Introduction
A tanker semi is a specialized type of trailer designed for transporting liquids, ranging from water to petroleum products. With a unique structure and function, tanker semis play a crucial role in various industries, enabling the safe and efficient movement of liquids over long distances. This guide will explore everything you need to know about tanker semis, including their types, primary functions, and practical tips for their operation and maintenance.
What is a Tanker Semi?
A tanker semi, often seen on highways and roads, consists of a tractor unit coupled with a semi-trailer. The semi-trailer is equipped with a tank that holds liquid cargo. Unlike standard flatbed or dry van trailers, tanker semis are specifically engineered to minimize the risk of spills and contamination, ensuring that the transported liquids remain safe and secure during transit.
History of Tanker Semis
The concept of liquid transportation dates back to the early 20th century when simple metal containers were used to move oil and other liquids. Over the years, advance in engineering and technology led to the development of more sophisticated tanker semis, enhancing safety and efficiency.
How Tanker Semis Work
When using a tanker semi, the liquid is stored inside the tank, which is mounted on the frame of the trailer. The tank’s design allows for even weight distribution, crucial for maintaining balance during transport. Tankers are typically equipped with a manhole for loading and unloading the liquid, along with various valves and pumps to facilitate this process.
Types of Tanker Semis

1. Food Grade Tankers
Food grade tankers are specifically designed to transport consumable liquids, such as milk, juice, and even wine. These tanks are constructed from materials that comply with health regulations and are easy to clean to prevent contamination.
2. Chemical Tankers
Chemical tankers transport various hazardous and non-hazardous chemicals. They have additional safety features to avoid leaks and spills, including specialized coatings and pressure relief systems.
3. Fuel Tankers
Fuel tankers are used to transport petroleum products, including diesel and gasoline. These tankers are usually compartmentalized, allowing for the transport of different grades of fuel in a single trip.
4. Milk Tankers
Milk tankers are designed for dairy transportation, equipped with insulation and refrigeration to maintain the freshness of the product during transit. They are typically stainless steel, preventing contamination and ensuring compliance with health standards.
5. Water Tankers
Water tankers cater to the transportation of bulk water supplies, often used in construction, agriculture, and municipal services. These tankers vary in size and configuration, accommodating different volume requirements.
6. Vacuum Tankers
Vacuum tankers are specialized vehicles designed to suck out liquid waste or sludge. They are frequently used in industries such as sewage treatment, septic tank cleaning, and hazardous waste removal.
Key Components of a Tanker Semi
1. Tank
The tank is the core component of a tanker semi, built to handle the specific type of liquid being transported. Tanks can be cylindrical or oval in shape, with varying sizes depending on the transport requirements.
2. Chassis
The chassis is the framework that supports the tank and houses crucial components such as axles and tires. A sturdy chassis ensures stability and adds to the overall safety of the vehicle during travel.
3. Valves and Hoses
Valves control the flow of liquid in and out of the tank, while hoses facilitate loading and unloading operations. High-quality hoses are essential to prevent leaks and maintain safety standards.
4. Safety Equipment
Safety equipment, such as fire extinguishers, spill kits, and warning devices, are crucial for tanker semis. Compliance with local regulations often dictates the type and quantity of safety equipment required.
5. Monitoring Systems
Modern tanker semis may include monitoring systems that track the liquid levels in the tank, pressure, and other crucial parameters to ensure safe transit.
Factors to Consider When Choosing a Tanker Semi
1. Type of Liquid
The type of liquid you intend to transport significantly influences your choice of tanker semi. Each type of tanker is designed to handle specific properties and safety requirements associated with different liquids.
2. Size and Capacity
Consider the required capacity for your operations. Tankers come in various sizes, and selecting one that matches your transport needs can minimize costs and maximize efficiency.
3. Regulatory Compliance
Ensure that the tanker semi meets all local and international regulations concerning the transport of hazardous materials, food-grade substances, and environmental protection.
4. Cost of Ownership
Evaluate not only the purchase price of the tanker semi but also additional costs such as insurance, maintenance, and fuel efficiency, which can significantly impact your total investment.
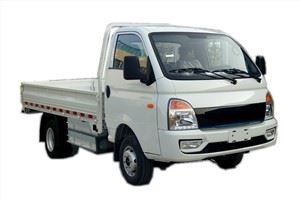
Tip: Research thoroughly and compare different models and their operating costs to find the best option for your business.
Tank Semi Operations and Maintenance
1. Daily Inspections
Conduct daily inspections to ensure that all components of the tanker semi are functioning correctly. Check for leaks, signs of wear, and proper operation of safety equipment.
2. Cleaning Requirements
Regular cleaning of the tanker is essential, especially for food grade and chemical tankers. Develop a cleaning schedule that complies with industry regulations and ensures thorough sanitation.
3. Maintenance Schedule
Implement a regular maintenance schedule that covers inspections, repairs, and part replacements. Collaborate with professional mechanics who specialize in tanker semis to ensure optimal performance.
4. Training Operators
Training the drivers and operators of tanker semis is critical. Proper training ensures safety and efficiency, reducing risks associated with liquid transport.
Tanker Semi Use Cases
1. Fuel Distribution
Tanker semis are integral to fuel distribution systems, supplying gas stations and industrial clients with petroleum products efficiently.
2. Transporting Food Products
Food grade tankers facilitate the movement of consumables, such as milk and juices, ensuring safety and compliance with health standards.
3. Chemical Supply Chain
In the chemical industry, tanker semis transport essential chemicals used in manufacturing processes, hazardous waste, and more.
4. Emergency Services
Fire departments often utilize water tankers to transport large quantities of water to areas affected by fire or drought, demonstrating the versatility of tanker semis.
Technological Advances in Tanker Semis
1. GPS Tracking
Modern tanker semis increasingly utilize GPS tracking systems, allowing operators and customers to monitor the location and status of shipments in real-time.
2. Advanced Safety Features
New technologies, such as spill monitoring and automatic shut-off valves, enhance safety and compliance with increasingly strict regulations governing liquid transport.
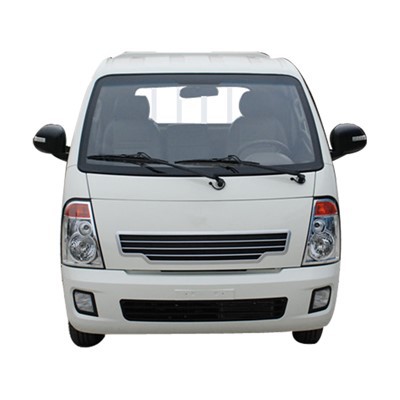
3. Eco-Friendly Innovations
With a focus on sustainability, some manufacturers are developing tankers made from recycled materials or integrating biofuel systems to reduce environmental impact.
Frequently Asked Questions (FAQ)
What is the average lifespan of a tanker semi?
The average lifespan of a tanker semi is typically between 10 to 15 years, depending on usage, maintenance, and environmental conditions.
How do you ensure the safety of transported liquids?
Maintaining safety involves regular inspections, adhering to regulations, employing qualified operators, and using appropriate safety equipment always.
What should I consider when loading a tanker semi?
Factors to consider include the weight distribution, tank capacity, type of liquid, temperature requirements, and proper sealing of valves and hoses.
Can I transport hazardous materials in a tanker semi?
Yes, you can transport hazardous materials, but you must comply with local and international regulations and ensure the tanker is equipped with necessary safety features.
What are the maintenance costs associated with tanker semis?
Maintenance costs can vary widely based on usage, but on average, you might expect to spend around 10-15% of the purchase price annually on maintenance and repairs.
Is it better to buy or lease a tanker semi?
This largely depends on your business needs. Buying has long-term benefits, while leasing can reduce initial costs and provide flexibility in managing assets.