Introduction
Progress tanks are essential components in various industries, facilitating the effective management of different fluids and materials. Understanding how progress tanks operate and their applications can revolutionize workflows, reduce costs, and improve overall efficiency in operations. This comprehensive article delves into the definition, functionality, types, applications, advantages, and best practices associated with progress tanks. Whether you are an industry professional or a curious learner, this guide aims to provide valuable insights.
What is a Progress Tank?
A progress tank, also known as a settling or retention tank, is specifically designed for the treatment, observation, and management of liquids. These tanks can hold fluids, allowing for sedimentation and separation processes to occur, ensuring a clean and effective output. They are instrumental in various sectors, including water treatment plants, chemical processing facilities, and food production lines.
The Functionality of Progress Tanks
The primary function of a progress tank is to provide sufficient retention time for processes such as sedimentation, flotation, or chemical reactions. The tank’s design influences how effectively these processes occur. Here are the key functionalities:
- Separation of solids from liquids
- Storage of processed materials
- Regulation of flow rates in treatment systems
- Facilitating chemical reactions through controlled environments
Types of Progress Tanks
Understanding the types of progress tanks can help you choose the right one for your needs. Common types include:
1. Clarifier Tanks
Used for separating suspended solids from liquids, clarifier tanks enable sedimentation and are commonly found in wastewater treatment processes.
2. Flotation Tanks
These tanks complement clarifiers by using air bubbles to float solid particles to the surface for easy removal. They are also vital in mineral processing.
3. Digesters
Often used in waste treatment, digesters break down organic materials under anaerobic conditions, producing biogas as a byproduct.
4. Equalization Tanks
Equalization tanks help balance flow rates in treatment systems, receiving variable inflows and releasing a constant outflow, aiding in process stability.
Applications of Progress Tanks Across Industries
Progress tanks have diverse applications, and understanding these can enhance their implementation in various fields:
1. Wastewater Treatment
In wastewater treatment facilities, progress tanks play crucial roles in sedimentation and filtration processes to ensure clean output without contaminants.
2. Food and Beverage Processing
In the food industry, progress tanks are used for separating solids from liquids during the processing of products like juices, sauces, and dairy.
3. Mining and Mineral Processing
These tanks are employed in separating valuable minerals from waste materials through different methods like flotation and gravity separation.
4. Chemical Manufacturing
Progress tanks serve as reactors or settlers in chemical procedures, aiding in the mixing and reaction of various ingredients.
Advantages of Using Progress Tanks
Implementing progress tanks in your operations can yield significant benefits. Here are some advantages:
1. Improved Efficiency
Progress tanks facilitate optimal sedimentation and separation rates, resulting in faster and more efficient processes.
2. Cost-Effectiveness
By minimizing waste and optimizing resources, progress tanks can substantially reduce operational costs.
3. Enhanced Environmental Compliance
Progress tanks contribute to better waste management and treatment, helping industries adhere to environmental regulations.
4. Versatile Applications
The adaptability of progress tanks across various sectors makes them invaluable to industries with fluid management needs.
Design Considerations for Progress Tanks
When designing or selecting a progress tank, consider the following parameters:
1. Tank Size and Dimensions
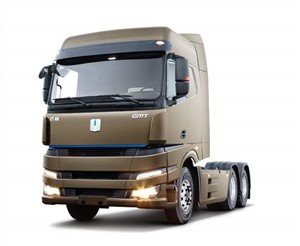
Calculate the necessary capacity based on inflow rates and intended retention time to ensure effective operation.
2. Material Selection
Choose materials that can withstand the specific chemical and physical conditions of the fluids involved.
3. Inlet and Outlet Configurations
Optimize the design of inlets and outlets to enhance flow dynamics and minimize turbulence.
4. Maintenance Accessibility
Design with accessibility in mind to facilitate maintenance tasks and inspections easily.
Practical Examples of Progress Tank Applications
Here are examples showcasing the effectiveness of progress tanks:
Example 1: Wastewater Treatment Plant
A local municipality utilizes clarifiers in their wastewater treatment plant. The clarifiers enable the separation of solids from the sewage, ensuring the water meets environmental discharge standards.
Example 2: Juice Production
A fruit juice manufacturing company uses flotation tanks to extract pulp from juice beverages. This not only enhances the product quality but also maximizes material recovery.
Example 3: Mining Industry
A mining company employs a flotation tank to separate valuable minerals from ore. The flotation process increases mineral recovery, thus improving profitability.
Best Practices for Maintaining Progress Tanks
Maintaining progress tanks is crucial for sustaining their efficiency and operating lifespan. Here are recommended best practices:
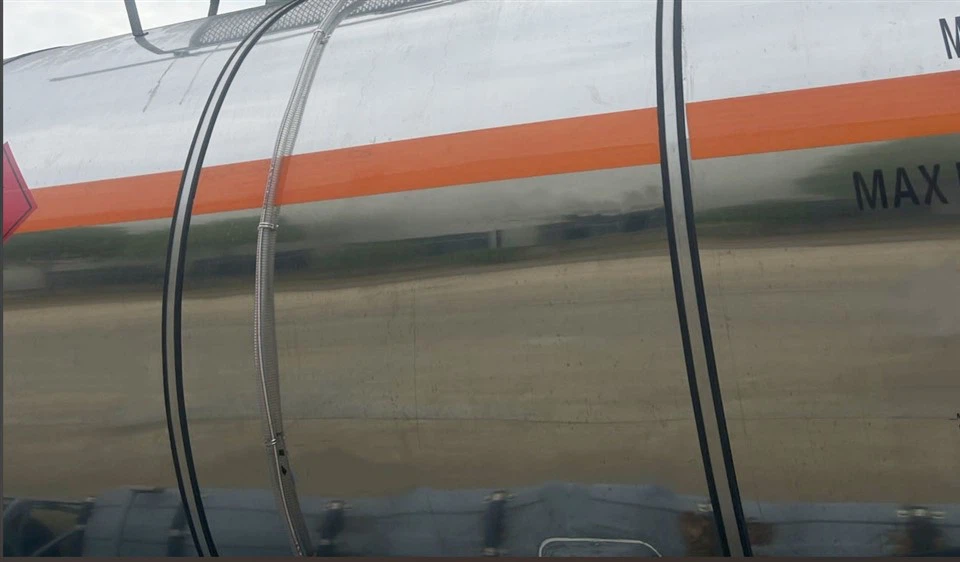
1. Regular Inspections
Conduct routine inspections of the tank and associated equipment. Look for signs of wear, corrosion, or blockage.
2. Scheduled Cleaning
Establish a cleaning schedule based on usage, which may vary from weekly to monthly, depending on the tank’s application.
3. Monitoring Flow Rates
Implement continuous flow monitoring to detect any irregularities that could indicate operational issues.
4. Staff Training
Ensure that operators are well-trained in the tank’s functionality and maintenance protocols to prevent mishaps.
Costs and Economic Consideration for Progress Tanks
The economic impact of progress tanks includes initial investment, operational costs, and potential savings. Understanding these factors is essential for decision-making.
1. Initial Investment
The cost of a progress tank can vary widely based on size, design complexity, and material choice. Assessing specifications is crucial to estimate total expenses.
2. Operational Costs
Factor in maintenance, cleaning, and monitoring frequency when calculating operational costs. Efficient tanks may have lower long-term expenses.
3. Return on Investment (ROI)
Evaluate the potential ROI by considering how progress tanks can enhance process efficiency and material recovery, reducing overall costs.
FAQ Section
1. What is the main purpose of a progress tank?
The main purpose of a progress tank is to facilitate the separation of solids from liquids, ensuring effective treatment and management of fluids.
2. How do I choose the right type of progress tank?
Choosing the right type of progress tank depends on your specific application, including the nature of the fluids involved and the desired outcomes of the process.
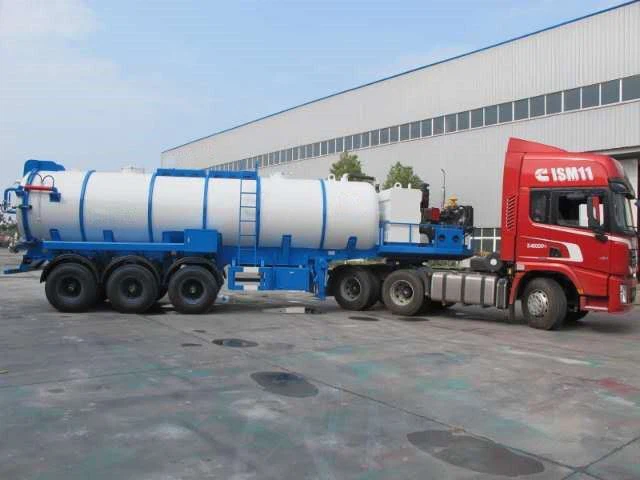
3. What maintenance is required for progress tanks?
Regular inspections, cleaning, and monitoring of flow rates are essential maintenance practices to ensure the optimal performance of progress tanks.
4. Can progress tanks be customized?
Yes, progress tanks can be customized based on specific operational requirements, including size, material, and design features.
5. What industries benefit most from progress tanks?
Industries such as wastewater treatment, food processing, mining, and chemical manufacturing benefit significantly from the use of progress tanks.
6. How does a progress tank improve environmental compliance?
Progress tanks enhance waste management processes, leading to better treatment and reduced environmental impact, thus helping industries meet regulatory standards.