PTR balers are essential machinery in the waste management and recycling industries. They provide an efficient solution for compacting and processing waste materials, contributing to both environmental sustainability and operational efficiency. This article delves deep into the functionalities, benefits, and types of PTR balers available in today’s market.
What is a PTR Baler?
PTR balers are designed to compress various types of waste materials into compact bales for easier handling, storage, and transportation. The name “PTR” stands for “Pneumatic Tie Recycling”, reflecting the baler’s method of bundling waste using pneumatic mechanisms. These machines are particularly effective in processing cardboard, plastics, and other recyclables.
How PTR Balers Work
The Mechanism Behind PTR Balers
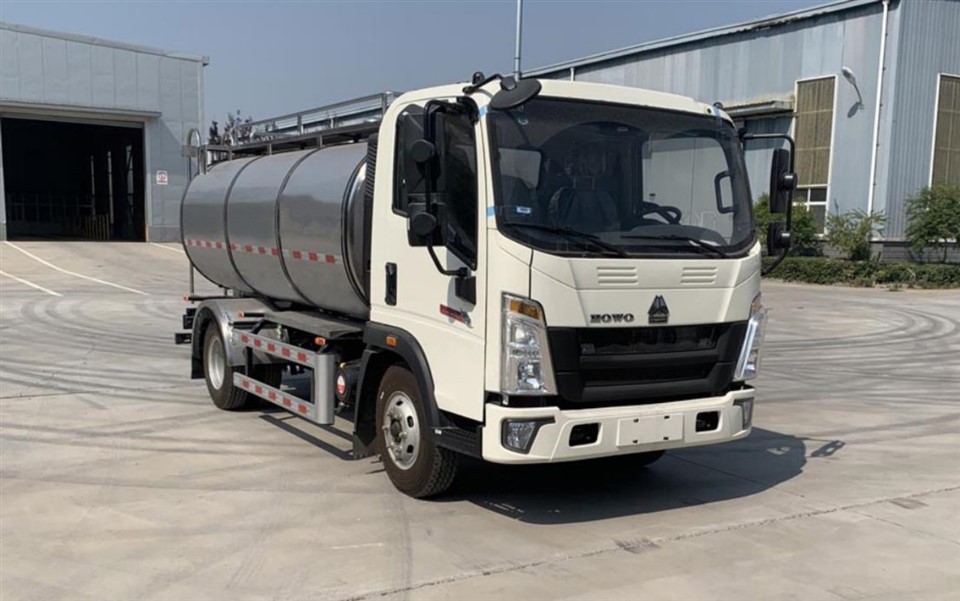
PTR balers operate via a hydraulic system that applies substantial pressure to waste materials, effectively compressing them into dense bales. The process consists of several key stages:
- Feeding: Waste materials are loaded into the baler’s chamber.
- Compression: Hydraulic cylinders exert pressure on the materials, compacting them.
- Tying: Once the bale is compacted, it is tied using wires or straps to keep it together.
- Discharge: The finished bale is ejected from the machine for further handling or storage.
Types of Waste Processed
PTR balers can efficiently compact various materials, including:
- Cardboard
- Plastic bottles
- Paper waste
- Aluminum cans
- Textiles
Benefits of Using PTR Balers
Enhanced Space Efficiency
One of the most significant advantages of PTR balers is their ability to significantly reduce the volume of waste. This reduction leads to substantial savings in storage space, making waste management more streamlined and organized.
Cost Efficiency
By compacting waste into bales, businesses can cut down on disposal costs. More compacted waste reduces the frequency of pick-ups, lowering transportation expenses. Additionally, some waste materials can be sold as recyclables, providing an extra income stream.
Improved Safety and Cleanliness
Balers help keep workspaces tidy and safer. By dealing with waste in a compact form, the risk of accidents related to clutter is minimized. Furthermore, less spillage means a cleaner environment, which is beneficial for both employees and customers.
Understanding Different Models of PTR Balers
Vertical Balers
Vertical balers, also known as downstroke balers, compress waste from the top down. They are usually smaller in size and suitable for businesses with moderate waste output.
Horizontal Balers
Horizontal balers are used for larger volumes of waste. They process waste in a horizontal position, often offering higher efficiency for businesses that generate large quantities of recyclables.
Choosing the Right PTR Baler for Your Business
Assessing Your Waste Output
Before selecting a PTR baler, it’s crucial to analyze your waste generation patterns. Knowing the type and volume of waste will help you choose a machine that best meets your needs.
Space Requirements
Consider the available space within your facility. Vertical balers typically require less floor space than horizontal balers, which can impact your decision based on operational constraints.
Operational Tips for Using PTR Balers
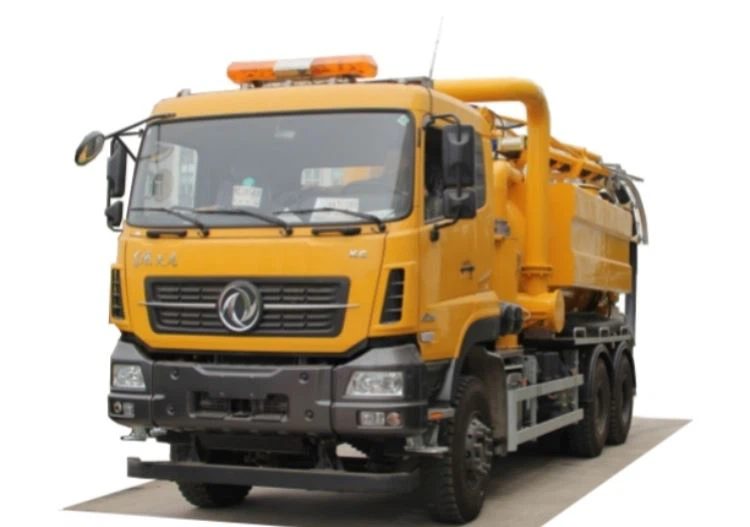
Regular Maintenance
To ensure longevity and optimal performance of your PTR baler, regular maintenance is essential. Schedule preventative maintenance checks and follow the manufacturer’s guidelines for care.
Proper Loading Techniques
Loading the baler correctly can enhance its efficiency. Distribute the waste evenly within the chamber and avoid overloading, which can strain the machine and lead to malfunctions.
Training Staff
Ensure your staff is properly trained on operating the baler. Knowledgeable operators can minimize safety risks and maximize the efficiency of the machine.
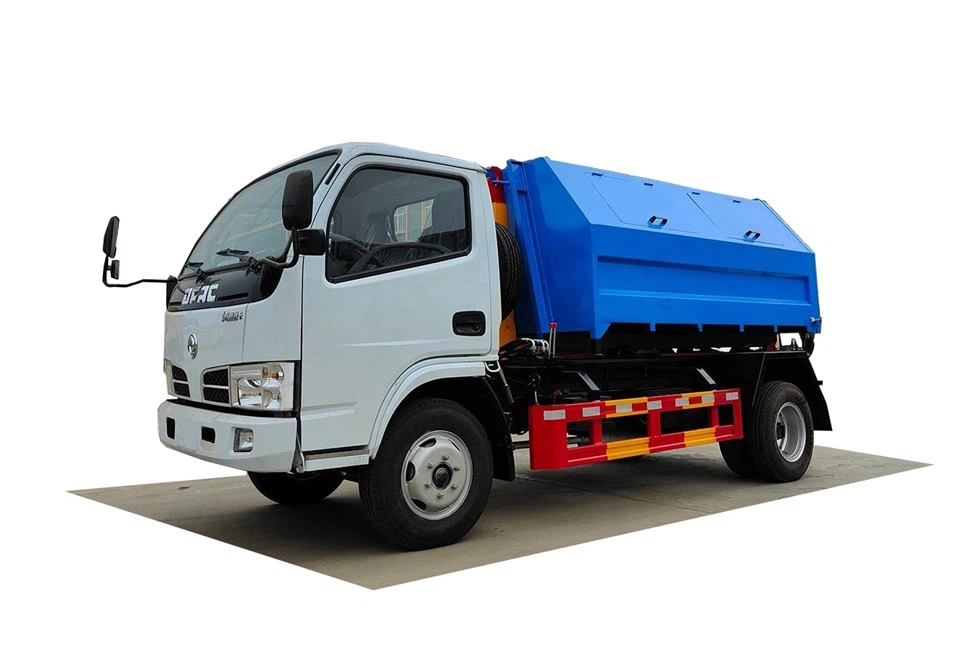
Environmental Impact of PTR Balers
Promoting Recycling
PTR balers play a crucial role in promoting recycling initiatives. By facilitating the easy compression and storage of recyclable materials, they contribute to a more sustainable waste management solution.
Reducing Carbon Footprint
Increased recycling rates lead to fewer materials being sent to landfills, directly reducing greenhouse gas emissions associated with waste decomposition.
Case Studies: Successful Implementation of PTR Balers
Case Study 1: A Local Retail Store
A local retail store implemented a vertical PTR baler to manage their cardboard waste. This reduced waste volume by 85%, freeing up valuable storage space and resulting in significant cost savings in disposal fees.
Case Study 2: Manufacturing Facility
A manufacturing facility switched from manual waste handling to using a horizontal PTR baler. This change allowed for a more systematic approach, leading to a 70% reduction in labor costs associated with waste management.
Common Misconceptions About PTR Balers
Myth 1: PTR Balers Are Too Expensive
While the initial investment can seem substantial, the long-term savings in waste disposal costs often outweigh these expenses. Additionally, many businesses find new revenue streams through recycling.
Myth 2: PTR Balers Are Complicated to Operate
Modern PTR balers are designed with user-friendliness in mind. With proper training, most staff can learn to operate these machines without difficulty.
Frequently Asked Questions About PTR Balers
1. How much space do I need for a PTR baler?
The space required depends on the type of baler. Vertical balers need less floor space, while horizontal balers take up more room due to their larger size. Assess your waste volume to determine the best fit for your space.
2. Can PTR balers handle all types of waste?
While PTR balers are highly versatile, they are most effective for processing recyclable materials such as cardboard, plastics, and paper. Specific models may have limitations, so check the manufacturer’s guidelines.
3. What is the average lifespan of a PTR baler?
The lifespan of a PTR baler can vary based on usage and maintenance practices, but with proper care, many balers can last over a decade.
4. Is operator training necessary for using a PTR baler?
Yes, operator training is highly recommended. Proper training ensures the safe and efficient operation of the baler and minimizes the risk of accidents.
5. What are the maintenance requirements for PTR balers?
Regular maintenance includes checking hydraulic fluid levels, inspecting for wear on parts, and cleaning the machine. Following the manufacturer’s maintenance schedule will help prolong the life of the baler.
6. Are there any safety risks associated with using PTR balers?
As with any heavy machinery, there are potential safety risks. Operators should be trained on safety procedures, wear appropriate protective gear, and operate the machine according to guidelines to mitigate these risks.