In the world of logistics and manufacturing, the term “semi knock down” (SKD) frequently appears, especially concerning the assembly and transportation of products. This article aims to provide a thorough understanding of semi knock down processes, their benefits, and practical applications in various industries.
What is Semi Knock Down?
Semi knock down refers to a method of assembling products where the goods are disassembled into parts or components for easier transportation. Unlike completely knocked down (CKD) products, which are completely disassembled and require full reconstruction, SKD products are often pre-assembled to some extent. This ensures that they are not only cost-effective to transport but also easier to assemble upon reaching their destination.
How Semi Knock Down Works
The Process of SKD
The process of utilizing the semi knock down method can be broken down into several key steps:
- Design and Planning: Manufacturers design products that can be easily disassembled into components.
- Production: The products are produced and partially assembled at the factory.
- Disassembly: Products are disassembled into SKD kits, minimizing the amount of space they will occupy during transportation.
- Transport: The SKD kits are shipped to the destination, where they are reassembled for final use.
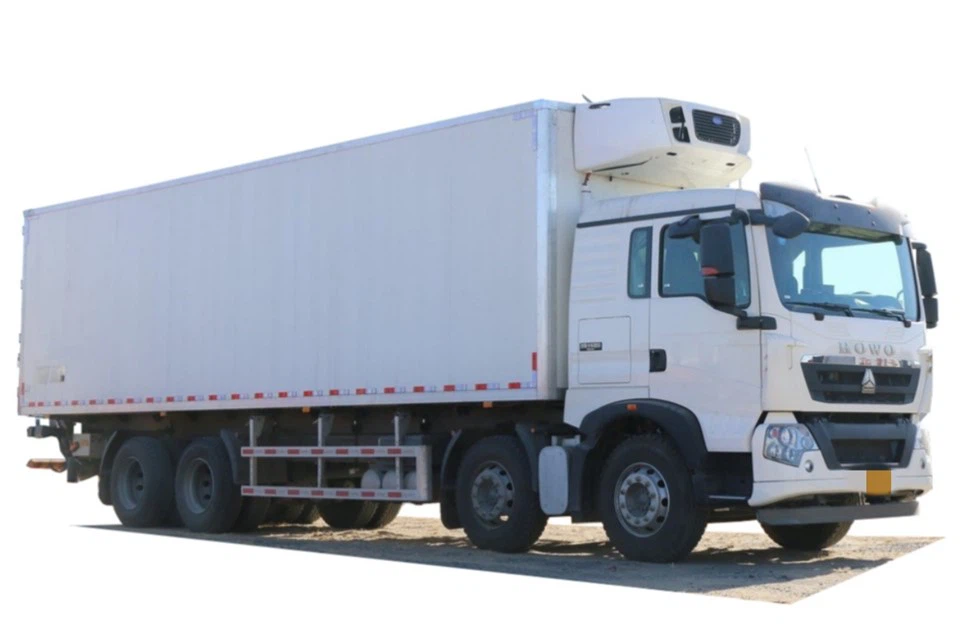
Components of a Semi Knock Down Kit
A semi knock down kit typically includes:
- Major components (e.g., engine, chassis, body panels)
- Essential assembly tools
- Instruction manuals or assembly guides
Benefits of Using Semi Knock Down
Cost-effectiveness
One of the primary advantages of semi knock down is the cost savings in logistics. With reduced shipping dimensions and weight, transportation costs are significantly lower.
Space Efficiency
Semi knock down kits occupy less space compared to fully assembled products. This space-saving feature allows businesses to transport more units at once, leading to higher efficiency.
Flexibility in Assembly
SKD provides manufacturers the flexibility to assemble products according to local specifications and standards, catering to the needs of different markets.
Industries That Use Semi Knock Down
Automotive Industry
The automotive industry has widely adopted semi knock down processes. Cars are often shipped overseas in SKD format, allowing for local assembly in target markets.
Example: International Car Brands
Many international car manufacturers, such as Toyota and Honda, utilize SKD kits to build cars in different countries, reducing import duties and taxes.
Furniture Industry
The furniture sector also benefits from semi knock down techniques. Flat-pack furniture, which must be assembled by the customer, is an excellent example of SKD.
Example: IKEA
IKEA is renowned for its flat-pack furniture delivered in SKD form, allowing for cost-effective shipping and easy transportation.
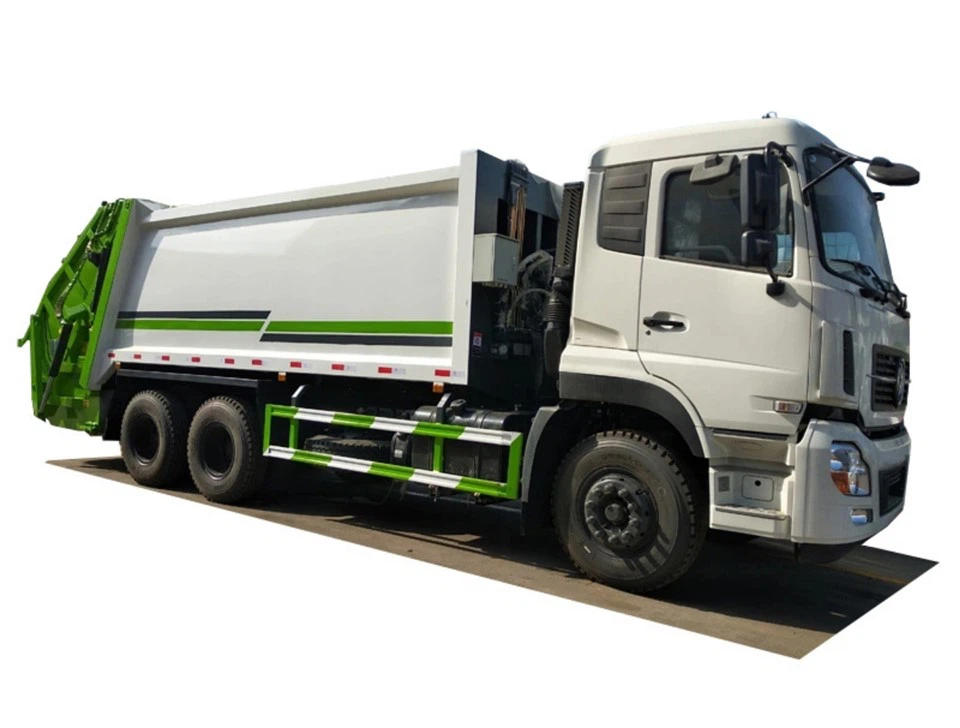
Electronics Sector
Electronics companies sometimes use SKD techniques to make transporting products like televisions and computers more manageable.
Example: Laptop Manufacturing
Some laptop manufacturers deliver components to local assembly plants worldwide, where they are put together as finished products.
Challenges of Semi Knock Down Methods
Quality Control
Ensuring quality control during the assembly of semi knock down products can be challenging, as it requires consistent oversight and standards across different manufacturing locations.
Skilled Labor Requirements
SKD kits require skilled labor for successful assembly, which can be a barrier in regions lacking a skilled workforce.
Practical Tips for Implementing Semi Knock Down
1. Evaluate Market Demand
Before implementing the semi knock down strategy, assess the local demand for products and the capacity to assemble them effectively.
2. Develop Comprehensive Assembly Manuals
Ensure assembly manuals are clear, concise, and include diagrams to aid in the assembly process, particularly for complex products.
3. Invest in Quality Control
Establish a robust quality control system to monitor the assembly process and maintain product quality.
4. Train the Assembly Workforce
Invest in training sessions for the workforce involved in assembly to ensure they are skilled and knowledgeable about the components they are working with.
Frequently Asked Questions (FAQ)
What is the difference between SKD and CKD?
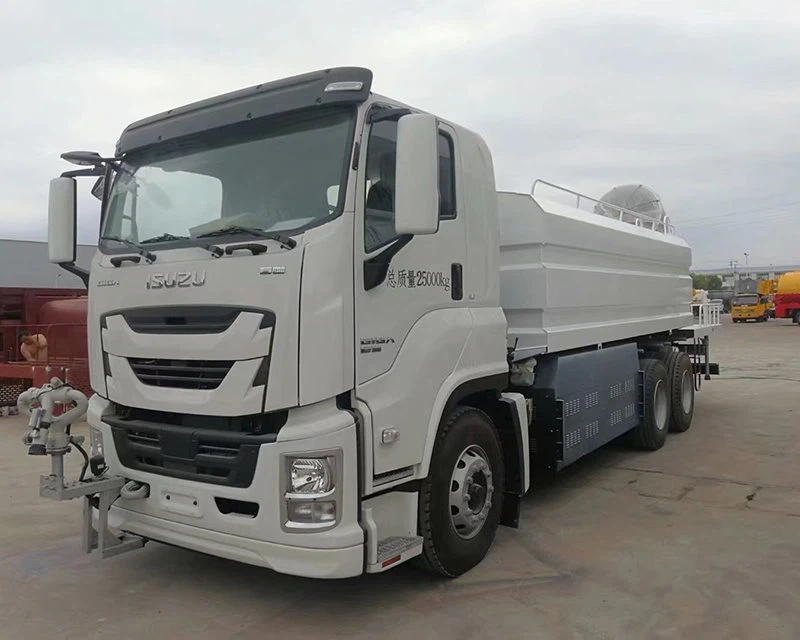
SKD (semi knock down) refers to products that are partially assembled and shipped in a more compact form, while CKD (completely knocked down) products are fully disassembled for shipping and require complete reassembly.
What industries benefit the most from SKD?
The automotive, furniture, and electronics industries are among the top sectors that benefit from utilizing semi knock down techniques.
Are there any risks associated with SKD?
Yes, risks include potential quality control issues, the necessity for skilled labor, and challenges related to customer assembly experience.
How can companies ensure successful assembly of SKD products?
Companies can guarantee success by providing thorough assembly manuals, conducting workforce training, and establishing a quality control system.
Is SKD a sustainable option?
Yes, since SKD reduces shipping volume and optimizes logistics, it can contribute to lower carbon footprints associated with transportation.
What are the logistics considerations for SKD shipments?
Logistics considerations include transportation costs, packaging design, and ensuring the safe arrival of components for efficient assembly.