The logistics and transportation industry has seen significant advancements over the years, with various tools and technologies emerging to improve efficiency and productivity. Among these, west coast loaders play a crucial role in streamlining the loading and unloading process of various goods along the western coast of the United States. This article delves into the significance, types, and efficiency of west coast loaders, providing insights and practical examples to help you understand their importance in today’s fast-paced world.
What Are West Coast Loaders?
West coast loaders refer to a range of loading equipment and machinery utilized in ports and warehouses along the western coastline of the United States. They are critical for shifting large volumes of goods, including containerized cargo, bulk materials, and automobiles. These loaders enhance operational efficiency, reduce turnaround times, and ultimately save costs across supply chains.
The Evolution of Loaders
Historically, loading and unloading cargo was a labor-intensive process that required many workers to manage heavy goods. With the advent of technology and mechanization, loaders were developed to automate and expedite these processes. The evolution from manual labor to automated machinery transformed the logistics industry, ultimately leading to increased productivity.
Major Milestones
- 1900s: Introduction of forklifts and basic loaders.
- 1960s: Enhanced designs and capabilities (e.g., containerization).
- 1980s: Rise of automated guided vehicles (AGVs).
- 2000s: Adoption of intelligent technology in loaders.
Types of West Coast Loaders
There are various types of loaders commonly employed along the west coast, each tailored for specific tasks or types of cargo. Here are some of the prominent types:
1. Forklifts
Forklifts are perhaps the most recognizable type of loader, used for lifting and transporting materials over short distances. They come in various sizes and capacities, making them versatile for different applications.
Characteristics
- Types: Electric, diesel, and LPG forklifts.
- Load Capacity: Ranges from 1,500 to over 10,000 pounds.
- Use Cases: Warehousing, shipping yards, and construction sites.
2. Telehandlers
Telehandlers, or telescopic handlers, offer extended reach and versatility for loading, unloading, and placing materials at height.
Characteristics
- Special Features: Telescoping boom for reaching heights.
- Load Capacity: Typically between 5,000 to 12,000 pounds.
- Use Cases: Construction, agriculture, and heavy material handling.
3. Wheel Loaders
These machines are designed for heavy lifting and material handling on construction and industrial sites.
Characteristics
- Versatile: Suitable for digging, transporting, and grading.
- Load Capacity: Ranges significantly depending on the model.
- Common Settings: Mining, gardening, and road construction.
4. Container Loaders
Specifically designed for loading and unloading shipping containers, these loaders are crucial in port operations.
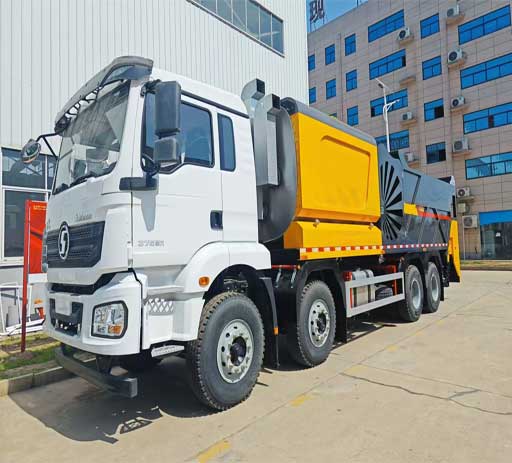
Characteristics
- High Lifting Capacity: Can handle large and heavy containers.
- Efficient: Reduces the time spent in port.
Benefits of Using West Coast Loaders
Companies along the western coast can experience numerous benefits from integrating modern loaders into their operations. Here are some key advantages:
1. Increased Efficiency
Loaders significantly speed up the loading and unloading processes. For example, the time taken to unload a shipping container can decrease from hours to just minutes with the use of a specialized container loader.
2. Enhanced Safety
Modern loaders come equipped with safety features that minimize accidents at work sites. Forklifts with automatic shutoff systems ensure that excessive load is not carried, reducing potential hazards.
3. Cost-Effectiveness
By optimizing loading operations, businesses save money on labor costs and improve overall productivity. Companies like UPS and FedEx often report millions in savings through enhanced loader efficiency.
4. Environmental Benefits
Electric loaders and advancements in eco-friendly technologies help reduce emissions, making logistics operations more sustainable. Choosing electric forklifts can reduce a company’s carbon footprint significantly.
Practical Examples of West Coast Loaders in Action
The role of west coast loaders can be seen in various operations across the western United States. Here are some notable examples:
1. Port of Los Angeles
As one of the busiest ports in the nation, the Port of Los Angeles employs state-of-the-art gantry cranes and straddle carriers that automate the loading of shipping containers.
2. Seattle-Tacoma International Airport
Operator firms at SEA use specialized loaders for handling baggage and cargo, enhancing turnaround times for flights due to efficient loaders managing high-volume deliveries.
Tips for Choosing the Right Loader
When selecting a loader for your logistics operation, consider the following tips to ensure you make the best decision:

1. Assess Load Capacity Needs
Determine the maximum weight and dimensions of the materials you will be handling. This ensures that the loader can manage your cargo without strain or risk of an accident.
2. Evaluate the Environment
Consider where the loader will be used—indoors, outdoors, or both. For example, outdoor operations may require wheel loaders that can function efficiently on uneven terrain.
3. Look for Safety Features
Prioritize loaders equipped with advanced safety features like sensors, alarms, and automatic shutoff capabilities to protect operators and workers.
4. Opt for Energy Efficiency
Choose environmentally friendly machines like electric forklifts whenever possible, as these can lead to savings on energy costs and reduced emissions.
Future Trends in Loader Technology
The future of west coast loaders is shaping up to be influenced by trends in automation, data analytics, and sustainability. Here are some expected developments:
1. Automation and Robotics
Automated loaders and robots for material handling will likely become commonplace, reducing the need for human operators.
2. IoT Integration
The integration of the Internet of Things (IoT) will enable real-time monitoring of loaders, improving maintenance schedules and load management.
3. Sustainability Advances
As companies continue to seek greener solutions, innovations in battery technology and electric models will define the next generation of loaders.
FAQ Section
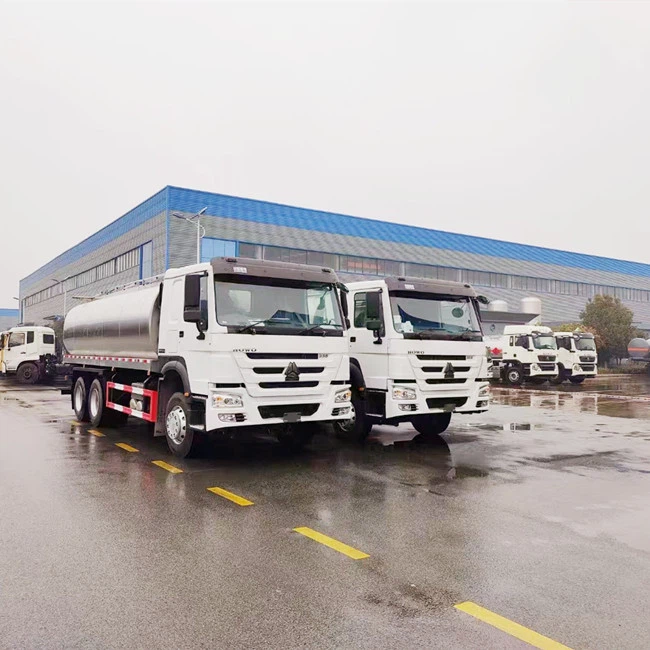
1. What types of loads can west coast loaders handle?
West coast loaders can handle a variety of loads, including shipping containers, bulk materials, and heavy construction equipment, depending on the specific type of loader used.
2. Are electric loaders as powerful as traditional loaders?
Yes, many electric loaders are designed to rival their diesel counterparts in terms of load capacity and power while offering the added benefit of reduced emissions.
3. How do I choose the right loader for my warehouse?
To choose the right loader, assess factors like load capacity, usage environment, and necessary safety features. Consult with suppliers to find the best options for your needs.
4. Can loaders be rented instead of purchased?
Yes, renting loaders is a common practice, especially for companies that need equipment seasonally or for specific projects without the long-term commitment of a purchase.
5. What safety measures should be taken when operating loaders?
Operators should undergo proper training, conduct daily inspections, use helmets, and follow manufacturer guidelines to enhance safety while operating loaders.
6. How can I reduce loader downtime in my operations?
Regular maintenance, timely repairs, and using IoT technology for predictive maintenance can help reduce loader downtime and keep operations running smoothly.