Introduction
The transportation of gas via tankers plays a crucial role in the global energy market. Gas tanker capacity is a key factor influencing shipping operations, trade volumes, and even pricing strategies. In this article, we will delve into the various aspects of gas tanker capacity, including definitions, types of tankers, industry standards, and practical considerations for businesses and individuals involved in gas transportation. Our goal is to provide a detailed overview that demystifies the subject and aids in understanding its importance in the energy sector.
What is Gas Tanker Capacity?
Gas tanker capacity refers to the volume of gas that a tanker can transport safely and efficiently. This capacity can vary significantly based on the type and size of the tanker, as well as the nature of the gas being transported. Understanding tanker capacity is essential not only for shipping companies but also for suppliers, traders, and regulatory bodies.
Types of Gases Transported
Gas tankers typically transport various types of gases, including:
- Liquefied Natural Gas (LNG)
- Liquefied Petroleum Gas (LPG)
- Compressed Natural Gas (CNG)
Liquefied Natural Gas (LNG)
LNG is natural gas that has been cooled to a liquid state, making it easier to store and transport. It is commonly used for power generation and residential heating.
Liquefied Petroleum Gas (LPG)
LPG consists mainly of propane and butane and is used for cooking, heating, and as fuel for vehicles.
Compressed Natural Gas (CNG)
CNG is natural gas that is compressed to less than 1% of its volume at standard atmospheric pressure, primarily used as a fuel for vehicles.
Capacity Measurement Units
Gas tanker capacity is measured in several units, depending on the type of gas and the conventions used in the industry.
Cubic Meters (m³)
The most common unit for measuring gas tanker capacity is cubic meters. It represents the volume of gas the tanker can hold.
Metric Tons
For liquefied gases like LNG and LPG, capacity may also be measured in metric tons, reflecting the weight of the gas when liquefied.
Key Factors Influencing Tanker Capacity
Several factors impact the capacity of gas tankers, including:
Tanker Design
The design of the tanker itself greatly influences its capacity. Different designs cater to specific types of gas and operational requirements, such as:
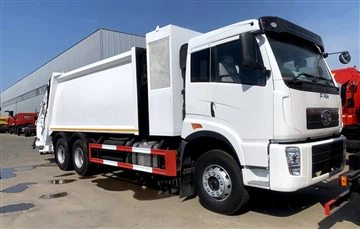
- Membrane tanks for LNG
- Spherical tanks for LPG
Regulatory Standards
Regulatory bodies impose standards for the construction and operation of gas tankers. These standards can affect tank capacity and safety protocols.
Environmental Considerations
Increasingly stringent environmental regulations also play a role in the design and capacity of gas tankers. Tankers must adhere to laws to minimize emissions and prevent leaks.
Market Demand
Global gas demand can fluctuate, influencing how much gas tankers are designed to carry. Shipping companies often adjust their fleets based on market trends.
Types of Gas Tankers
Gas tankers come in various types, tailored to the specific requirements of the gas being transported.
Medium-Size LNG Carriers
These carriers typically hold between 125,000 to 175,000 cubic meters of LNG, commonly used for regional transport routes.
Large LNG Carriers
These massive tankers can carry over 200,000 cubic meters of LNG, ideal for long-haul international shipping.
Pressurized LPG Carriers
LPG carriers are designed to transport liquefied petroleum gas at high pressure, generally having capacities between 30,000 and 80,000 cubic meters.
Small Scale Gas Carriers
These vessels are smaller in size and usually designed for transporting gas to regions without access to large-scale infrastructure.
Gas Tanker Loading and Unloading Procedures
Understanding the procedures for loading and unloading gas tankers is crucial for safety and efficiency.
Loading Procedures
Loading gas onto a tanker involves various steps:
- Pre-loading checks to ensure safety and equipment readiness.
- Connecting loading arms or hoses to the tanker.
- Monitoring temperature and pressure during the loading process.
Unloading Procedures
Unloading typically follows these stages:
- Connecting unloading equipment to the receiving terminal.
- Monitoring gas transfer, including temperature and pressure.
- Post-unloading inspections to check for leaks or equipment failure.
Economic Impact of Gas Tanker Capacity
The capacity of gas tankers can significantly impact the economics of the energy market.
Trade Volumes
A higher tanker capacity allows for the transportation of larger volumes of gas, which can lead to reduced shipping costs per unit of gas transported.
Price Fluctuations
As supply chains become more efficient due to larger tankers, prices may stabilize, benefiting both producers and consumers.
Investment in Infrastructure
Increased tanker capacities often necessitate upgrades to ports and handling facilities, creating new opportunities for investment and growth in the shipping industry.
Challenges in the Gas Tanker Industry
While the gas tanker industry has seen significant advancements, it also faces several challenges.
Safety Risks
Transporting gas poses inherent risks, including potential leaks, explosions, and environmental consequences. The industry must constantly evolve its safety protocols.
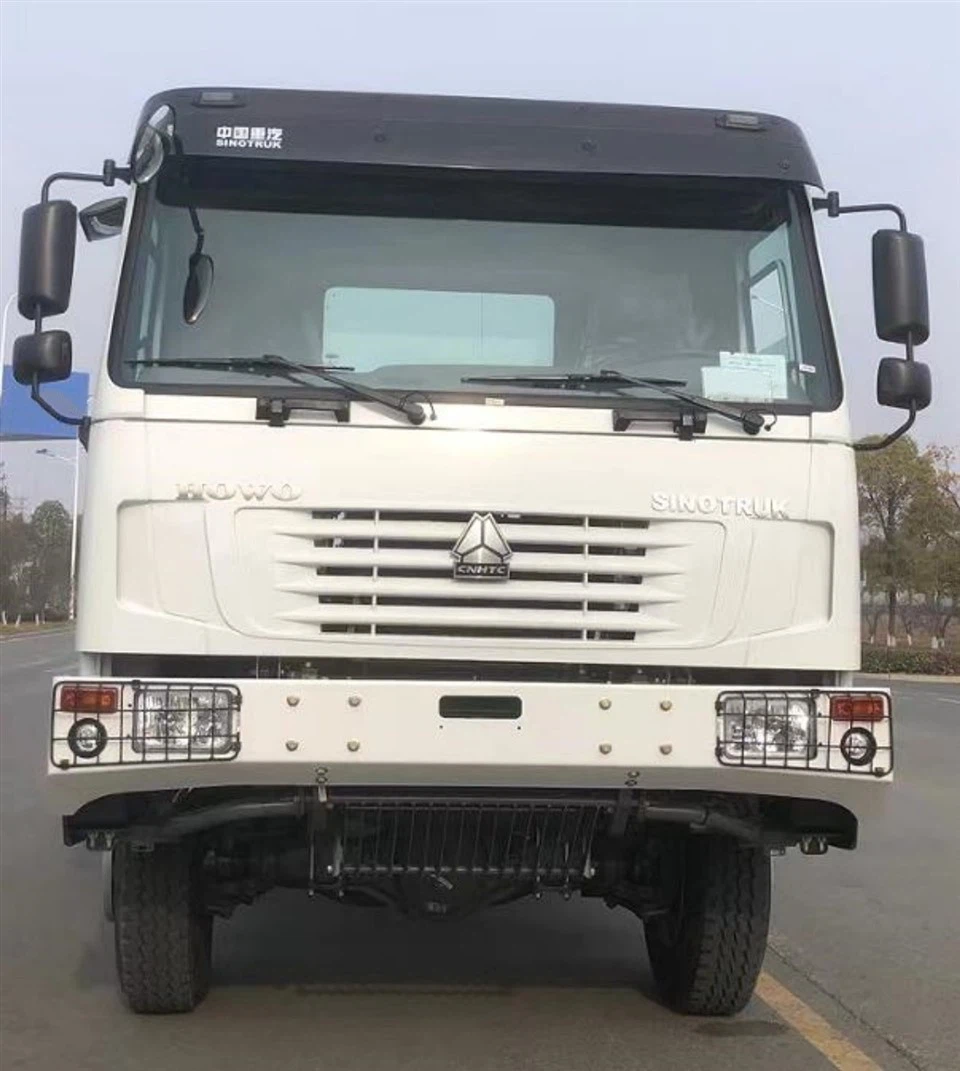
Regulatory Compliance
Keeping up with shifting regulatory requirements can be challenging for operators, necessitating ongoing training and investment.
Market Volatility
The global gas market can be volatile, influenced by geopolitical events, shifts in energy policy, and emerging technologies.
Future Trends in Gas Tanker Capacity
The future of gas tanker capacity is shaped by several emerging trends.
Technological Innovations
Advancements in technology are leading to more fuel-efficient tankers with improved monitoring systems, enhancing safety and operational efficiency.
Sustainability Initiatives
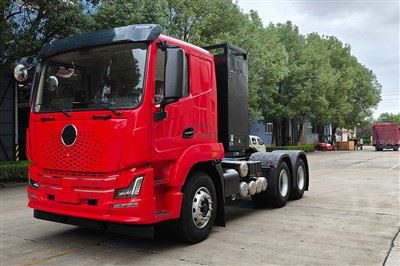
As environmental concerns escalate, the industry is focusing on reducing carbon emissions and exploring alternative fuels for tankers.
Emerging Markets
Growth in emerging markets presents new opportunities for gas transportation as demand for energy continues to rise.
Practical Examples and Tips for Businesses
If you’re involved in the gas tanker industry, considering the following tips can help optimize your operations:
Evaluate Transport Needs
Understand your specific gas transportation needs to choose the right tanker size and design.
Stay Informed on Regulations
Regularly review and comply with evolving industry regulations to mitigate risks and ensure safe operations.
Invest in Training
Provide thorough training for your staff to ensure they are well-versed in safety protocols and operational procedures.
Utilize Technology
Incorporate advanced monitoring and management technologies to enhance operational efficiency and reduce waste.
FAQs about Gas Tanker Capacity
What is the average capacity of a gas tanker?
The average capacity of gas tankers varies greatly depending on the type; for example, LNG carriers typically range from 125,000 to over 200,000 cubic meters.
What types of gas can be transported by tankers?
Gas tankers can transport various gases, including liquefied natural gas (LNG), liquefied petroleum gas (LPG), and compressed natural gas (CNG).
How does tanker capacity affect shipping costs?
A larger tanker capacity can lead to reduced shipping costs per unit of gas, making distribution more economically viable.
What safety measures are in place for gas tankers?
Safety measures for gas tankers include rigorous pre-loading inspections, pressure monitoring during transit, and post-unloading checks to identify leaks.
How are gas tankers loaded and unloaded?
Gas tankers are loaded and unloaded through specialized equipment that connects to loading arms or hoses, ensuring safe transfer while monitoring conditions like pressure and temperature.
What is the impact of gas tanker capacity on global trade?
Gas tanker capacity directly impacts global trade by influencing trade volumes, shipping routes, and pricing strategies, ultimately affecting market dynamics.