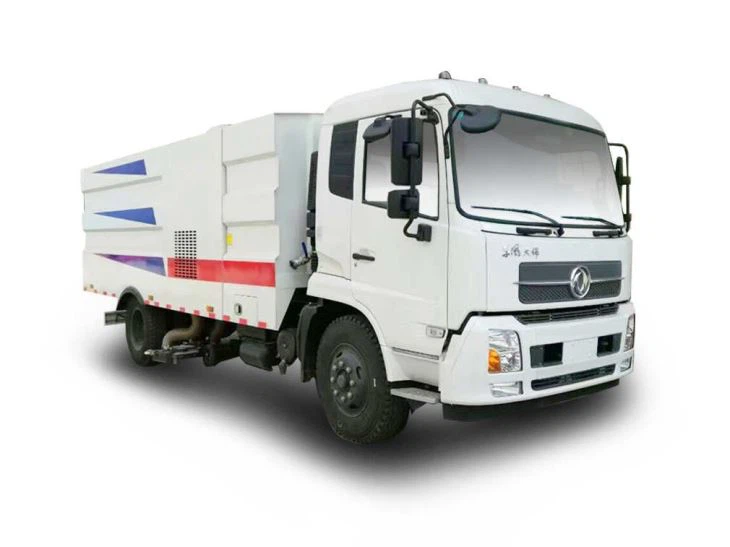
3. Can vacuum tanks be used in corrosive environments?
Yes, but they must be constructed from corrosion-resistant materials or coated to prevent damage from harsh chemicals.
4. What is the role of a vacuum pump in a vacuum tank?
The vacuum pump is responsible for removing air from the tank, creating the negative pressure necessary for its operation.
5. How can I maintain my vacuum tank effectively?
Regular inspections, cleaning, and monitoring of pressure levels are essential for effective maintenance of vacuum tanks.
6. Are there new technologies improving vacuum tank efficiency?
Yes, advancements in smart technology, eco-friendly materials, and pump designs are all contributing to improved vacuum tank efficiency and sustainability.