Introduction
In today’s fast-paced world, waste management has become an essential component for businesses and municipalities alike. One of the key innovations in waste management is the vertical compactor. Designed to optimize space and enhance efficiency, vertical compactors play a crucial role in reducing the volume of waste. This article explores the various aspects of vertical compactors, including their benefits, types, features, maintenance tips, and answers to frequently asked questions. Whether you’re a business owner looking to improve your waste management practices or simply curious about vertical compactors, this guide will provide you with comprehensive insights.
What is a Vertical Compactor?
A vertical compactor is a machine designed to compress waste materials into a tight, manageable block. This type of compactor operates vertically, allowing it to be more space-efficient compared to horizontal compactors. By reducing the size of waste, vertical compactors can significantly lower disposal costs and increase recycling rates, making them an essential tool for businesses in various industries.
Benefits of Using Vertical Compactors
Utilizing vertical compactors offers numerous benefits, including:
- Space Efficiency: Vertical compactors require less floor space, making them ideal for locations with limited room.
- Cost Savings: Reduced waste volume leads to lower transportation and disposal costs.
- Increased Recycling: Compaction can help separate recyclables, promoting sustainability.
- Improved Safety: By consolidating waste, vertical compactors minimize the risk of injury from loose waste materials.
Types of Vertical Compactors
Vertical compactors can be categorized based on their design and application. Below are the most common types:
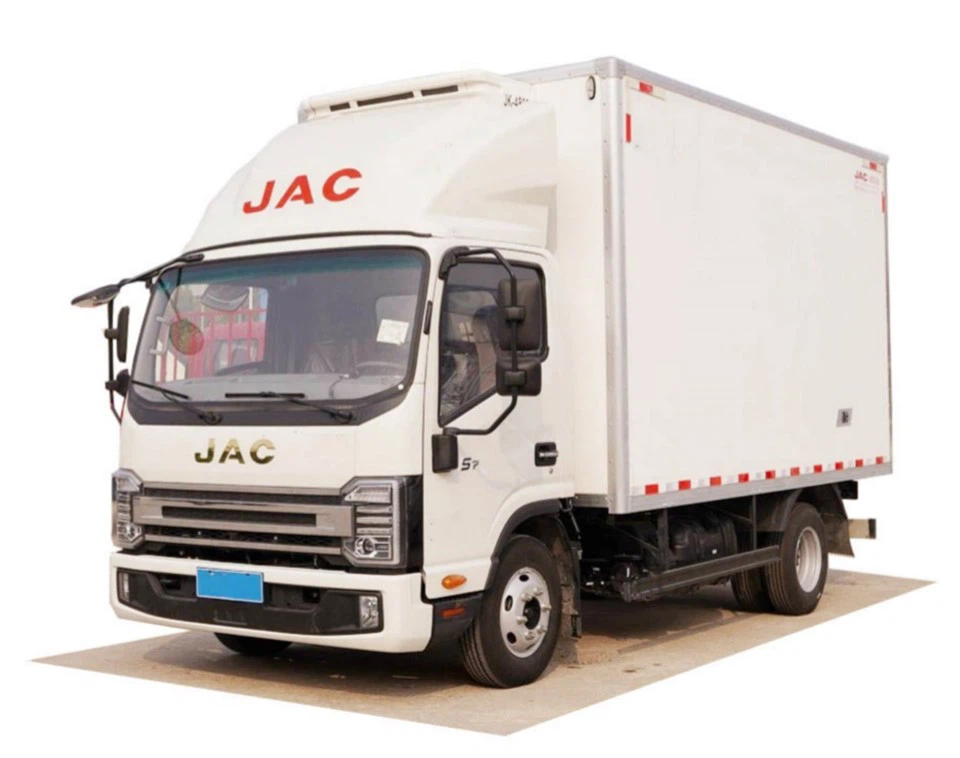
1. Stationary Vertical Compactors
These compactors are typically installed at a fixed location and are designed to handle large volumes of waste. They are best suited for businesses that generate a significant amount of waste.
2. Portable Vertical Compactors
Portable vertical compactors are designed for temporary use and can be moved from one location to another. They are ideal for events or seasonal operations.
3. Self-Contained Vertical Compactors
This type of compactor includes a built-in container to hold compacted waste. They are often used for wet waste and are designed to reduce odors and leachate.
4. Hook-Lift Compactors
Hook-lift compactors can be easily transported using a hook-lift truck. They are ideal for businesses that require flexibility in their waste disposal methods.
Essential Features of Vertical Compactors
When choosing a vertical compactor, consider the following essential features:
Power Source
Vertical compactors can operate using electric, hydraulic, or a combination of both power sources. Electric models are often quieter, while hydraulic models offer greater strength.
Compaction Ratio
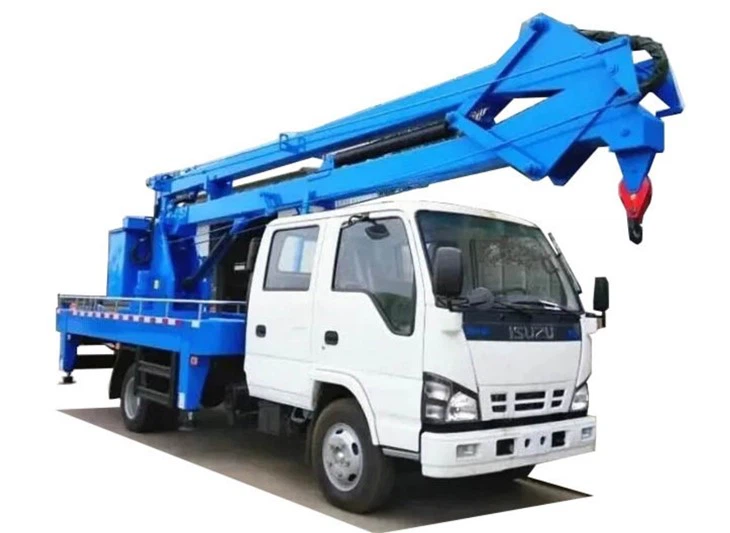
The compaction ratio indicates how much the compactor can reduce the waste volume. Higher ratios mean greater efficiency and cost savings.
Container Size
The size of the container impacts how much waste can be held before it needs to be emptied. Selecting the right size is crucial for efficiency.
Safety Features
Look for compactors with built-in safety features such as automatic shut-off, emergency stops, and safety interlocks to prevent accidents.
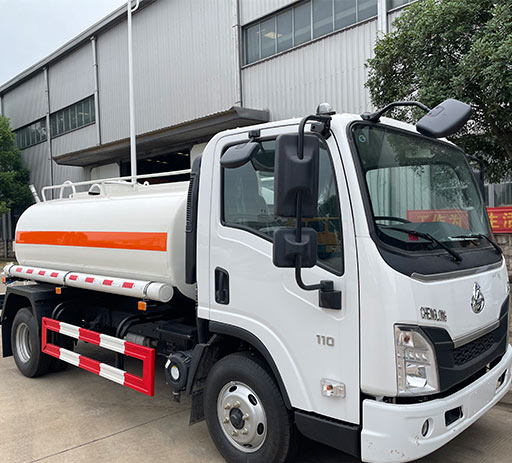
Maintenance Tips for Vertical Compactors
Regular maintenance is key to ensuring the longevity and efficiency of your vertical compactor. Here are some practical tips:
1. Regular Inspections
Conduct routine inspections to check for signs of wear or damage. Look for leaks, loose bolts, or electrical issues.
2. Clean the Compactor
Keep the compactor clean to prevent odors and maintain hygiene. Use appropriate cleaning agents to remove any stuck waste.
3. Lubrication
Ensure moving parts are properly lubricated to reduce friction and prevent deterioration.
4. Follow Manufacturer Guidelines
Always refer to the manufacturer’s instructions for maintenance schedules and procedures.
Practical Examples of Vertical Compactors in Use
Vertical compactors can be found in various industries. Here are a few practical examples:
1. Retail Stores
Retail chains utilize vertical compactors to efficiently manage cardboard and plastic waste generated from packaging. The compactors help keep storerooms organized and reduce recycling costs.
2. Restaurants
Restaurants often use self-contained vertical compactors for wet waste. These compactors minimize odors and ensure a cleaner environment in kitchen areas.
3. Construction Sites
Construction companies employ portable vertical compactors to manage debris and waste on temporary job sites. This keeps the site neat and safe for workers.
4. Manufacturing Facilities
Manufacturers use stationary vertical compactors to handle large volumes of scrap materials, improving workflow efficiency and minimizing waste costs.
Costs Associated with Vertical Compactors
The cost of vertical compactors can vary significantly based on several factors. Here are some key elements to consider:
Initial Purchase Price
The purchase price for vertical compactors can range from $3,000 to over $10,000, depending on size, features, and brand.
Maintenance Costs
Regular maintenance may incur additional costs, including servicing and replacement parts. Budget for ongoing maintenance to ensure optimal performance.
Operating Costs
Electricity and disposal fees can add to the operating costs. Consider these factors when calculating the total cost of ownership.
Choosing the Right Vertical Compactor for Your Needs
Selecting the right vertical compactor involves assessing your specific requirements. Consider the following:
Volume of Waste
Identify the amount and type of waste generated to choose a compactor with the appropriate size and capacity.
Space Availability
Evaluate the available space in your facility to determine whether a stationary or portable compactor would be the best fit.
Types of Waste
Different vertical compactors are better suited for various types of waste. Understanding your waste stream will help with your choice.
Budget Considerations
Set a budget not only for the purchase but also for ongoing maintenance and operating expenses.
Frequently Asked Questions (FAQ)
1. What materials can be compacted using a vertical compactor?
Vertical compactors can handle a variety of materials, including cardboard, plastics, paper, and certain types of metal. However, it’s essential to check the manufacturer’s guidelines for specific waste compatibility.
2. How often should I maintain my vertical compactor?
Maintenance frequency largely depends on usage. Regular weekly or monthly inspections are recommended, with more detailed maintenance performed bi-annually or annually.
3. Can a vertical compactor reduce the volume of wet waste?
Yes, self-contained vertical compactors are specifically designed to manage wet waste while minimizing odors and leachate.
4. What is the average compaction ratio for vertical compactors?
Most vertical compactors provide a compaction ratio of 4:1 to 10:1, depending on the type of material being compacted.
5. Are there safety features in vertical compactors?
Yes, many vertical compactors come equipped with safety features such as emergency stop buttons, safety interlocks, and automatic shut-off functions to protect operators.
6. Is it necessary to train staff to operate a vertical compactor?
Yes, proper training is essential to ensure safe and efficient operation, helping to minimize the risk of accidents and equipment damage.