Concrete mixer trucks play a vital role in the construction industry, transporting concrete efficiently to various job sites. Understanding the intricate details of these vehicles, particularly what’s inside a concrete mixer truck, can provide valuable insights for both professionals and enthusiasts. This article delves deep into the components, operation, maintenance, and advantages of concrete mixer trucks.
1. How Concrete Mixer Trucks Work
Concrete mixer trucks are specialized vehicles designed to transport and mix concrete while ensuring it remains workable. Their core function relies heavily on their unique structure and equipment.
1.1 Structure of a Concrete Mixer Truck
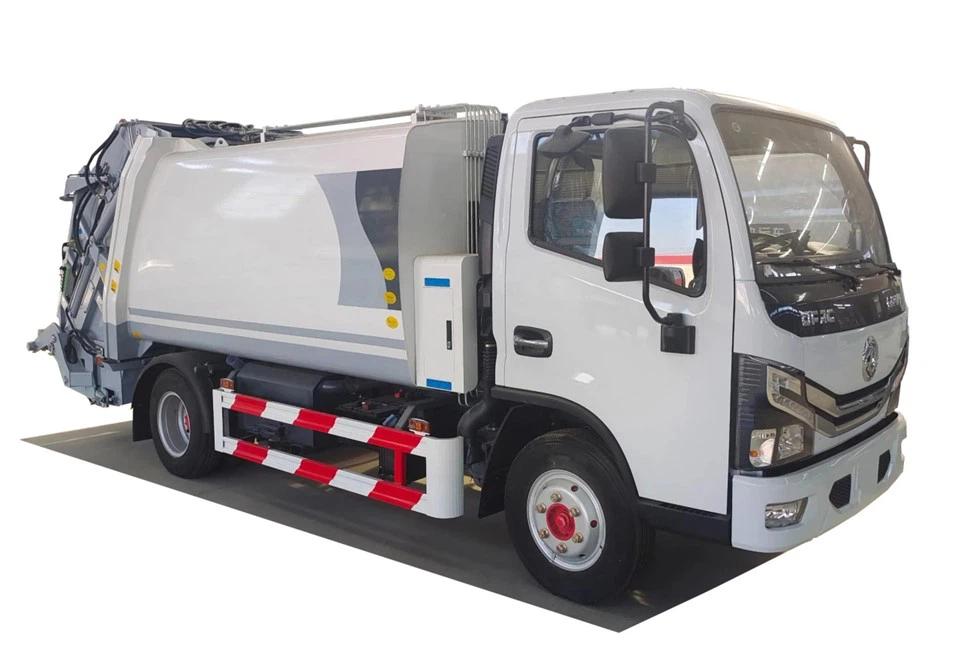
The truck consists of several key components:
- Chassis: The base frame that supports the entire truck.
- Mixing Drum: The cylindrical part where concrete is mixed and stored.
- Water Tank: Provides additional water to the concrete mix when required.
- Control Panel: Allows the driver to control the mixing process.
- Discharge Chute: Channels the concrete from the drum to the desired location.
1.2 The Mixing Process
The mixing process starts with the ingredients—cement, water, sand, and aggregates—loading into the drum. The drum rotates to mix the components thoroughly. The speed and direction of the drum rotation can also be controlled to ensure optimal mixing quality.
2. Components of a Concrete Mixer Truck
A concrete mixer truck consists of numerous components that work together efficiently:
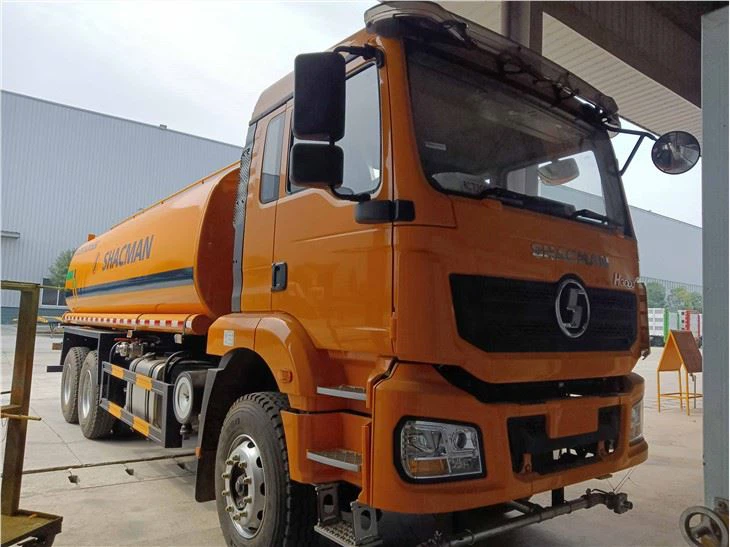
2.1 The Mixing Drum
The heart of the mixer truck, the mixing drum, is designed to keep concrete agitated and prevent it from hardening. The interior has spiral blades that mix the components uniformly.
2.2 Chassis and Cab
The chassis includes the truck’s frame, wheels, and engine, while the cab houses the driver’s controls and seating. Most mixer trucks have enhanced suspensions to support heavy loads.
2.3 Hydraulic System
The hydraulic system powers the drum’s rotation and enables the discharge of concrete. It allows for precise control of the mixing process and ensures smooth operation.
2.4 Water Supply System
A water tank is crucial for adjusting concrete consistency. It allows operators to add water during transit to ensure the mix remains workable without compromising the concrete’s integrity.
3. Different Types of Concrete Mixer Trucks
Concrete mixer trucks come in various types, each serving specific needs in construction:
3.1 Transit Mixers
Transit mixers are the most common type, featuring a rotating drum that keeps the concrete mixed while in transit.
3.2 Batch Mixers
Batch mixers prepare concrete in batches before loading it into transit mixers, suitable for large construction projects.
3.3 Volumetric Mixers
These mixers offer on-site mixing capabilities, allowing for the adjustment of concrete mix ratios according to the project requirements.
4. Benefits of Using Concrete Mixer Trucks
Concrete mixer trucks provide numerous advantages over traditional mixing methods.
4.1 Efficiency in Transportation
These trucks can transport large quantities of mixed concrete to various sites, significantly reducing transportation time.
4.2 Quality Control
Onboard mixing reduces the risk of environmental contamination and ensures that the concrete retains its intended properties during transport.
4.3 Versatility
Concrete mixer trucks can efficiently handle different types and grades of concrete, ideal for various construction projects.
5. Maintenance of Concrete Mixer Trucks
Proper maintenance is vital for the longevity and efficiency of concrete mixer trucks. Regular care ensures optimal performance and reduces maintenance costs.
5.1 Daily Maintenance Checks
Drivers should conduct daily inspections, which include:
- Checking fluid levels (oil, water, hydraulic fluid);
- Inspecting tire pressure and tread;
- Inspecting belts and hoses for signs of wear;
- Ensuring the mixing drum and discharge chute are clean.
5.2 Scheduled Maintenance
Following the manufacturer’s schedule for servicing is essential. This typically includes:
- Oil changes and filter replacements;
- Hydraulic system checks;
- Inspection of the mixing drum wear;
- Brake system maintenance.
6. Tips for Operating Concrete Mixer Trucks
For operators and drivers, following practical tips can enhance both safety and performance:
6.1 Safe Driving Practices
- Familiarize yourself with the truck’s dimensions and weight limits;
- Practice defensive driving to mitigate risks on the road;
- Maintain a safe distance from other vehicles.
6.2 Effective Loading Techniques
When loading concrete mix, ensure even distribution within the drum to maintain balance and prevent tipping.
6.3 Monitoring Mix Consistency
Regularly check the consistency of the concrete during transit and make adjustments with the water supply system as necessary.
7. Environmental Considerations for Concrete Mixer Trucks
With growing concerns about environmental impacts, the concrete industry is evolving:
7.1 Reducing Carbon Footprint
Many mixer trucks now utilize alternative fuels and technologies to minimize emissions.
7.2 Sustainable Materials
Promoting the use of environmentally friendly materials in concrete production can lower the overall ecological impact.
8. Innovations in Concrete Mixer Truck Technology
The concrete industry is embracing technological advancements to enhance operations and efficiency:
8.1 Telemetry Systems
Modern mixer trucks are equipped with telemetry systems that allow real-time monitoring of the mix’s condition and location.
8.2 Automated Controls
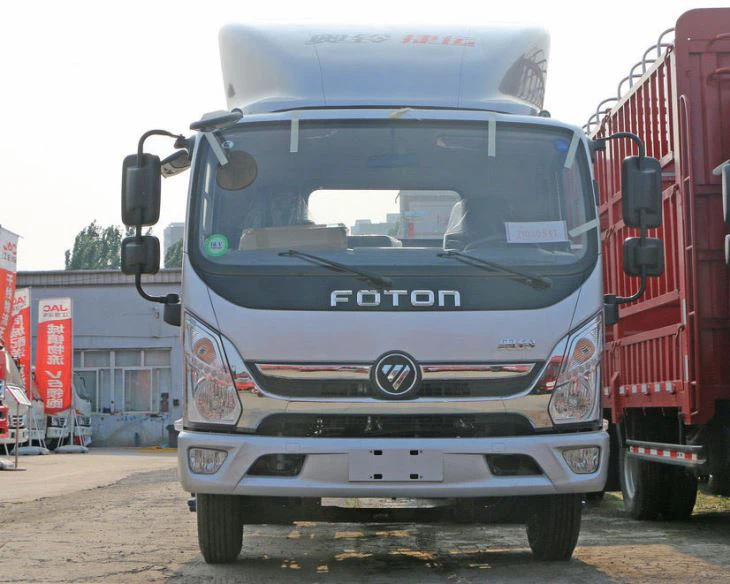
Automation in controlling the mixing process enhances precision and reduces human error during operations.
9. Common Misconceptions About Concrete Mixer Trucks
Despite their widespread use, several misconceptions persist:
9.1 Misconception: All Mixer Trucks Are the Same
There are significant differences between transit, batch, and volumetric mixers that cater to different project needs.
9.2 Misconception: Maintenance Is Not Necessary
Regular maintenance is crucial to prevent breakdowns and prolong the lifespan of the vehicle.
10. Frequently Asked Questions (FAQ)
10.1 What is the capacity of a concrete mixer truck?
The average capacity of a concrete mixer truck ranges from 6 to 12 cubic yards, depending on its size and model.
10.2 How long can concrete remain in a mixer truck?
Concrete should ideally be used within 90 minutes after mixing, but maintaining the drum’s rotation helps keep it workable for a longer period.
10.3 Can concrete mixer trucks operate in cold weather?
Yes, but precautions must be taken, such as using anti-freeze additives to prevent the concrete from freezing before it sets.
10.4 How can I ensure the concrete remains durable during transport?
Ensuring proper mix ratios and consistent monitoring during transport can help maintain concrete quality.
10.5 What safety measures should be in place when operating a mixer truck?
Proper training, wearing safety gear, and adhering to road safety regulations are crucial for operators’ safety.
10.6 Are there eco-friendly concrete mixer trucks?
Yes, some manufacturers offer mixer trucks that utilize alternative fuels, reducing emissions and environmental impact.