Introduction
Diesel engines serve as a critical component in various sectors including transportation, construction, and power generation. When it comes to operating in confined spaces like tunnels, the dynamics change significantly. The performance, emissions, and safety protocols surrounding diesel engines in tunnels become paramount due to the unique challenges posed by limited ventilation and confined spaces. This article explores the intricacies of diesel engines used in tunnels, examining their operational benefits, safety measures, environmental impacts, practical examples, and much more.
The Basics of Diesel Engines
What is a Diesel Engine?
A diesel engine is an internal combustion engine that operates using diesel fuel. Unlike gasoline engines, which use spark plugs for combustion, diesel engines rely on compression to ignite the fuel. This makes them more efficient and often more powerful than their gasoline counterparts.
Types of Diesel Engines
- Two-Stroke Diesel Engines
- Four-Stroke Diesel Engines
- Turbocharged Diesel Engines
- Supercharged Diesel Engines
Diesel Engines in Tunnel Applications
Common Uses of Diesel Engines in Tunnels
Diesel engines find a range of applications in tunnel settings:
- Construction Equipment: Used for excavators, drills, and trucks.
- Emergency Power Generation: Provides backup electricity in case of power failure.
- Ventilation Systems: Powering fans and air circulation systems.
- Transportation: Diesel trains and service vehicles.
Performance Characteristics
Diesel engines are known for their durability and high torque output, which make them suitable for heavy-duty tasks in tunnels. Their ability to run continuously without overheating is another advantageous feature. However, it is notable that performance can be impacted by factors such as fuel quality, altitude, and engine maintenance.
Challenges of Using Diesel Engines in Tunnels
Ventilation Concerns
One of the primary challenges of using diesel engines in tunnels is the requirement for effective ventilation. The combustion process produces carbon monoxide and other harmful pollutants, necessitating adequate air flow to mitigate health risks for workers and passengers.
Effective Ventilation Strategies
Some effective ventilation strategies include:
- Natural Ventilation: Utilizing air shafts and tunnel openings.
- Mechanical Ventilation: Installing exhaust systems and fans.
- Periodic Monitoring: Conducting air quality assessments to ensure safe environments.
Emissions and Environmental Impact
Diesel engines emit various pollutants, including nitrogen oxides (NOx) and particulate matter (PM), that can pose serious health risks in confined spaces. Regulations and standards have been established globally to limit these emissions, urging the adoption of cleaner technologies.
Emissions Reduction Technologies
Advancements in technology for emissions reduction include:
- Selective Catalytic Reduction (SCR): A process that reduces NOx emissions using a catalyst.
- Exhaust Gas Recirculation (EGR): Redirecting a portion of engine exhaust back into the combustion chamber.
- Particulate Filters: Devices that capture soot and other particulates from exhaust gases.
Safety Protocols for Diesel Engine Operations in Tunnels
Standard Safety Measures
Safety is a top priority in tunnel operations. Some essential safety measures include:
- Regular Maintenance Checks: Ensuring the engine and equipment are in top condition.
- Fire Safety Equipment: Installing fire extinguishers and alarms along tunnel routes.
- Emergency Protocols: Establishing clear evacuation procedures and training workers.
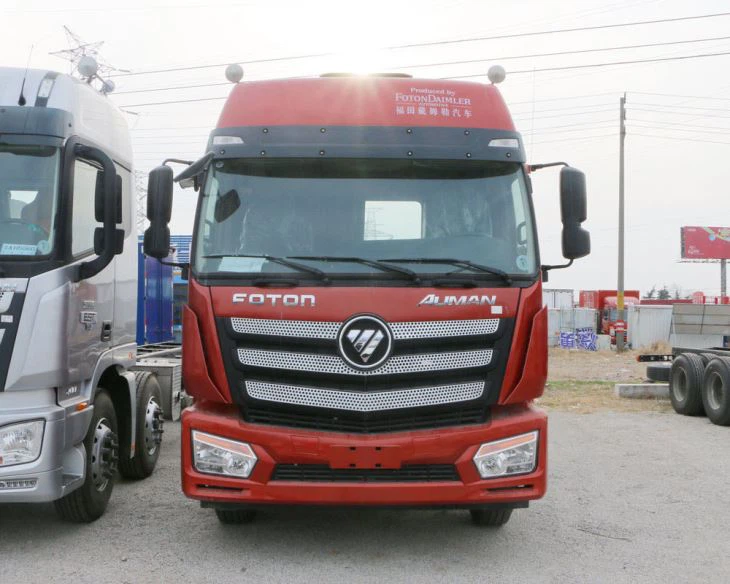
Monitoring Systems
Utilizing monitoring systems can provide real-time data related to air quality and engine performance, which can be crucial for maintaining safety and compliance.
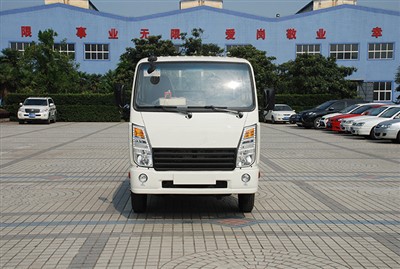
Types of Monitoring Technologies
Technology | Description |
---|---|
Air Quality Monitors | Devices that measure levels of CO, NOx, and particulate matter. |
Engine Telemetry Systems | Systems that track engine performance metrics remotely. |
Emergency Alarm Systems | Systems that alert workers of dangerous conditions. |
Practical Examples of Diesel Engines in Tunnel Projects
Case Study: Urban Rail Tunnel Projects
Urban rail projects often utilize diesel engines for construction equipment and temporary power generation. For example, during the construction of the Crossrail project in London, diesel-powered excavators played a pivotal role in tunneling beneath the city.
Case Study: Road Tunnels
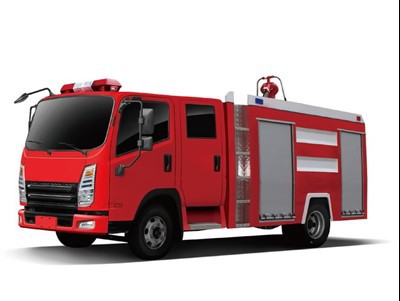
In road tunnel construction, diesel engines are crucial for both construction equipment and service vehicles. The tunnels’ ventilation systems are often powered by diesel generators, ensuring continuous airflow.
Lessons Learned from Tunnel Projects
Key lessons from these projects include:
- Investing in advanced ventilation systems can mitigate safety risks.
- Regular maintenance and monitoring of diesel engines reduce downtime.
- Utilizing cleaner diesel technologies can significantly cut emissions.
Best Practices for Diesel Engine Operation in Tunnels
Regular Maintenance and Inspections
Implementing a regular maintenance schedule is essential for ensuring the efficiency and reliability of diesel engines. Routine checks should focus on:
- Oil and filter changes
- Fuel system inspections
- Exhaust system evaluations
Training for Tunnel Operations Personnel
Providing detailed training for personnel operating diesel engines in tunnels is crucial. Topics should cover:
- Engine operation and troubleshooting
- Understanding emissions and their health impacts
- Emergency response procedures
Future of Diesel Engines in Tunnel Applications
Advancements in Engine Technology
The future of diesel engines in tunnels appears to shift towards hybrid technologies, integrating electric power with traditional diesel systems to reduce emissions and improve efficiency. This shift could lead to a decrease in environmental impact while maintaining performance.
Regulatory Trends
As governments increasingly prioritize environmental sustainability, diesel engines are facing stricter emissions standards. The adoption of alternative fuels and cleaner technologies is becoming a necessity rather than an option for tunnel operators.
FAQs about Diesel Engines in Tunnels
1. Why are diesel engines commonly used in tunnels?
Diesel engines are favored because of their high torque, durability, and capacity for continuous operation, making them ideal for heavy machinery and power generation in tunnels.
2. What are the main safety concerns associated with diesel engines in tunnels?
Key safety concerns include carbon monoxide emissions, potential fire hazards, and the need for adequate ventilation to ensure a safe working environment.
3. How can emissions from diesel engines in tunnels be reduced?
Emissions reduction can be achieved through advancements such as selective catalytic reduction (SCR), exhaust gas recirculation (EGR), and particulate filters, which help capture harmful pollutants.
4. What are effective ventilation strategies in tunnel operations?
Effective strategies include natural ventilation through shafts, mechanical ventilation using fans, and continuous air quality monitoring to ensure safety.
5. How often should diesel engines used in tunnels be maintained?
Diesel engines should be maintained regularly, with inspections typically scheduled every 100-200 hours of operation, or as recommended by the manufacturer.
6. Are there alternatives to diesel engines for tunnel operations?
Yes, there are alternatives, including electric and hybrid engines. These options help reduce emissions and environmental impact, especially as technology advances.